Obtain news and background information about sealing technology, get in touch with innovative products – subscribe to the free e-mail newsletter.

It Doesn’t Have to Be Dark
Machine learning, artificial intelligence and automation are fundamentally changing our industrial processes. But despite all the progress in robotics, a question is being raised: whether the fully automated factory is in fact a worthwhile goal – or whether the true “Smart Factory” might not better combine the strengths of people and machines.
When will the lights go out in factories around the world? Not in a figurative sense, but literally: The vision of the “Dark Factory” has been a preoccupation of factory managers for some time. “Dark” because the robots working there can function completely autonomously and do without human support. The lights might as well be off since robots and machines require no illumination, which devours huge amounts of electricity. And robot technology is certainly on the advance.
But it is increasingly bumping up against its limits. One example: The mechanical process of “reaching into the box.” How do you get a robot to identify the right tool and grip it properly with its gripping arm? The human being continues to be superior here. Again and again, robot manufacturers are unable to take the progress that they have made under laboratory conditions and reproduce it in the factory. There are other related issues as well: For example, how long would a robot be allowed to try to grasp an object before a human being comes over and helps it.
The Products Organize Themselves
That is likely why more and more engineers and scientists are asking: Aren’t there goals that are smarter than the “Dark Factory?” People have been looking at the machines for a long time, according to one of the theses of Prof. Johannes Fottner of the Mechanical Engineering Department of the Technical University Munich. He spoke at the VDI conference “Robotics for the Smart Factory,” an industry gathering of manufacturers, factory managers and software engineers in December 2018. “What would it be like to look at the products?” Fottner asked. Some German automakers are already testing what he has in mind: Modular production instead of assembly lines. That means the sequence of production steps changes depending on the requirements. “If a station is occupied or no longer needed, the vehicle moves into another station,” Fottner said. This in turn requires a decentralized, self-organizing material flow. But even these developments have come a long way, he said. In systems of this kind, the human being is still important: he’s the element that plans, considers and makes adjustments.
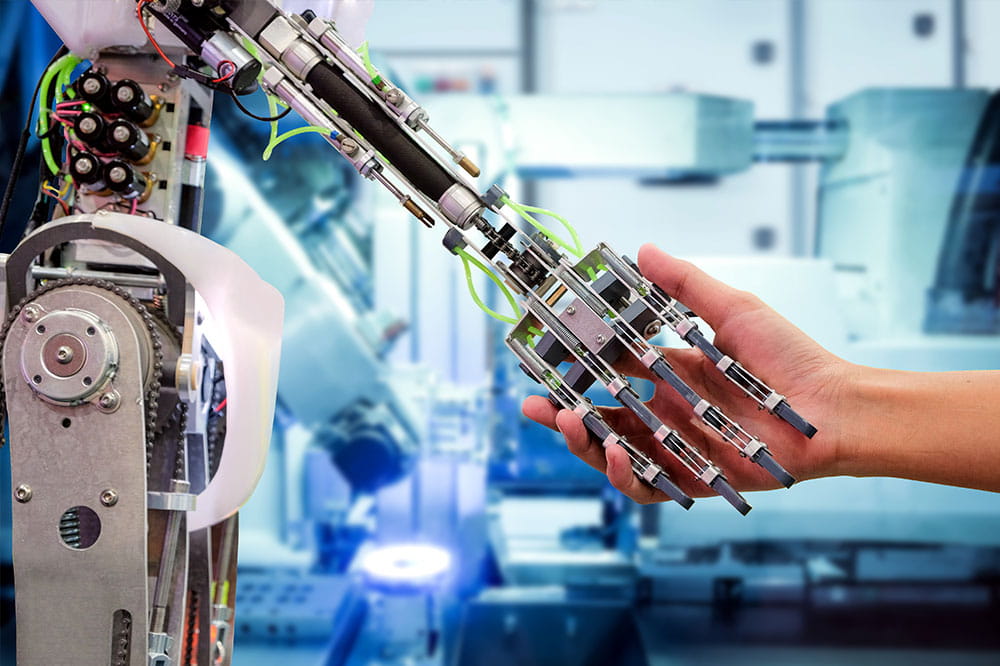
Artificial intelligence and machine learning continue to run up against their limits. “My dream would be a robot that knows all the tax rules and automatically creates a tax declaration for me,” said Prof. Kai Furmans of the Karlsruhe Institute of Technology. “But my tax advisor told me this would be impossible because the regulations aren’t consistent.” It’s the same situation in factories, he said. There are far too many forced relationships that cannot be logically connected with one another. To be sure, there has been excellent progress in the past, but development engineers are increasingly looking at collaborative, people-machine systems to link the strengths of both. “There were already factories bereft of people during the so-called Industry 3.0,” Fottner said. “But this was under certain circumstances. We have to move away from the idea of wanting to replace people on a one-to-one basis.”
Industry 4.0 as a Process Revolution
Fottner points out that “Industry 4.0” is somewhat misunderstood. “Earlier industrial revolutions were closely tied to a technology, the steam engine or the assembly line,” he said. “Industry 4.0’s actual innovation is a process revolution: connectivity, cyber-physical systems and new options for communication.” But the actions of human beings must be totally different if the processes change.
In turn, cooperation between robots and human beings raises entirely new questions: How do machines and people behave when they encounter one another? Which ones have to step aside and which of the two has to stop working when they block the efforts of the other? So far, it has often been the robot, which loses efficiency in the process. “It is much like traffic,” Fottner said. “Autonomous driving wouldn’t be a problem if every vehicle functioned autonomously, but human beings complicate the calculation.” Perhaps it is not surprising that the research by robotic manufacturers shows that people react very differently to robots. “Some run up to the robots aggressively. Others pull back shyly,” said Benjamin Sommer of the Magazino GmbH, which manufactures driverless transport systems. Depending on the type of person, the robot would have to react differently.
Operating System: Speech
There are already some technical solutions for this kind of cooperation: Bosch Rexroth is now experimenting with “sensor skin,” an electrical field around the machine. This is supposed to reliably detect the distance between the machine and the person. The machine would only curtail its speed if the person comes close to the machine. Other manufacturers are trying to increase the machines’ communication capabilities so they can react flexibly to as many situations as possible. “The operating system of the future will be human speech,” according to a current dictum. To an even greater extent than today, people will be able to give direct orders to machines that they are working with.
“Automation is not necessarily associated with situations where people are no longer working in factories,” Fottner said. He is convinced that, even twenty years from now, there will be factories where people work. “The human being will be responsible for deliberations and planning,” he said. The challenge for the future: the systems where human beings and robots can work with one another.
Where is digitalization heading, what is it doing with us, and what is actually behind this phenomenon? In our thematic cycle “Digitalization,” we get to the bottom of these questions and condense the topic in the upcoming issue of ESSENTIAL, among other media.
Read more about this topic: COO Dieter Schäfer and CFO Ludger Neuwinger-Heimes explain what the “fourth industrial revolution” means for Freudenberg Sealing Technologies (FST).
More Stories About Digitalization
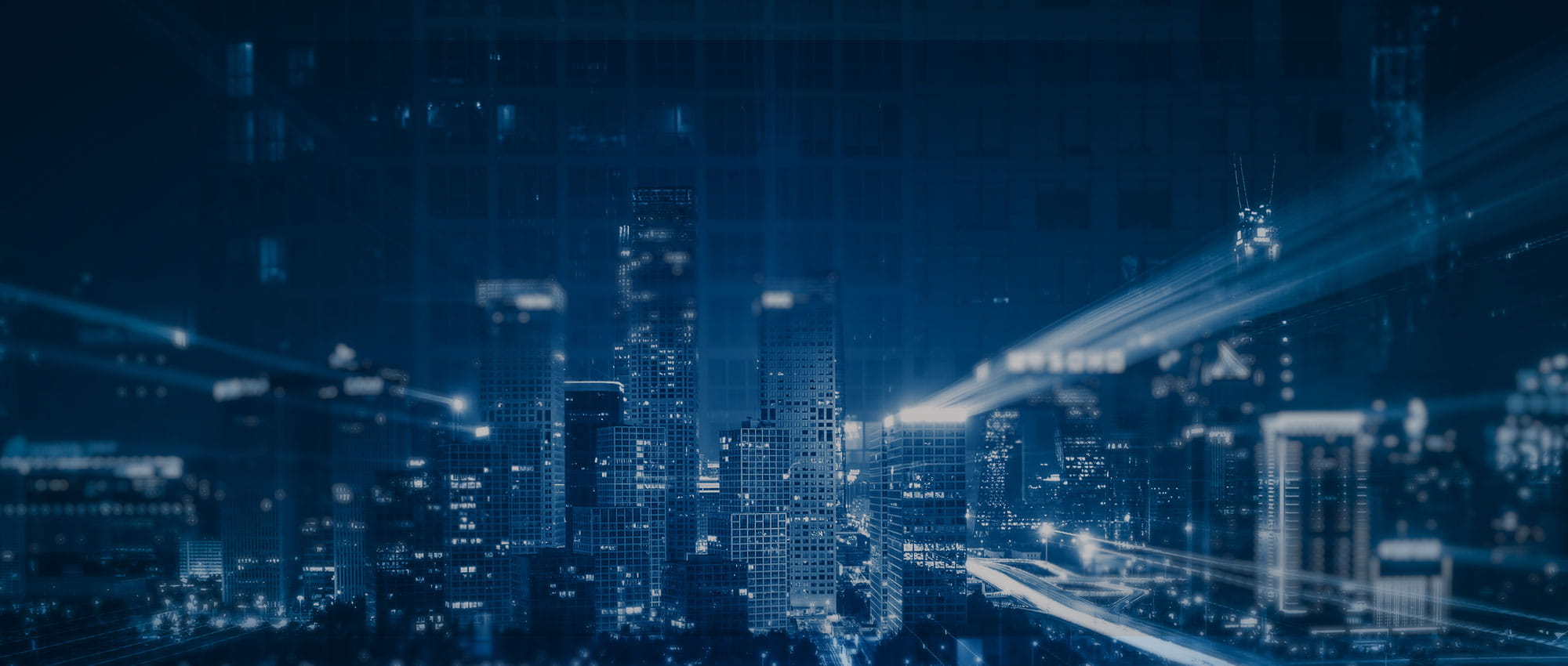
Join Us!
Experience Freudenberg Sealing Technologies, its products and service offerings in text and videos, network with colleagues and stakeholders, and make valuable business contacts.
Connect on LinkedIn! open_in_new