Obtain news and background information about sealing technology, get in touch with innovative products – subscribe to the free e-mail newsletter.

Robotics@Model.HeadlineTag.Tag>
Robotic Seals for Improved Features in your Equipment
We are more than seals, we enable and unlock new features for robotics
Robots have always fascinated us! The dream of human-like machines that independently perform complex tasks is ancient. What began as a utopia has long since gained a firm place in the automation industry as industrial robots. 6-axis, SCARA, or Delta robots take over physically demanding, unhealthy tasks and tirelessly complete even the most monotonous work steps 24/7.
This permanent use in mostly demanding industrial environments requires maximum performance from all robot components. For the seals, this means above all high demands on reliability and service life. Immerse yourself in the universe of robotics and discover how Freudenberg Sealing Technologies can support your company with its customized sealing solutions.
Sealing Solutions for Your Robotics Applications
Learn more now and increase your productivity
Definitions: What Is a Robot?
Since their beginnings in the automotive industry, robots have conquered many other industries. For example, they are now used in manufacturing, agriculture, medicine, research, and the military. The use of artificial intelligence (AI) enables them to learn and perform complex tasks independently. As a result, they are increasingly able to adapt to changing conditions and respond to unforeseen situations. This enables more efficient and precise execution of tasks and opens up new possibilities for robotic applications in various fields. What all these challenges have in common is that they demand long service lives, extreme precision and safety. Freudenberg Sealing Technologies’ experts develop high-performance sealing solutions for robots to maximize their performance, reliability and service life.
In general, a robot refers to complex, engineered systems designed to perform various tasks automatically or under remote control. They are usually composed of various mechanical, electronic and software components that interact with each other. There is no universally accepted definition of a robot. However, some organizations and institutions have developed generally accepted definitions or are contributing to the understanding of robots by establishing standards and sharing knowledge:
ISO 8373:2012 defines a robot as follows:
“An actuator operating in at least three independent axes to move, position, assemble or machine material, parts, tools or special equipment.”
Developing technical standards
Although the IEEE does not provide a specific, all-encompassing definition for robots, the IEEE Robotics and Automation Society (RAS) works to promote research, development, and application of robotics and automation technologies. IEEE RAS publishes technical journals, conference papers, and supports working groups that contribute to various aspects of robotics.
Promotion and exchange of knowledge
The International Federation of Robotics (IFR) is a non-profit organization that promotes the worldwide exchange of knowledge and information about robotics and automation. The definition of the IFR is based on the ISO definition and states that:
“A robot is an automatically controlled, programmable, multi-axis machine that can be either fixed or mobile for use in industrial automation.”
Focus on industrial robotics technology
The Robotic Industries Association (RIA) is a North American industry organization focused on industrial robotics technologies. It promotes safety standards and innovation in the robotics industry. The RIA’s definition refers to the ISO 8373:2012 standard and describes robots as follows:
“A robot is an actuator that operates in at least three independent axes to move, position, assemble, or machine materials, parts, tools, or specialized equipment.”
VDI Guideline 2860 defines them as follows:
“Industrial robots are universally applicable automatic motion machines with multiple axes whose movements are freely programmable (i.e., without mechanical or human intervention) and, if necessary, sensor-guided with respect to movement sequence and paths or angles. They can be equipped with grippers, tools or other manufacturing equipment and can perform handling and/or manufacturing tasks.”
Classification based on application flexibility and intelligence:
- Manual Manipulator: a handling device without a program, is guided directly by the operator.
- Fixed Sequence Robot: the manipulator operates repeatedly according to a constant motion pattern. Movement pattern can be changed with greater effort
- Variable Sequence Robot: the manipulator works repeatedly according to a constant motion pattern. Movement pattern can be changed quickly, without great effort.
- Playback Robot: a motion sequence taught once by the operator can be repeated at will.
- Numerical Control Robot: works similar to an NC-controlled machine. The information about the motion sequence is entered numerically into the device via pushbuttons, switches or data carriers.
- Intelligent Robot: has various sensors and is therefore able to adapt the program sequence independently to changes in the workpiece and the environment.
It All Began With a Mechanical Duck
The history of robots dates back to the 18th century, when Jacques de Vaucanson created a mechanical duck that was able to swim, dive and even digest. However, the real development of robots began in the 20th century, as their potential for automating industrial production processes was recognized:
1954
Georg Deval develops the first industrial robot. “Unimate” is used in a factory to advance the automation of manufacturing processes.
1970s
Industrial robots are increasingly used in the automotive industry to automate and speed up production.
1977
In this year, the company Yaskawa achieved a minor revolution with the first articulated robot by today’s definition. With movement around five axes, the “Motoman L10” was the industry’s flagship model at the time.
1980s
Robots are also used in other industries, such as electronics and food, to automate production and improve working conditions for people.
1990s
With the introduction of sensors and cameras, robots are able to perform more complex tasks, such as inspecting products or sorting materials.
2000s
The increasing networking of machines and systems enables robots to be seamlessly integrated into production lines to further increase efficiency.
2010s
The development of collaborative robots (cobots) enables close cooperation between humans and machines and opens up new areas of application, such as cooperation in assembly lines or assisting humans with physically demanding tasks.
2020s
Further development of artificial intelligence and machine learning will enable robots to take on increasingly complex tasks, such as autonomous navigation in factories or automatic detection of errors in production.
How Do Robots Work?
Robots use mechanical components such as joints, motors and gears to perform precise movements. They are often equipped with multiple degrees of freedom enabled by joints such as ball joints, swivel joints, or rotary joints. Drive systems such as electric motors, hydraulics or pneumatics provide the necessary power transmission and motion control.
Copied from nature
Like the arm of a human being, for example, a robot consists of rigid connecting elements, the so-called arm links, and movable connecting points, the joints. The effector, i.e. the tool, is the last arm link. For each arm link, a tool center point (TCP) is defined, to which the motion specifications refer.
Articulated and flexible
Translational and rotational joints are two main categories of joints in robotics that allow different types of motion:
-
Translational joints: these joints allow linear movements along one or more axes. They change the position of the robot or its components without performing a rotation around an axis. Examples of translational joints are the Prismatic Joint, which allows linear motion along one axis, and the Cylindrical Joint, which moves both rotationally and linearly along the same axis.
-
Rotational joints: these joints allow rotational movements around one or more axes. They change the orientation of the robot components without changing their position in space. An example of a rotational joint is the revolute joint, which allows rotation around one axis. Rotational joints also include the spherical joint, which provides combined rotation around multiple axes, the cylindrical joint, and the pivot joint, which provides limited rotation around one axis.
Motion in space
Degrees of Freedom (DOF) are the independent motion capabilities of a mechanical system. In terms of robots, they describe the number of independent motions or changes in position and orientation that the robotic arm or mobile system can perform.
In robotics, degrees of freedom are often divided into two categories: translational and rotational degrees of freedom. Translational degrees of freedom allow a robot to move along the three spatial axes (X, Y, Z), while rotational degrees of freedom allow rotation around these axes (roll, pitch, yaw).
The more degrees of freedom a robot has, the more flexible and versatile it is able to perform different tasks and execute complex motions. However, the number of degrees of freedom can also increase the complexity of the control system and affect the mechanical stability of the robot.
Basis for control and programming
In robotics, kinematics is of particular importance because it is the basis for robot control and programming. In this context, there are two main types of kinematic analysis:
- Forward kinematics:
this analysis is concerned with determining the position and orientation of the end effector (e.g., gripper or tool) of a robot based on joint positions and angles. Here, the geometry of the robot and the relationship between joint parameters and the end effector position are used to determine the exact position in space. - Inverse kinematics:
In contrast to forward kinematics, inverse kinematics solves the opposite problem. Here, the position and orientation of the end effector is specified. In addition, the appropriate joint positions and angles must be found to achieve this position. This is often a more complex problem, as there may be multiple solutions (or no solution) for a given end effector position. - Parallel kinematics:
In parallel kinematics, multiple chains of joints and segments are simultaneously connected to the base and end effector (e.g., gripper or tool) of the robot. This allows delta or hexapod robots to have higher stiffness, accuracy, and speed because the load and motion requirements are distributed evenly among the individual chains. However, parallel kinematics can also result in a more limited range and restricted freedom of movement, as the individual joints and segments are more closely related to each other. - Serial kinematics:
In robots with serial kinematics, such as jointed-arm robots and gantry robots, the joints and segments are arranged in a chain or row, with each joint directly connected to the preceding and following segments. This arrangement is common in many conventional industrial robots and robotic arms. Serial kinematics allow for greater range and flexibility in the robot’s movements, but can also result in lower stiffness and precision, as errors and inaccuracies can accumulate along the kinematic chain. Other examples of robots with serial kinematics include SCARA robots, gantry robots, dual-arm robots, and palletizing robots.
Robots - Human Machines?
The variety of robots and autonomous devices has grown immensely in recent years, ranging from robotic dogs to autonomous vehicles and the many different industrial robots. But what actually makes a robot a robot and what distinguishes it from a machine?
While machines are limited to individual work steps, robots can take on a variety of tasks. They perform monotonous tasks such as feeding, picking, sorting or coating constantly and reliably, thus increasing productivity.
For most of them, the physical form is a prerequisite for a robot. However, if you look at how they work, software bots could also be called robots. Chatbots, for example, work independently, constantly learn and can react to unforeseen events with the help of artificial intelligence.
Learn more about this fascinating world in our issue of Essential on robotics chevron_right
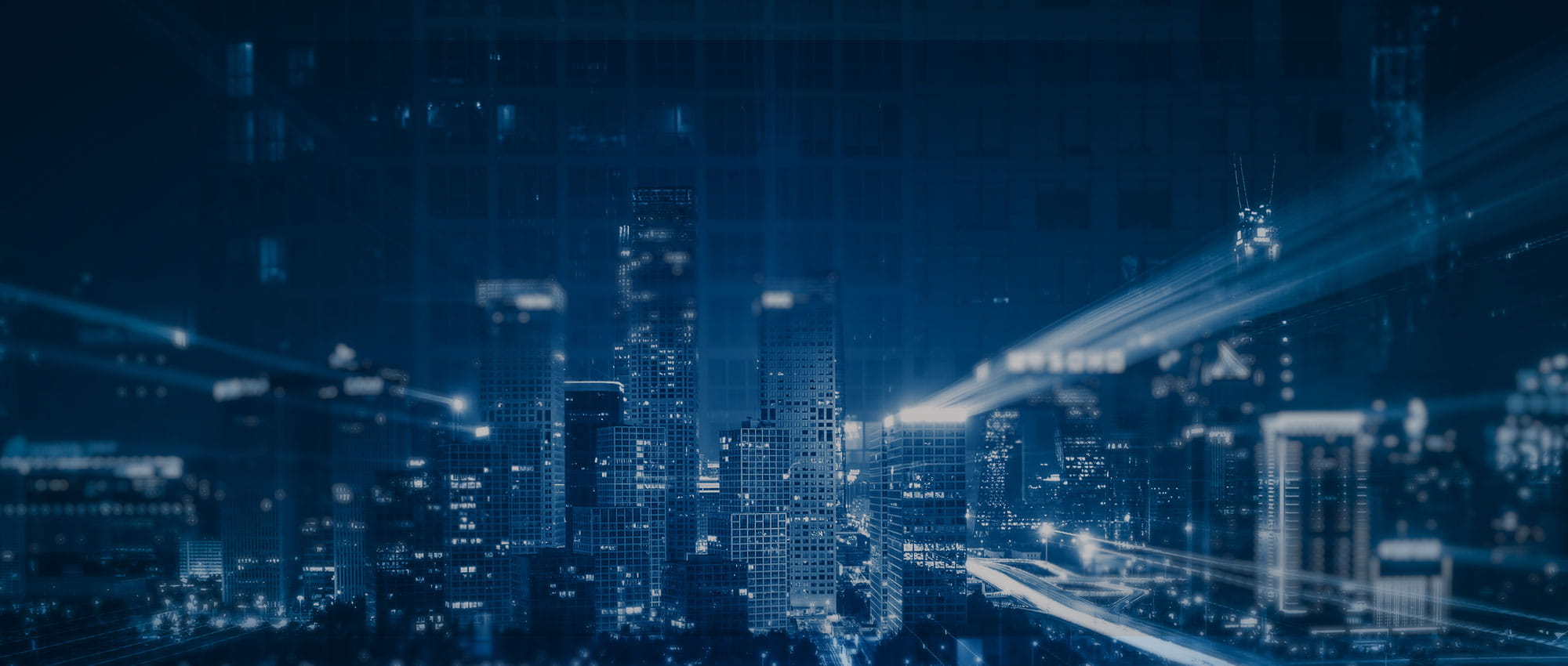
Join Us!
Experience Freudenberg Sealing Technologies, its products and service offerings in text and videos, network with colleagues and stakeholders, and make valuable business contacts.
Connect on LinkedIn! open_in_new