Obtain news and background information about sealing technology, get in touch with innovative products – subscribe to the free e-mail newsletter.
21.02.2024 | News
Overcoming Seal Failures With Freudenberg EPDM 291 Material
Learn how a major US manufacturer in the health and well-being industry used Freudenberg EPDM 291 material to solve their sealing failures while delivering considerable cost-saving.
Sealing failures aren’t only a major headache, they can be extremely costly when you consider replacement costs, lost production time, wasted product due to the risk of contamination, and the time spent by maintenance staff to find and replace the seal. Unfortunately, this can be a very common issue when you utilize the wrong seal for your equipment. With every application having unique requirements, it can be challenging to pick the right seal to reliably perform at a high level. A large global manufacturer that specializes in health and well-being enhancement products was having just this issue with regularly facing significant challenges with the seals of their centrifugal equipment.
Used to separate partials by their density from fluids, gases, and solids, this equipment spins incredibly fast typically at 100 to 200 plus revolutions per minute (RPMs). When the components inside the centrifuge move at this speed in a circular path it creates inertia i.e. the force needed to separate compounds of different densities. Centrifuges are a very commonly used piece of equipment often found in the food & beverage space for applications in dairy, juices, breweries…etc., biodiesels, and applications such as this in the pharmaceutical/medical space.
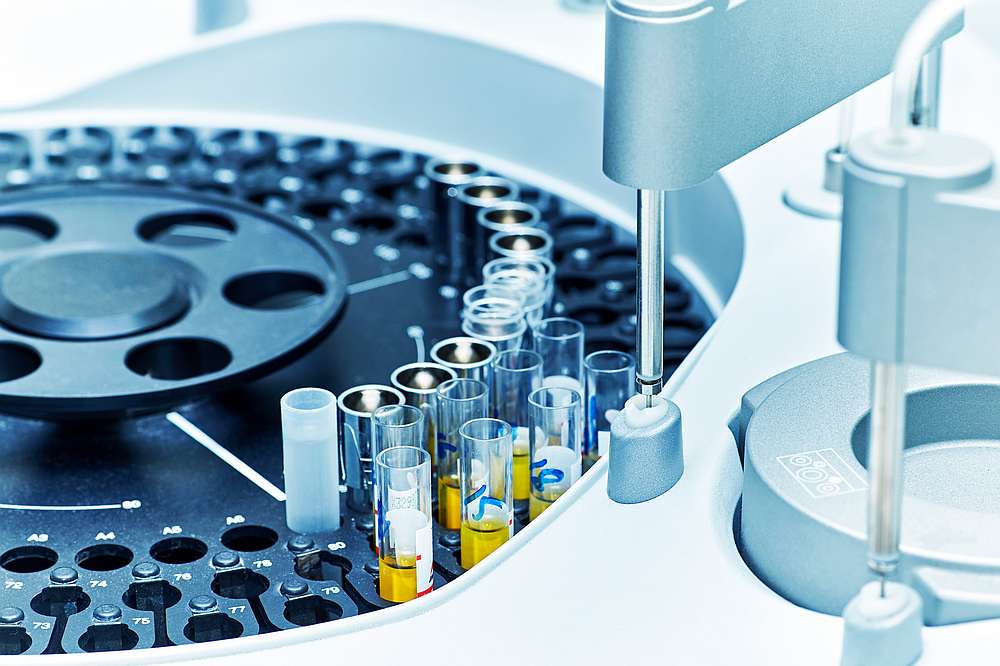
The Challenge
Centrifuges are quite demanding applications for seals because of the combinations of temperatures, media, and their incredibly quick speeds of rotation that create a significant amount of force that is used to separate particles. The manufacturer was experiencing regular seal failures causing untimely downtime to repair the seals. Originally they reached out to the supplier of the equipment to purchase OEM replacement kits, which turned out to be quite expensive and were subject to long lead times resulting in additional downtime that prevented them from recapturing lost revenue. With a single seal failing causing the line to go down and requiring the ordering of an entire new OEM replacement kit, this became incredibly costly especially when you consider the equipment typically costs $100,000 to $1 million or more to purchase.
The Solution
After continued struggles, the manufacturer reached out to one of our distributors in the United States who quickly recruited the support of our experts. As a first step, our team conducted a detailed analysis to understand the application and the unique requirements of how they were utilizing their equipment.
Once completed our team put together a full package that includes standard-sized Freudenberg brand EPDM 291 O-rings, kits, and custom O-rings made of EPDM 292 by Freudenberg Xpress®. We also took one large O-ring and created a custom square-ring to prevent spiral failure. These parts were FDA-compliant and retrofitted perfectly into the manufacturer’s centrifuge equipment. Our team was quickly able to provide these standard and custom machined O-rings, all while ensuring a quick reliable supply of seals from our Durham, North Carolina facility for future needs.
The Results
Since the implementation of the custom EPDM 291 seals the manufacturer has seen a significant increase in the service life of their seals and no longer has line-down situations allowing for considerably improved productivity. Additionally, beyond the savings of longer service lives and increased production, they have also seen savings of almost $35,000 annually without the need to purchase overpriced OEM repair kits.
Our ability to solve challenging problems for customers has tremendous benefits to everyone as the customer receives more productivity and cost savings all while the distributor was able to win around $65,000 of new business because of our diverse solutions. Creating win-win situations like this is possible with our team at Freudenberg Sealing Technologies thanks to our sealing experts all with an extremely extensive portfolio of materials, seals, and services. We firmly believe we are better together and place a major emphasis on supporting our partners.
Our specialized EPDM materials help solve challenging situations for our customers every day. Think this might be the right solution for you? Leave your info below, and our sealing experts can support you in finding the perfect application for your unique needs!
More news on the subject Industrial Applications
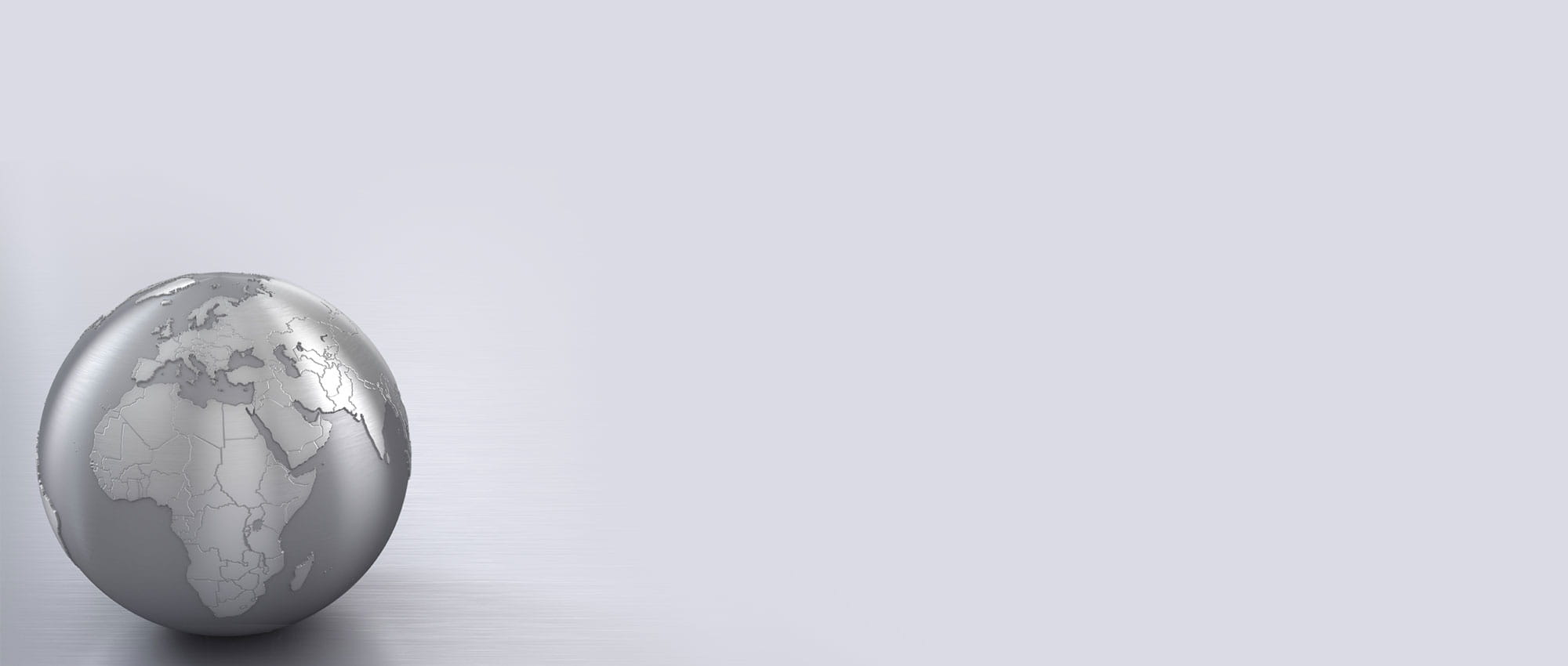
First Hand News
Best of all, keep up with the latest developments
with the Freudenberg Sealing Technologies newsletter.