Obtain news and background information about sealing technology, get in touch with innovative products – subscribe to the free e-mail newsletter.
03.12.2019
Zero Friction Bearing Material for Improved Lubrication
The original Levitorq design was created to reduce weight, decrease friction, improve thickness/flatness control and often provide a cost benefit to the customer. It relies on the principles of hydrodynamic oil film technology and is designed to create a surface on which a bearing can roll, or a load can be applied. Traditionally, thrust washers are made from metals, but Freudenberg has used its material expertise and design knowledge, along with proprietary software and testing capabilities, to develop design alternatives in thermoplastic or thermoset materials that allow engineers to replace heavy metal thrust washers.
In pushing thrust washer technology further, Freudenberg engineers and material scientists looked at a variety of application parameters to optimize design performance, including thrust load, rotation speed, temperature, counter surface characteristics, lubricant type and availability of the lubricant. A team of experts developed several scoop designs based on the types and availability of lubricants used in powertrain applications. These designs help optimize the availability of lubrication at the inner diameter, thus improving lubrication across the washer.
Nine Times the Pumping Ability, Three Times the Critical Speed
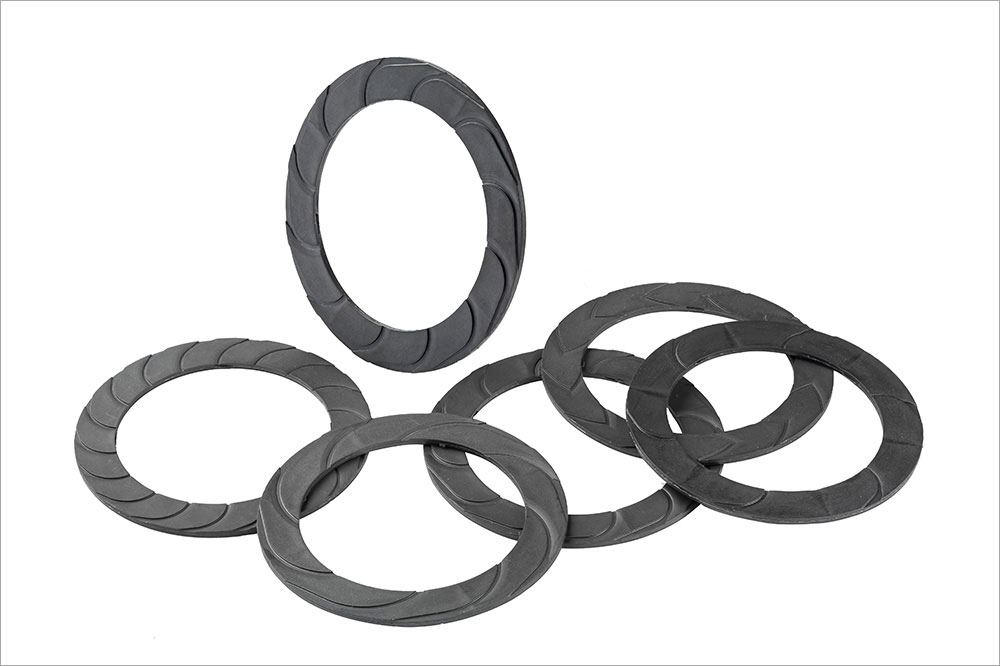
Pressurized or splash lubrication from the outer diameter is challenging to address because of limited fluid availability to remove heat. Recent design and material innovations from Freudenberg have enabled the use of polymeric thrust washers for such applications. The new Levitorq scoop feature significantly affects performance as it enables the application to use available fluid more effectively. Also, polymeric materials are designed to have low friction coefficients even in dry running conditions. These materials have dry friction coefficient one tenth of metal thrust washers.
Critical speed is when loss of pumping ability occurs due to centrifugal force. In a comparison between Freudenberg’s patent-pending D11 polymer thrust washer and its traditional thrust washer, the effectiveness of the new scoop design becomes obvious. The new polymeric thrust washers have nine times the pumping ability and three times the critical speed.
These designs are ideal for applications with limited or splash lubrication. The scoop feature is able to successfully move fluid under the washer to enable the application to run at higher critical speeds – up to 10,000 rpm – and pressures without failure.
An Exciting New Industrial Solution
“This patent-pending design is ideal for transmissions and driveline components, as well as a number of industrial applications,” said Ray L. Szparagowski, Technical Director Automotive and High Performance Plastics at Freudenberg-NOK Sealing Technologies. Freudenberg-NOK runs the business operations for Freudenberg Sealing Technologies in the Americas.
“Our new Levitorq thrust bearings have the potential to optimize lubrication in most applications, so the possibilities are very broad and exciting.”
Freudenberg’s LESS portfolio of engine, transmission and E-Mobility products includes a variety of seals, gaskets, encoders, accumulators, sealing modules and lightweight housings. These products have been uniquely engineered to reduce friction and weight, cut fuel consumption, ease installation challenges and lower emissions. First developed and benchmarked for automotive applications, Freudenberg has been able to leverage its LESS technology for other industrial applications resulting in a significantly shortened development cycle.
Download Documents
Download Images
News Service
You can subscribe to the Freudenberg Sealing Technologies news alert service, bringing you the news as soon as they are published. You can always unsubscribe from this service.
Subscribe now! chevron_rightFurther Articles With These Taggings
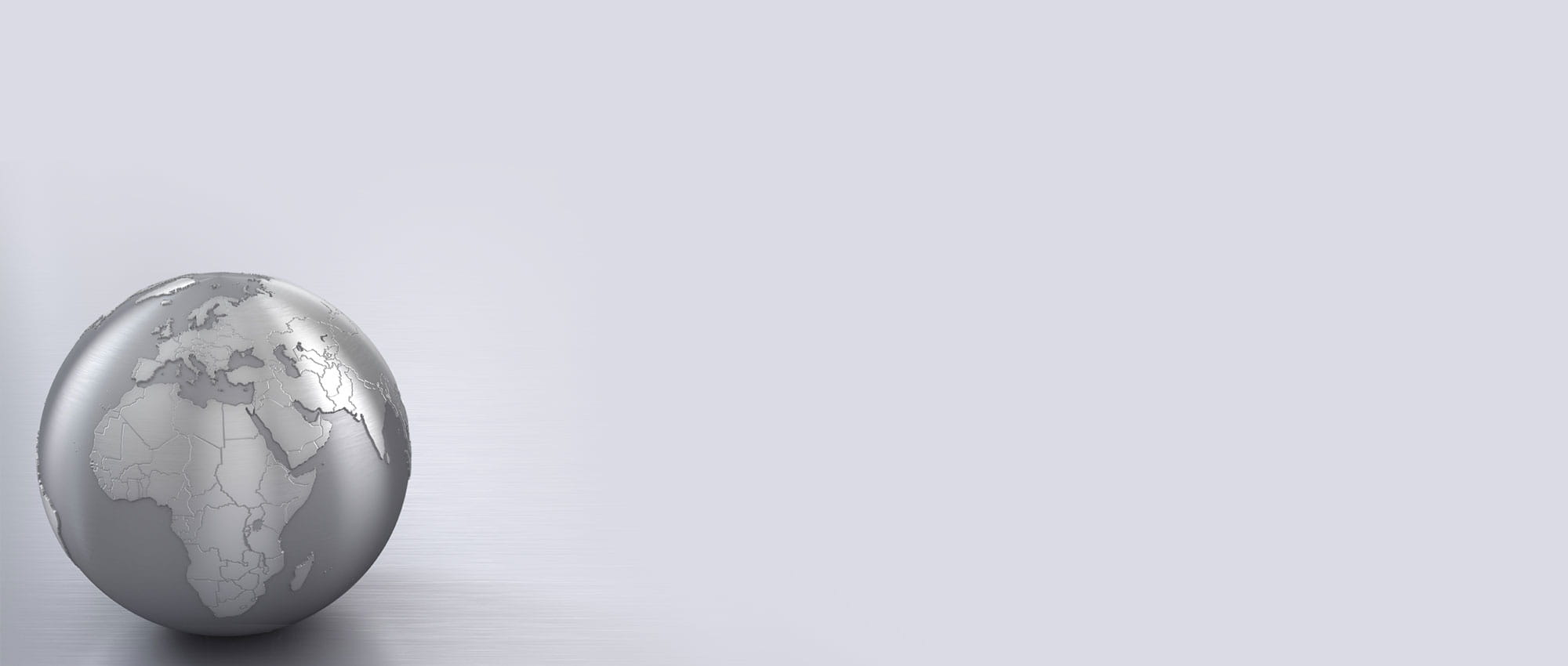
First Hand News
Best of all, keep up with the latest developments
with the Freudenberg Sealing Technologies newsletter.