Obtain news and background information about sealing technology, get in touch with innovative products – subscribe to the free e-mail newsletter.
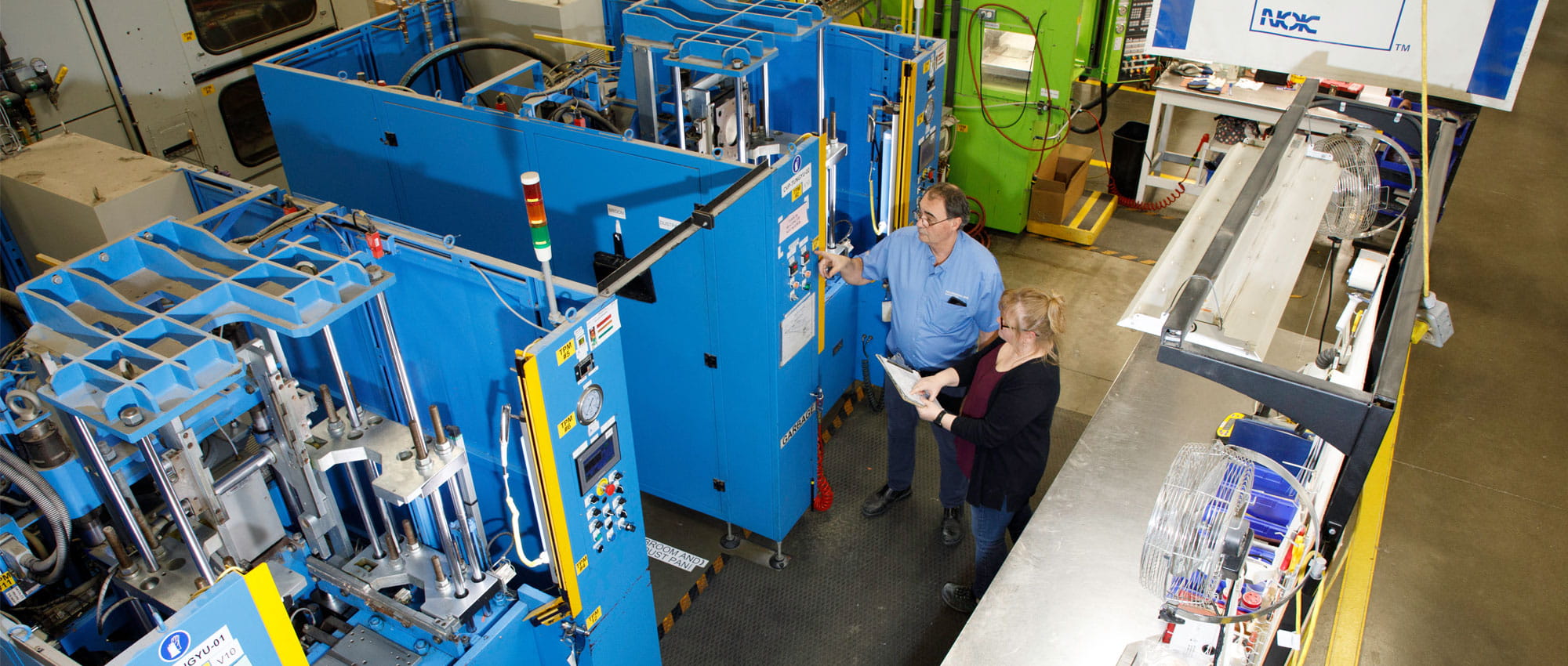
14.08.2023 | News
How Changes Today Can Impact Tomorrow
Our plant in Tillsonburg, Ontario, is focused on taking active strides to improve its emissions and energy consumption numbers of the facility.
Tillsonburg is located in the southwest of the Canadian province of Ontario, which has an abundance of natural resources. The city is not only home to more than 15,000 inhabitants - Freudenberg Sealing Technologies also manufactures a broad portfolio of specialty seals there with some 150 employees, ranging from a door seal for an airbus to a turbine seal or silicone rubber-coated fiberglass core rods for high-performance insulators used in power transmission and distribution systems worldwide.
As the most populous and manufacturing-heavy province in Canada, Ontario is also home to an abundance of natural resources. The combination of these two characteristics has led to the province dedicating itself to several sustainability goals to help keep the region thriving in a responsible way, including the goal of achieving CO2 neutrality before 2035 and Net Zero emissions by 2040.
Currently, the energy that powers Ontario is derived from a trio of sources, with approximately 51% coming from zero-emission nuclear power, 39% from hydroelectric power, thanks to the region’s abundance of waterways, and 10% from renewable resources (wind/ solar).
Located in Ontario, Freudenberg’s Tillsonburg facility is automatically powered via that combination of energy sources under the umbrella of the province’s sustainable energy initiatives. But even though the region provides an eco-aware backdrop, the staff at the facility is focused on taking active strides to improve its emissions and consumption numbers.
According to Terry Chute, Tillsonburg’s Health and Safety Manager, the facility is dedicated to not only maximizing the sustainable operational measures already in place but actively finding new ways to further improve.
“Based on Ontario’s energy mix, we come out pretty good on CO2 emissions as a whole,” Chute said. “But we were still being encouraged by the province to lessen the amount of electricity, overall, that we were using. Ontario was a little ahead of Freudenberg in terms of its goals, and this helped position us to respond to Freudenberg’s sustainability objectives when they were introduced in 2020.”
According to Chute, the team at Tillsonburg has undergone multiple efforts to improve energy reduction, beginning with taking the facility’s two cooling units and combining them into one.
Previously, the plant had two processing cooling systems, one for the LSR Molding cell and the other to cool the rest of the plant. This two-set arrangement not only doubled the cost of maintenance but also presented an additional energy cost. A plan was implemented to remove the LSR cell-dedicated chiller and connect the other to the main HVAC system to create one overall system.
This downsizing effort has not only reduced maintenance costs but also has allowed Tillsonburg to reduce its purchase of glycol, a type of antifreeze used in industrial refrigeration systems. As an additional sustainability measure, the plant now circulates the glycol that is used through the main air intake system, allowing waste heat to be reclaimed to heat the plant in the coldest months. The entire operation has lowered Tillsonburg’s heating costs.
Another effort taken at Tillsonburg was reducing the number of variable speed pumps onsite from four down to two. The original four pumps at the facility ran at 10HP and operated in a constant-on state no matter the amount of demand. They have since been replaced by two newer pumps that have the ability to run at a variable frequency based on demand specifics at 7.5HP.
In similar fashion, Chute and his team also removed the liquid-cooled compressor that had served as the backup unit for the plant’s main air compressor and upgraded it to GA22VSP variable speed air compressor. This upgraded setup allows for the heat that flows out of the compressors to be collected to help heat the adjoining tool shop, helping to keep electrical and heating costs down.
The system was also paired with product maintenance plan to prevent air leaks to keep it running efficiently, a vital part of the upgrade.
“Initiating these types of changes is an important step but without proper maintenance and oversight, you won’t get the results you’re aiming for,” said Chute. “Looking at these improvements from a full lifecycle perspective is key, not just from the initial implementation perspective.”
Tillsonburg implemented other sustainability activities, as well. By replacing all of the existing lights in the facility with LED lighting that included automatic off/on sensors, the plant cut its electricity usage by more than 259,000 KHW and is now realizing a $40,000 cost savings annually.
“While the initial investment in LED lighting does come with a cost, it more than pays for itself when used correctly in less than two years’ time,” said Chute.
Other improvement areas at the plant includes the reduction in size of the steam autoclave – which is the equipment system where parts and components manufactured onsite are cured – allowing it to use less steam to fill and maintain pressure during operation – and replacing the old fabric hand-cutters with equipment which has reduced material waste by nearly 20%.
Even with all these improvements, Chute says that Tillsonburg is still thinking ahead to what’s next in the effort to reduce emissions further and not rest on current achievements for too long.
“We’ve got more plans in process to further improve our HVAC, curing oven and boiler operations,” said Chute. “It’s important for us to look for ways to reduce across all of different areas of our facility. When you take the collective sum of all these efforts, it becomes clear what an impactful difference seemingly small actions can have over time.”
More Stories About Sustainability
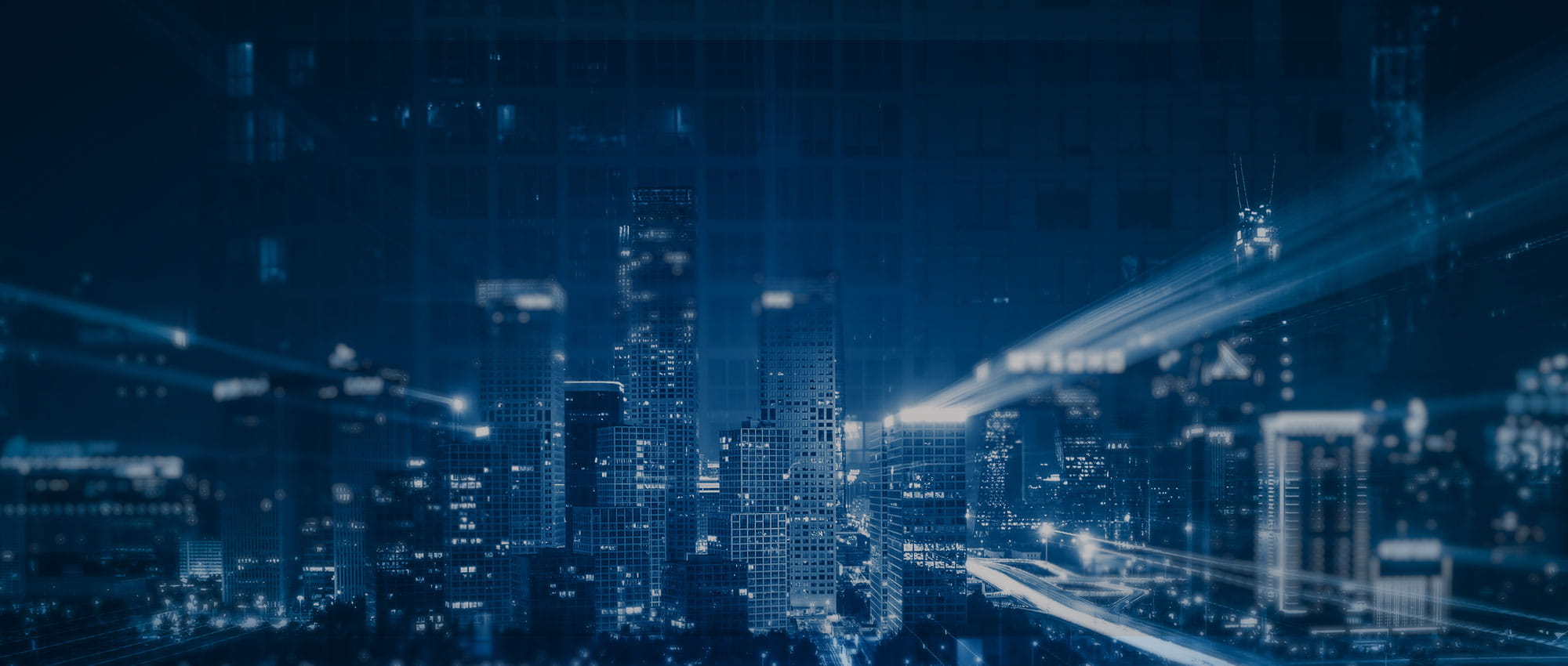
Join Us!
Experience Freudenberg Sealing Technologies, its products and service offerings in text and videos, network with colleagues and stakeholders, and make valuable business contacts.
Connect on LinkedIn! open_in_new