Obtain news and background information about sealing technology, get in touch with innovative products – subscribe to the free e-mail newsletter.
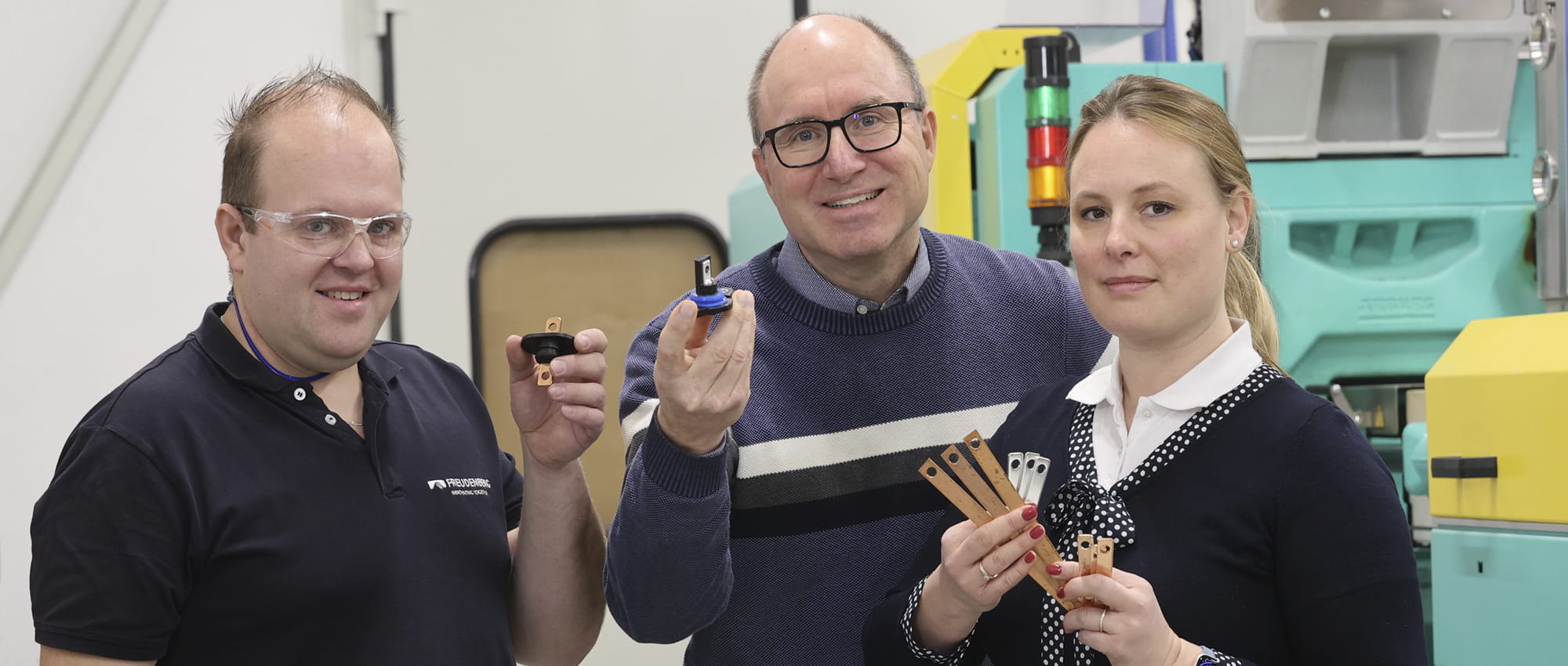
Innovative Sealing Solution for Busbars
Aluminum or copper conductor rails – or busbars – are found in all electric vehicles. They allow electricity to flow within powertrains. In the past, the busbars’ rectangular design has made it hard to seal them effectively. Freudenberg Sealing Technologies has now created a solution that is suitable for large-scale production. It is both impressive and in demand.
The plastics and sealing experts at Freudenberg Sealing Technologies have achieved what sounds like a triumph of geometry. They have developed a sealing solution to enclose rectangular copper or aluminum conductor rails (also known as busbars) completely securely. The seal uses chemical bonding to keep any fluid along the busbar from leaking into sensitive areas, such as the car's power electronics.
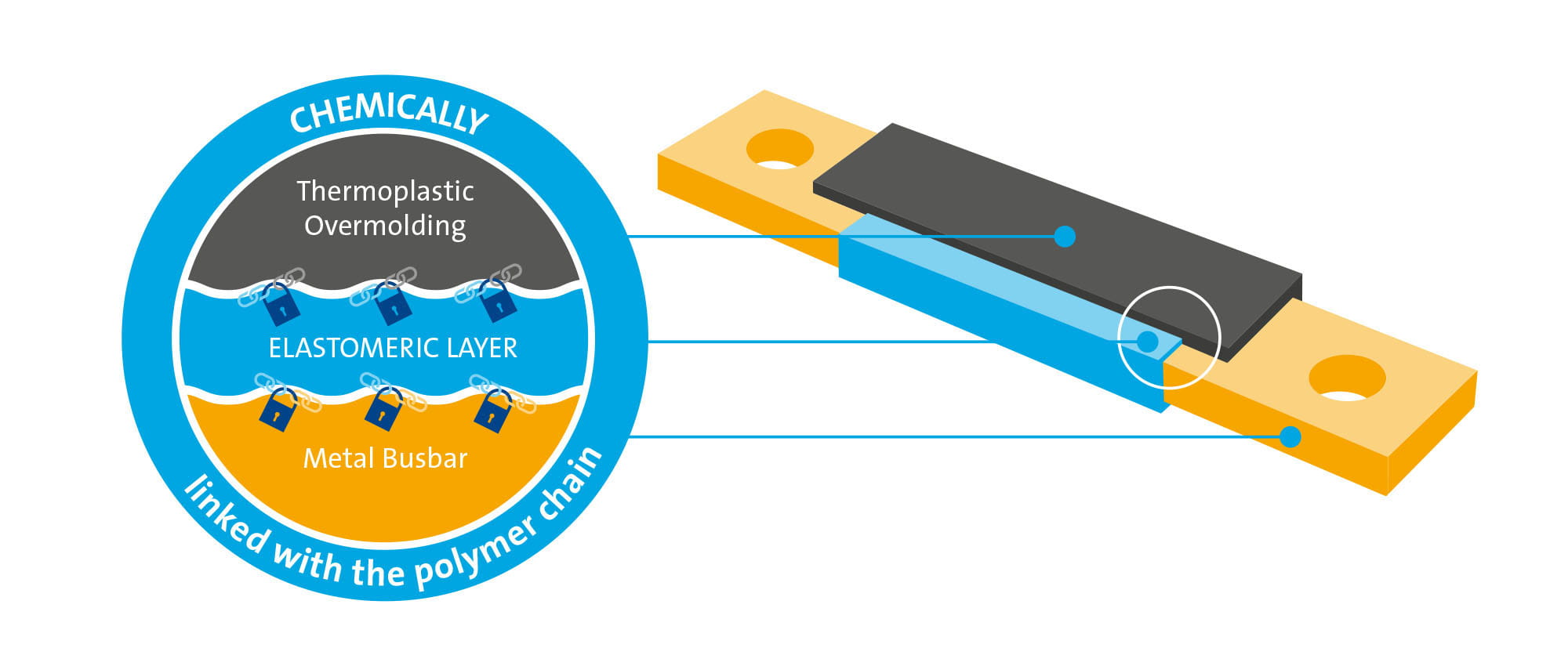
Busbars Carry and Distribute Electric Current
Busbars are a proven technology used in many applications and in a range of industries. These rectangular power rails, or current-carrying conductors, can be used wherever high levels of current flow are required. They transport and distribute energy, making them a good solution at many locations in electric vehicles. They include charging and battery management systems, performance electronics and electric drivetrains. Their length and cross-section vary by area of application. Most busbars are found in the drive battery and have a compact design. The geometry of busbars gives them an advantage over insulated copper cables. “They are also robust, easier to produce and thus more competitive,” said Marco Sutter, Global Market Segment Manager at Freudenberg Sealing Technologies.
Today many electric cars have oil-cooled motors. The sensitive power electronics of their inverters must be protected against oil from the e-motor. This requires efficient sealing in the busbar module where the copper rail is encased in a thermoplastic housing. The seal’s job is to close the gap between the copper and the plastic – and do it reliably. The market has not come up with completely satisfactory solutions so far. “Round busbar feedthroughs take up more space and are more expensive," Parisa Burger said. And potting, the application of a mass of viscous adhesive around the busbar, is not ideal. It affects the design and provides incomplete protection against leaks. “So far, all the approaches on the market are just improvisations,” she added.
Cooling & Flame Protection
Freudenberg Sealing Technologies not only offers sealing solutions for busbars in electric vehicles. Certain busbar sections can be encapsulated with materials that have either cooling or flame-protection properties. For example, heat dissipating elastomers prevent conductor rails from becoming too hot and damaging power electronics or other electrical components. Special flame-protection materials such as Thermoplast Quantix® ULTRA in turn make sure that busbars in batteries withstand flames and continue to provide insulation in the event of a fire.
Individualized solution: Freudenberg Sealing Technologies produces busbar modules with an integrated seal as prescribed by the automakers. This makes it possible for them to manage and install the busbars in line with their design specifications.
Freudenberg Creates a Totally New Approach
Freudenberg Sealing Technologies has recognized the problem in recent years and tackled it from scratch. An interdisciplinary team of material developers and process experts considered the insights from the sales team and then took a new approach: “Our advantage is that we had been bonding rubber on both metal and plastic chemically for a long time,” Parisa Burger said. “To seal the busbar module, our chemists came up with the idea of developing an elastomer seal that – so to speak – fuses with the copper on one side and with the plastic housing on the other. All three components bond integrally, becoming an impenetrable unit.” The idea took shape and has now been fully developed.
The solution is based on the use of vulcanizable, high-performance elastomers as the sealing rubber layer, which bonds integrally with the two other materials. “For the elastomers, we turn to our extensive material construction kit,” Marco Sutter said. “We select the right material depending on the prevailing temperatures and pressure and the fluid that the module has to seal against.” In a new, innovative process, a reaction produces the adhesive bond. Think of the result as a chain with its chain links welded together. “The molecular chains of the sealing rubber bond with the copper on one side and with the plastic housing on the other. In a sense, they become one part, which blocks the penetration of liquids,” said Parisa Burger. “By chemically bonding the components and avoiding the kind of mechanical bond found in conventional seals, we have developed a truly revolutionary process,” she said.
Our customers are getting a module that is completely tailored to them and is the best solution both technically and commercially.
Katinka Raschke of the Busbar Incubation Team at Freudenberg Sealing Technologies
No Design Restrictions
The “media-tight over-molding of rectangular busbars" is both fascinating and impressive. The Busbar Incubation Team responsible for the Freudenberg Sealing Technologies project delved deeply into automakers' specifications, making sure that they could manage and install the busbars as prescribed. Since it takes up no additional space, the integrated Freudenberg seal is not a limiting factor. Even the plastic desired by the customer is taken into account during the module’s development. Customers have ended up sourcing the entire busbar module from Freudenberg Sealing Technologies. “Our customers are getting a module that is completely tailored to them and is the best solution both technically and commercially,” said Katinka Raschke of the Busbar Incubation Team.
A number of electric vehicle makers have become aware of the innovation. Freudenberg Sealing Technologies is now in the prototype phase with several customers and is carrying out validation tests. Burger and Katinka Raschke of the Busbar Incubation Team are optimistic about the future: “We are very confident that our sealing innovation will soon go into regular production in the first vehicle models.”
This article originally appeared in ESSENTIAL, Freudenberg Sealing Technologies’ corporate magazine that covers trends, industries and new ideas. To read more stories like this, click here.
More Stories About E-Mobility
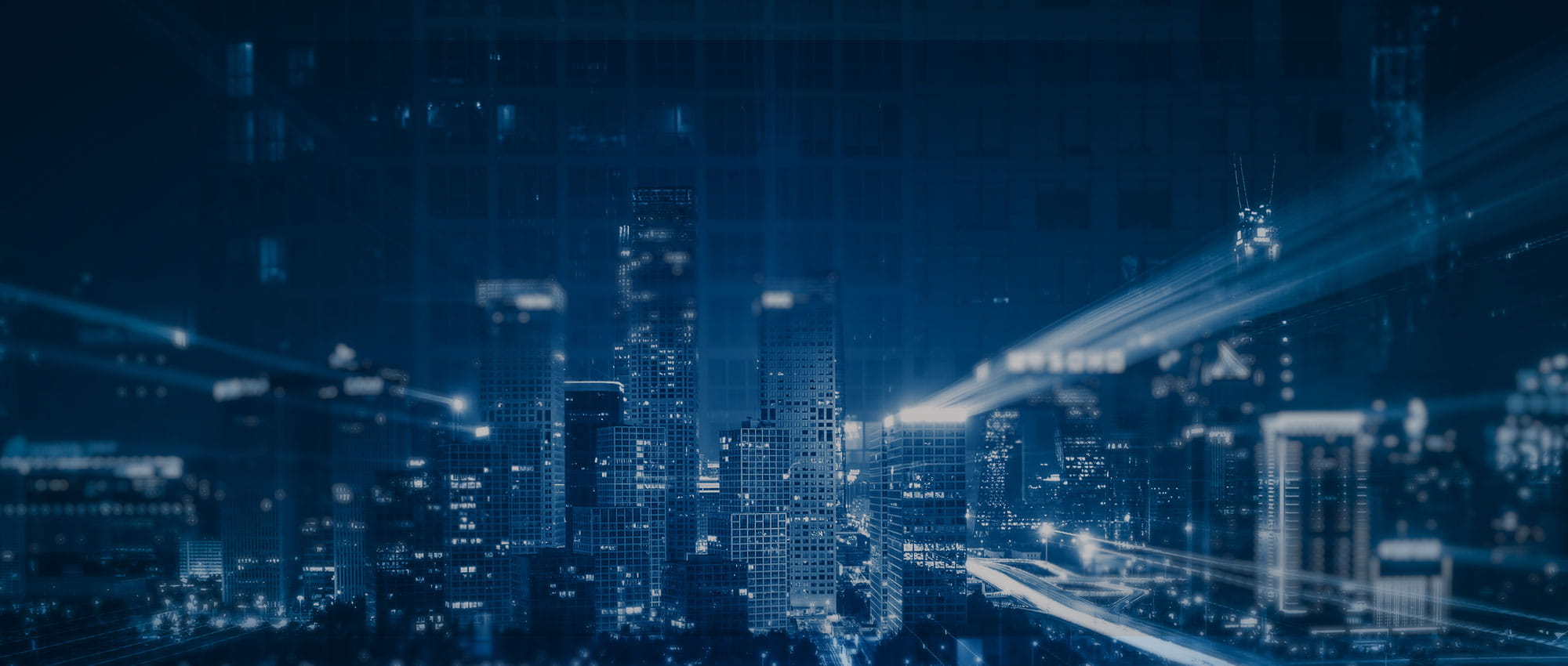
Join Us!
Experience Freudenberg Sealing Technologies, its products and service offerings in text and videos, network with colleagues and stakeholders, and make valuable business contacts.
Connect on LinkedIn! open_in_new