Obtain news and background information about sealing technology, get in touch with innovative products – subscribe to the free e-mail newsletter.
09.04.2019 | Press release
New Lightweight Solutions to Seal against Electromagnetic Radiation
Weinheim (Germany), April 9, 2019. Electronic components must be protected from disruptions caused by electromagnetic waves. Experts from Freudenberg Performance Materials and Freudenberg Sealing Technologies are working together on ways to provide shielding with plastic housings. In the future, they could partially replace the aluminum versions that have dominated the market until now.
Holger Michael Steingräber
Director Global Communications (Freudenberg Performance Materials)
Telephone: + 49 (0) 6201 80 6640
Fields of electromagnetic interference often form where electric current flows. When the flow is powerful, in high-performance electric powertrains, for example, the strength of these fields increases, and they can disrupt the signal flow in microprocessors and transmitter-receiver systems. One proven remedy is the encasement of electric components in housings made of a conductive metal. So far, aluminum has been the main tried-and-tested material for this. But its use substantially increases the proportion of aluminum in electric vehicles. This doesn’t just impair driving dynamics and vehicle range. Costs also rise because the tools used to produce the aluminum housings have limited durability. Due to their lack of conductivity, significantly lighter plastics have not been considered as materials so far. But experts from Freudenberg Performance Materials and Freudenberg Sealing Technologies have teamed up to develop processes that can equip plastics with conductive coatings or nonwovens. Early lab tests show excellent values for electromagnetic shielding: up to 99.999999 percent.
Two general approaches to achieving good shielding
There are basically two technical approaches to achieving good shielding in the frequency range of 150 kHz to 100 MHz – a spread especially relevant to the drivetrains of electric vehicles. One of them relies on a specific effect: Electromagnetic waves striking conductive surfaces can be almost entirely deflected. A second approach is to weaken electromagnetic waves at relatively high frequencies in the interior of a material – absorption is the term used to describe this effect. Two processes developed by Freudenberg combine the two effects. The processes offer specific benefits that depend on the size of the component, among other factors.
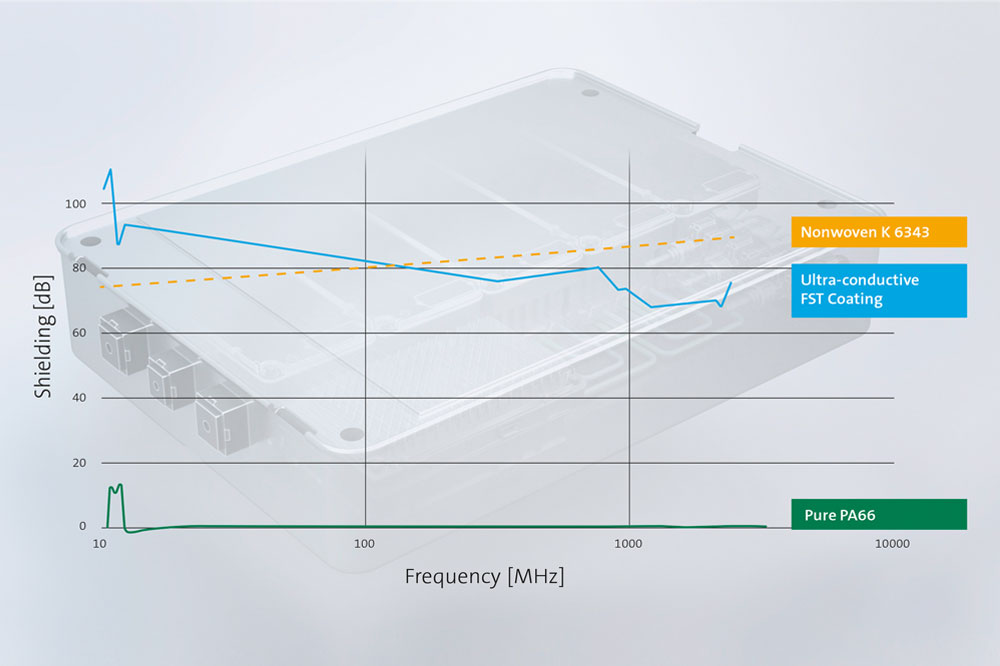
Freudenberg Performance Materials has developed a nonwoven that is treated with a special galvanic process. It totally encases individual nonwoven fibers with a copper surface, covered by another material layer to prevent corrosion. Since these nonwovens are produced as endless metered product, the technology is especially suited for components with large surfaces produced in the preforming process. Housing covers for traction batteries are one example. The trimmed nonwoven can then be inserted and compressed into the tool with the pre-product – which is necessary anyway. An inseparable bond is formed during the setting process. Due to the low density of the nonwoven, an extremely small quantity of the material – a mere 60 grams – is consumed per square meter. That is less than the corresponding weight of normal printer paper. Combined with a lighter-weight plastic carrier material, the result is weight savings of up to one-third compared to aluminum housings. This represents about a 5-kilogram reduction in the weight of a battery housing cover.
„Seal & Shield“
For the shielding of fairly small components, Freudenberg Sealing Technologies has developed coatings that deflect electromagnetic waves from their surfaces. The plastic component is coated with an aqueous dispersion whose plastic matrix contains filler offering a high level of electric conductivity. One alternative is to apply the dispersion to a plastic film, which is in turn integrated into the injection molding tool. In this process, the highly conductive coating lies inside, so it is well protected from mechanical damage. Long-term tests on material samples show that such coatings display very good aging behavior even at 120°C and completely meet the requirements of the LV 124-2 test standard. The standard sets industry-wide testing processes and boundary values for electrical components permitted for use in cars. The protective coating, the plastic housing and its seal create a unit whose parts are ideally coordinated with one another. Freudenberg Sealing Technologies offers these solutions under the phrase “Seal & Shield.”
Whatever process is used, neither the coating nor the use of the nonwoven impairs the mechanical properties of the plastic component. This is crucial where the vehicle’s electrical components such as motors or batteries are installed in a way that they can be damaged in an accident. But the acoustic and vibration-related behaviors of a component are determined exclusively by the easily calculable properties of the plastic.
„Innovating Together“
In some applications, it is important for the absorption to account for the lion’s share of electromagnetic shielding. This especially applies to the housings for radar sensors that operate in the 77-gigahertz frequency range. If the housing surface were to deflect radar waves, the result could be signal distortion. Freudenberg Sealing Technologies has developed a composite material that can be processed using injection molding and, based on early measurements, exhibits much higher absorption rates than commercially available plastics.
It is not just Freudenberg Performance Materials and Freudenberg Sealing Technologies that are teaming up to develop lightweight materials that offer electromagnetic shielding. The two sister companies collaborate with Freudenberg Technology Innovation, the Freudenberg Group’s main research unit, on the selection of appropriate test procedures and on material development. “‘Innovating together’ is not just a buzzword – it’s part of our Freudenberg DNA,” said Claus Möhlenkamp, Chairman of the Board of Management at Freudenberg Sealing Technologies. “We are working together to simplify the path to the era of electric mobility.” Dr. Frank Heislitz, CEO of Freudenberg Performance Materials, added: “As an example, electric mobility demonstrates a main strength of the Freudenberg Group. As sister companies, we have the ability to combine very different kinds of expertise, which gives us a major advantage. We can work together to develop innovative solutions for our customers.”
Ulrike Reich
Head of Media Relations & Internal Communications
Telephone: + 49 (0) 6201 960 5713
ulrike.reich@fst.com chevron_rightNews Service
You can subscribe to the Freudenberg Sealing Technologies news alert service, bringing you the news as soon as they are published. You can always unsubscribe from this service.
Subscribe now! chevron_rightMore news on the subject Technology & Innovation
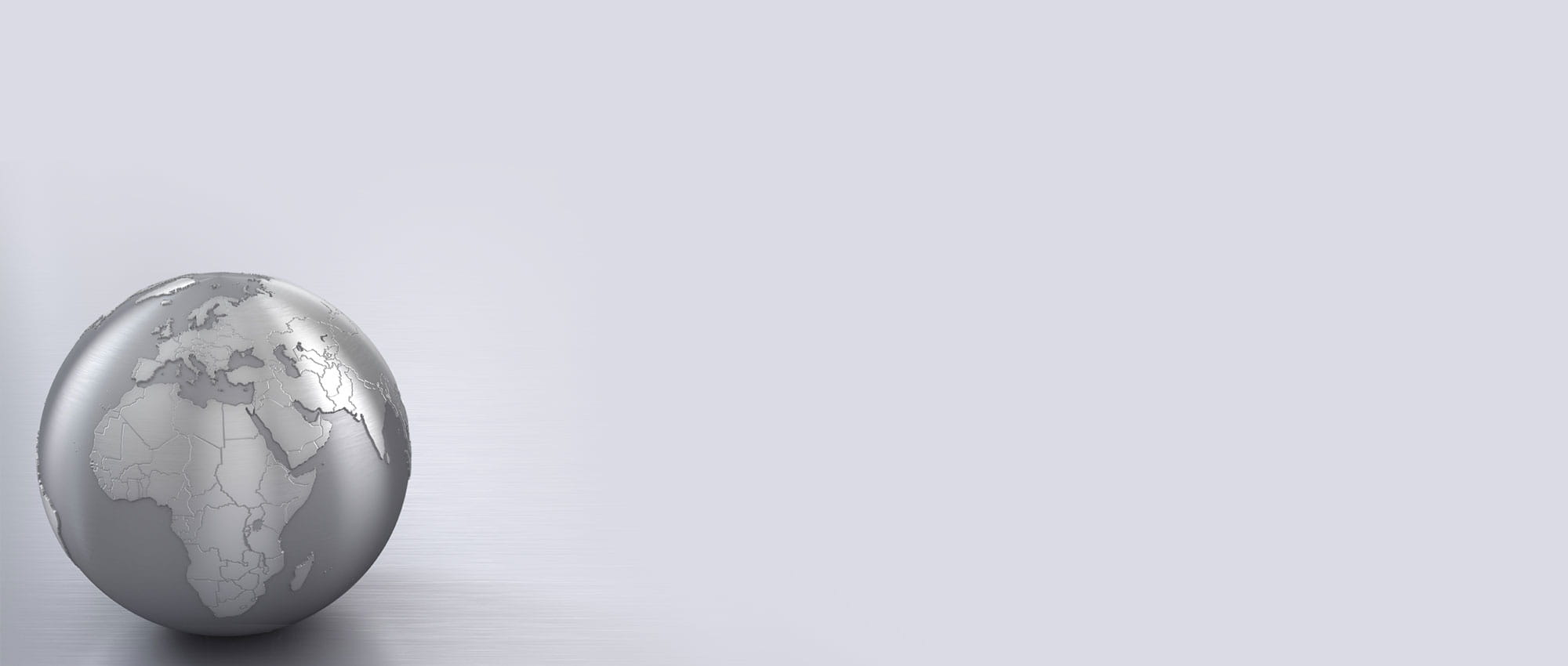
First Hand News
Best of all, keep up with the latest developments
with the Freudenberg Sealing Technologies newsletter.