Obtain news and background information about sealing technology, get in touch with innovative products – subscribe to the free e-mail newsletter.
27.09.2022 Press Release
Stormproof
The highest wind velocity ever measured in the German North Sea was 191 km/h (119 mph). While wind turbines erected in the ocean are shut down even at considerably lower wind speeds, the structures still have to withstand the enormous force of a hurricane, no matter what – and this throughout their entire service life. The foundation that anchors the towers in the seabed plays an important role in this. In the shallow waters predominant in the North and Baltic Seas, it is usually constructed by means of so-called “monopiles”. These are steel piles driven into the seabed until only the upper ends are above the water surface. The tower, which even for a 10-megawatt turbine can reach a height of 150 meters (493 ft) to the rotor hub, is usually not mounted directly on the piles but supported by a connecting piece, a flange. This flange is attached with several dozen bolts that become inaccessible for any maintenance once the tower is installed. To prevent the screw connections from corroding in the harsh environment at sea, they have to be protected against the ingress of moisture. Today, seals from Freudenberg Sealing Technologies are already handling this crucial task in more than 800 offshore wind turbines.
Important advantage of double-row design
The most important function is performed by a ring seal at the top of the pile: It encloses the interior part of the linking piece that supports the screw connection. In modern installations, this flange seal with the abbreviation MP-TP (monopile transition piece) can reach a diameter of eight to ten meters. Freudenberg Sealing Technologies has also offered this seal in a double version in recent years. The main advantage of the double-row design is the resulting redundancy, as Freudenberg expert Manuel Hille explains: “If minor damage occurs at one of the two seals during the transport or installation, the function is still ensured. In addition, this makes it possible to optimally combine different designs and materials with each other.” However, the specific design is almost exclusively customer-specific in order to make optimum use of the available assembly space. Freudenberg also offers an already established standard product upon request.
In a conventional design, a gap remains between the lower end of the connecting piece and the pile. One or two ring seals interspersed with air chambers designed as elastic breakwaters ensure that no seawater can enter. On the other hand, if the gap is filled with cement, a ring seal can keep the cement in the desired position during the curing and later protect it against damage from saltwater. Maintenance platforms, which are often positioned above the water surface inside the monopile, can additionally be protected against ingress of gases with a specially designed seal. These kinds of gases may form due to biological seawater processes in the pile.
Designed for long life
There has been a sharp increase in the expected service life of components used for sea-based wind turbines in recent years. While 25 years were initially considered a good lifespan, this standard has now risen to up to 35 years. Such a long operating life can’t be ensured by means of bench tests. This is why Freudenberg is using an adapted Arrhenius algorithm to extrapolate the results of six-week intensive stress tests. This quite familiar procedure, named after the Swedish chemist and Nobel laureate Svante August Arrhenius, has been consistently refined by Freudenberg experts in recent years. They significantly improved the service life model by coupling chemical and physical effects with the structural mechanical behavior of the material.
“80 percent of all currently projected marine wind farms are based on monopile technology,” estimates Marcel Schreiner, who oversees sales in the energy sector at Freudenberg Sealing Technologies. “This is an important growing market for us.” In the expert’s view, the trend towards ever larger systems – nominal capacities of 20 megawatts are under discussion for 2030 – also speaks in favor of paying particular attention to the service life when selecting components.
Freudenberg Sealing Technologies will also be showcasing the MP-TP seals at its booth B6.531 at the WindEnergy 2022 trade fair in Hamburg (Germany). In addition, other products such as Seventomatic S95 for oil-lubricated main shaft bearings, piston accumulators for pitch control of wind turbines and seals for electrolysers will be on display. At the same booth, Klüber Lubrication and Freudenberg Performance Materials will also present their latest products and developments specifically for the wind energy industry.
Ulrike Reich
Head of Media Relations & Internal Communications
Telephone: + 49 (0) 6201 960 5713
ulrike.reich@fst.comCheryl Eberwein
Director, Corporate Communications
Telephone: +1 734 354 5373
cheryl.eberwein@fnst.comDownload Press Release
Download Images
News Service
You can subscribe to the Freudenberg Sealing Technologies news alert service, bringing you the news as soon as they are published. You can always unsubscribe from this service.
Subscribe now!Further Articles With These Taggings
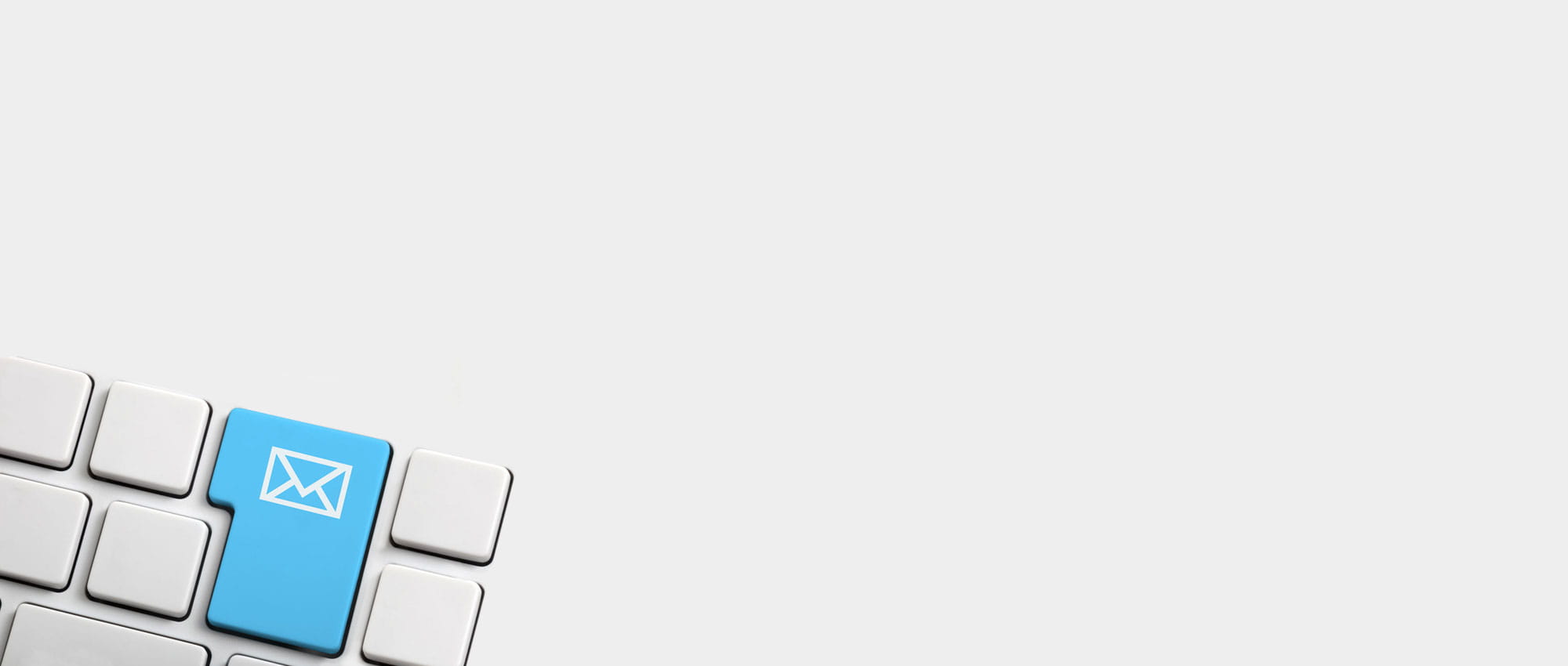
News Service
You can subscribe to the Freudenberg Sealing Technologies news alert service, bringing you the news as soon as they are published. You can always unsubscribe from this service.
Subscribe now!