Obtain news and background information about sealing technology, get in touch with innovative products – subscribe to the free e-mail newsletter.

“Less In, Less Out”
Materials that are specially developed to meet the requirements of the food industry have turned out to be outstanding options for the pharmaceutical industry. By contrast, seemingly plausible ideas sometimes make little sense. An expert in the field, Mike Minow highlights the materials that are making headway in the medical field.
The clothing worn in many medical professions is white, in part because the color makes it easier to see contaminants. But Mike Minow, Global Key Account Manager for Freudenberg Process Seals, is surprised when he offers a white material to pharmaceutical manufacturers. It turns out that very few want it. “In black EPDM, we replaced the carbon black with silicates to create the white coloring,” Minow said. In reality, though, the color proved to be an obstacle. When the pharmaceutical industry uses black plastic, “medicine producers can see any detachment of particles in the product more easily,” he explained. And if necessary, they can discard an entire batch. For pharmaceutical companies, it is more economical to throw out contaminated batches than to have dirt particles in their products.
Insight into the pharmaceutical industry: Mike Minow, Global Key Account Manager at Freudenberg Process Seals.
Expensive End-Product
Thus, there are similarities and differences between the pharmaceutical and the food industries. Hygiene is a central concern for both. Even the smallest impurities are a problem. “The investments in the development of a pharmaceutical product are considerable,” Minow said. “That makes the end-products many times more expensive than those for the food industry.” Freudenberg Sealing Technologies has extensive experience with specialized products for the food and beverage sector. One thing has been clear for some time: Many of them can be successfully carried over to the pharmaceutical equipment and are an extremely good fit. And, for the most part, pharmaceutical companies are willing to invest in innovations because of their products’ price structures.
“When a batch of an already expensive end-product has to be destroyed, we are quickly talking about a half-million euro loss,” Minow said. That’s why the use of the right material is especially important. Seals in hygienically pure equipment have to withstand high temperatures and resist aggressive cleaning agents.
An Entirely New Material
One of these materials is Fluoroprene® XP. The blue material has a special status in the Freudenberg Sealing Technologies portfolio. “We designed it specifically for the food sector and then found that it also works for the pharmaceutical industry,” Minow said. “This is a material that had not been available on the market in its current form.” The development process originally focused on solving an issue in the food industry: Companies were looking for a material that totally blocked the transfer of flavors from one food product to another during production. “We were sure that there would be a basic need for this.”
Then the need grew greater than expected and came from other sectors like the pharmaceutical industry. Fluoroprene® XP is even more resistant to extreme temperatures than ethylene propylene diene monomer rubber, or EPDM. Fluoroprene® XP can be used at temperatures up to 200°C (392°F). A material that offered resistance to all other substances and that withstood high temperatures was completely unique. “That makes it overdesigned for some applications,” Minow admitted, but just right for many uses in the pharmaceutical industry.
As Little as Possible
Inside “The EPDM 291 version clearly has the highest sales at our company,” Minow said. The material is ideal for use in hygienically pure facilities. It is chemically resistant and especially sterile. Since sterility is so crucial to the industry, some manufacturers and pharmaceutical producers are experimenting with antibacterial plastics – even Minow and his team have thought about this. But this rather enticing idea has a catch: “You would be adding something to a tried-and-tested material,” he said. “And it is never clear what the effects will be.” In short, the pharmaceutical industry is sensitive to these issues and wants to avoid unnecessary risks. Instead, it can turn to a material proven to be ideal for the job.
It makes much more sense to design equipment from the outset without dead space where dirt can accumulate. “It is better to rely on hygienic design than on extra chemicals to correct for something that was not well-designed in the first place,” Minow pointed out. The goal would be to restrict inputs into the equipment as much as possible. That means “the less in, the less out” when it comes to materials.
Problem Solver and Intermediary
In the area of facility design, Freudenberg Sealing Technologies can be an intermediary between machine-builders and pharmaceutical manufacturers. “The two sides don’t always speak the same language,” Minow noted. An engineer’s bright idea could cause an unforeseen problem on the pharmaceutical side. “But we can often solve these problems,” he explained, “because we look at things from the standpoint of the material – in both directions.” This helps both sides. The machine-builder designs a better product, and the pharmaceutical company can produce its medicines more reliably.
“We have long experience with materials,” Minow added. High-quality products do have their price though. But in return, they can be traced back to the manufacturer. “That is especially important to smaller companies.” They are ready to spend money on that. The reason: Errors in production processes quickly become a question of survival for smaller suppliers. “The industry needs high-purity materials, traceability and guidance.” Freudenberg Sealing Technologies will continue to develop ideas, even if they may not be well-received in the market at first – like the white plastic. “Which, incidentally, is by no means a failure,” Minow concluded. It was precisely the right solution for some pharmaceutical producers’ special processes.
Learn more about sealing solutions for applications in the pharmaceutical industry.
This article originally appeared in ESSENTIAL, Freudenberg Sealing Technologies’ corporate magazine that covers trends, industries and new ideas. To read more stories like this, click here.
More Stories About Technology
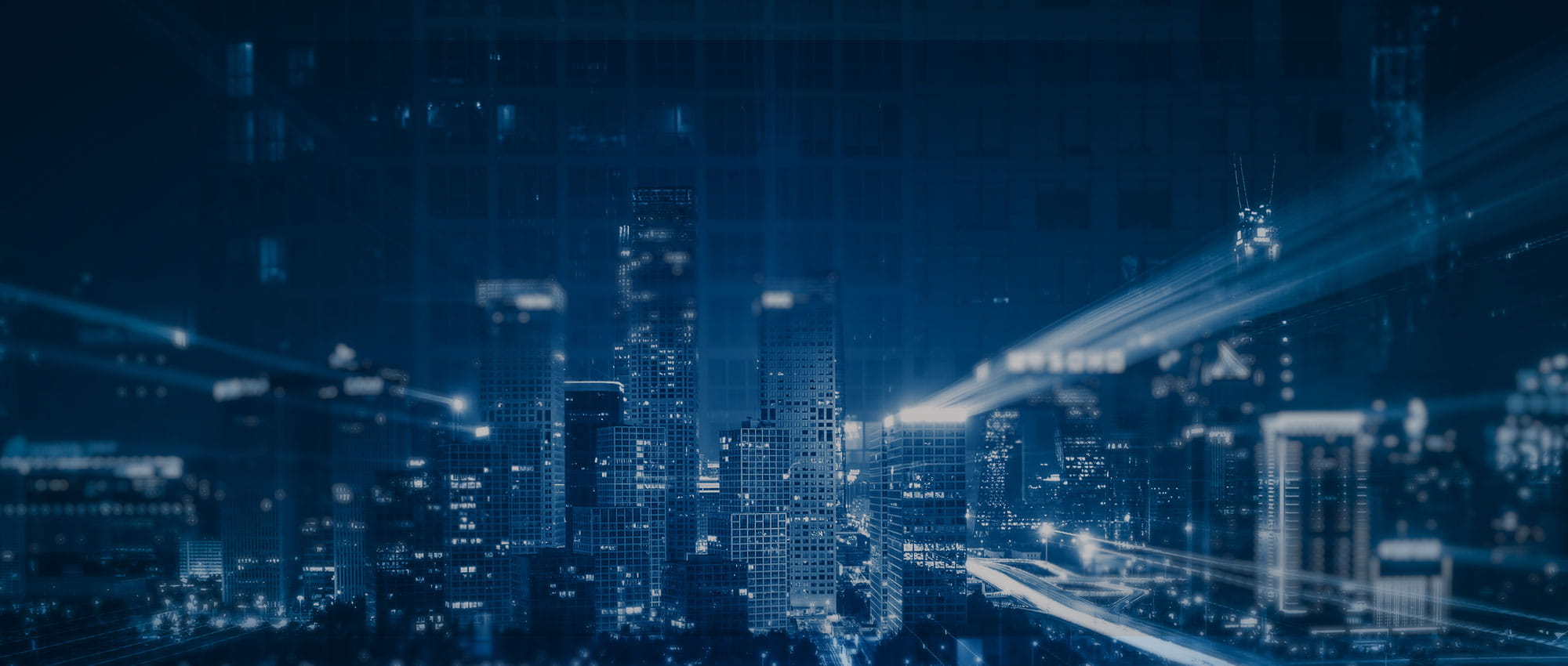
Join Us!
Experience Freudenberg Sealing Technologies, its products and service offerings in text and videos, network with colleagues and stakeholders, and make valuable business contacts.
Connect on LinkedIn! open_in_new