Obtain news and background information about sealing technology, get in touch with innovative products – subscribe to the free e-mail newsletter.
10.07.2024 | News
Who Do You Trust, When the Line Is Down?
When a wood mill in the United States realized they didn’t have the O-rings they needed, they required a quick solution to restart their equipment.
Seals are often one of the most overlooked components within any equipment, so much so that they are often an afterthought. This sentiment holds true until a situation arises like a failure or a replacement part order if forgotten. Despite being overlooked, seals are essential with a single failure or ordering mishap that can shut your line down indefinitely until a replacement is in hand. This reality creates a nightmare for supply chain planners because a single mistake could result in unexpected downtime costing thousands of dollars of lost productivity every hour. While seals are out of sight in equipment, not forgetting these critical components can be a real headache because something as simple as a missing O-ring could shut you down. When a situation arises you need a partner with inventory and a customer-focused sense of urgency and flexibility to get the line restarted.
The Challenge
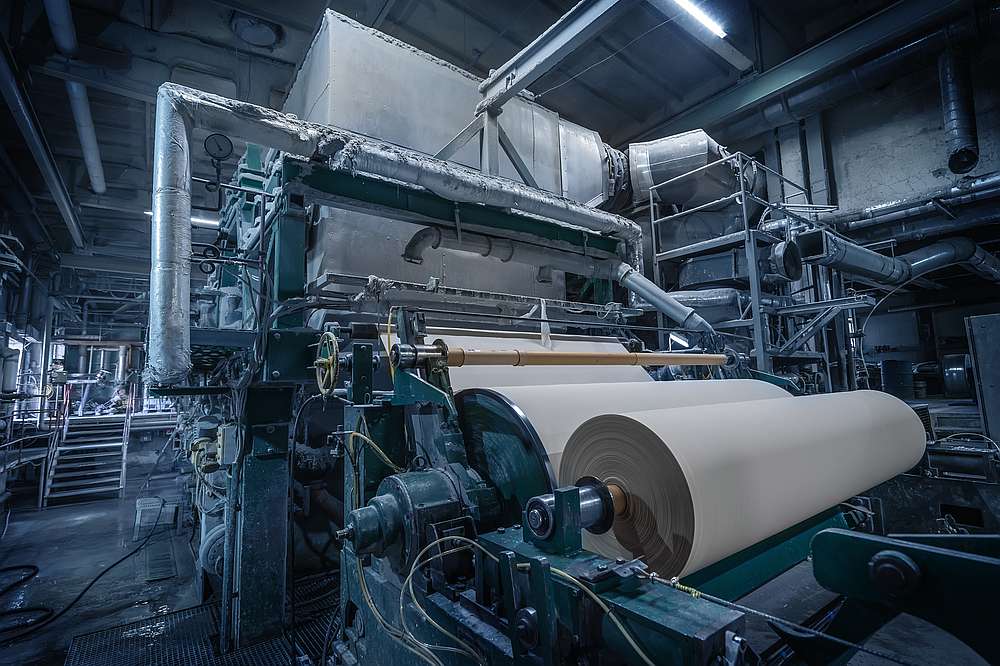
Around 4 pm central time, we received an urgent request from one of our United States distributors. One of their customers had frantically contacted them looking for NBR O-rings, which were needed for maintenance purposes. We had previously worked with the wood mill in the eastern United States, supplying them with Freudenberg brand Merkel® kits for their large industrial presses. This time was different, their maintenance made the mistake of forgetting to order the NBR O-rings before their planned shutdown to replace all the components. Unfortunately, they hadn’t realized they were missing the O-rings until the middle of the shutdown, after not finding the seals. They quickly realized their mistake and needed help urgently to get back operational quickly.
The Solution
Our team quickly looked up the O-rings they needed and saw we had the exact ones they needed in stock from our Houston, Texas facility. Within a matter of minutes, we provided pricing, and availability, and received the order approval from the distributor. “Before we had even received the order the wood mill was in the process of planning to fly someone to Houston as a carrier to pick up the O-rings and get them back to the facility” – Justin, Sales Engineer. Due to the timeframe, we reviewed with our customer service team if we could get this shipped out for overnight delivery. The biggest concern was the last truck leaves at around 5 pm central time making it very tight for our standard solutions. With the mill planning to send a courier, they requested we place the parts outside to pick them up, and they were willing to risk something happening to the seals.
Patrice our operations supervisor in Houston got involved at this point and decided “We are going to take care of the customer. I don’t feel comfortable leaving a product outside, where we can’t guarantee delivery. I will find another solution, that we can confirm successfully makes it to the customer.” We had requested a UPS drop box outside of our facility for nonstandard hours shipments similar to this. We called UPS and informed them that we have an urgent overnight shipment that needs to be picked up as soon as possible from the drop box tonight. We then picked the O-rings off the shelf, packaged them with the UPS label, and got them into the drop box.
The next morning, we kept a close eye on the tracking number to ensure it arrived. Thanks to the quick work from our team, the mill received the O-rings at 10:14 am Eastern time. This allowed them to quickly install the O-rings into their equipment and be back up and running that morning. While a $40 O-ring order might not seem like a big deal, to the mill it was critical because they were unable to run their business. The flexibility and dedication of our team to get the parts out and delivered across the country saved the mill thousands of dollars worth of lost productivity.
With well-stocked warehouses, and process improvements to have over 95% on-time delivery from our warehouses in Houston, Durham, and Shakopee combined with a dedicated team we are here to serve our customers and provide quick turnaround times for thousands of warehoused SKUs in North America. “We care about our customers, and making sure they have what they need when they need it. We are eager to support their business, this is just a perfect example of our dedication to the customer” – Mario, Sr Distribution Center Manager Houston. Whether you are line down or stocking up for a project months away, we have a solution and are ready to serve you with multiple warehouses around the globe and a highly motivated and customer-oriented team!
More news on the subject Industrial Applications
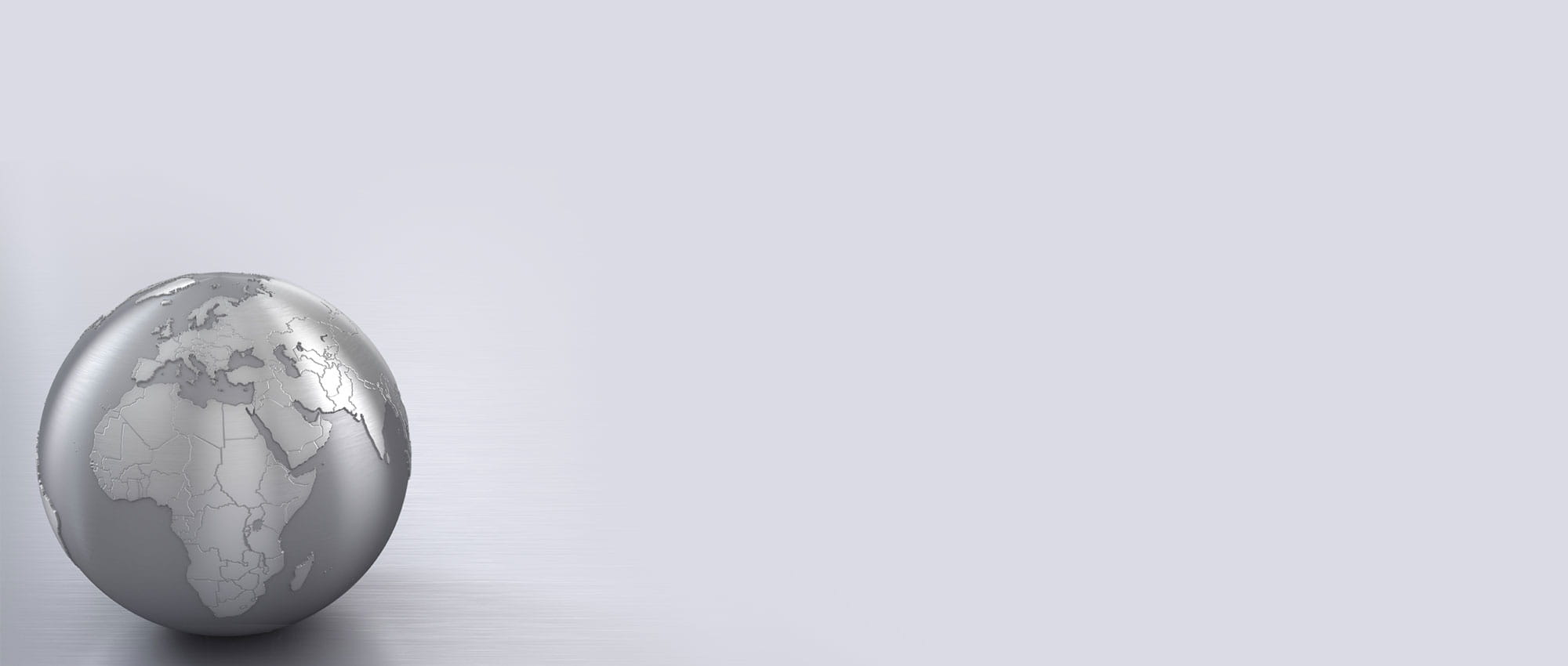
First Hand News
Best of all, keep up with the latest developments
with the Freudenberg Sealing Technologies newsletter.