Obtain news and background information about sealing technology, get in touch with innovative products – subscribe to the free e-mail newsletter.
15.07.2025 | Press release
Breakthrough: Simulation Transforms Seal Development
Weinheim (Germany), July 15, 2025 – The first pressure seal resulting from entirely simulation-based product development – this milestone is the outcome of a collaboration between Freudenberg Sealing Technologies and the central corporate research department Freudenberg Technology Innovation. Compared to previous, conventionally developed versions, this new method has enabled design improvements in key details of the Simmerrings. The result: They easily surpass the demanding requirements of modern hydraulic systems in terms of service life and reliability, leading to longer maintenance intervals and lower maintenance costs.
The new development tool is called FIRS³T, an abbreviation that stands for “Freudenberg Integrated Radial Shaft Seal Simulation Tool”. The experts at Freudenberg Technology Innovation programmed it as a fully coupled EHL (elastohydrodynamic lubrication) simulation model – a highly challenging task, due to factors such as the complex fluid dynamics when the shaft rotates relative to the sealing ring. In this partnership, Freudenberg Sealing Technologies supplied all the practical development parameters for the development of the new pressure seal.
“The simulation model is a milestone in our development process and holds strong potential for future applications,” says Dr. Daniel Frölich, Technical Director of the lead center Simmerring® Industry at Freudenberg Sealing Technologies. “FIRS³T enables us to push physical boundaries and develop seals with even better performance parameters than ever before – and much faster.”
The combined expertise involved in this close collaboration played a key role in achieving this breakthrough. It is also an example of the company’s perseverance in offering its customers innovations with the highest standards: The specialists worked on the simulation model for several years. Now ready for series development, it has already proven its effectiveness.
Innovative radial shaft seal withstands dynamic pressure cycles
The new pressure seal is now available. It is designed for a wide range of hydraulic pump and motor applications operating at varying pressure levels. The seal offers a longer service life and even greater reliability, which translates into lower maintenance costs and longer intervals between servicing. “It has a redesigned sealing lip with an optimal contact width under all pressure conditions. This ensures excellent wear behavior at pressures of up to 5 bar while also providing robust sealing at lower pressures. This ability to withstand dynamic pressure cycles makes the seal ideal for demanding fluid system applications,” Dr. Frölich explains.
A simulated view inside the hydraulic system
Radial shaft seals are a well-established machine component, used millions of times across industries. They ensure both dynamic and static sealing on the shaft. At the same time, they help to distribute lubricant effectively. However, even with all the routine, many aspects of what exactly happens in the contact between the seal and the shaft have been unclear – simply because it isn’t possible to observe the relevant areas in practice. FIRS³T offers a new level of insight through simulation: The powerful tool delivers precise, traceable predictions of the sealing performance under varying loads and conditions, which makes it possible to develop the optimum design and functionality.
To this end, FIRS³T contains considerable and complex knowledge. Numerical descriptions include realistic surfaces in contact between the sealing ring and shaft, macroscopic aspects such as a contact pressure distribution, the distortion of the seal in dynamic operation, and lubricant simulation with viscosity and flow factors on the surfaces. All influencing variables can be adjusted flexibly in the calculation model, offering a simulated view into the system.
Product development in days instead of months
The process also greatly accelerates the development: Only with simulation calculations is it possible to design the seal up to the “design freeze” stage. This only takes a few days. In general, one prototype that is physically validated is now sufficient. This eliminates the time-consuming, labor-intensive and therefore costly steps of multiple prototype iterations with the associated tooling and physical validation, which can take months for complex seals when using conventional methods. It means that FIRS³T significantly reduces time, effort, and cost.
“For the radial shaft seal, the results from FIRS³T closely matched the values actually measured with the prototype seal. This confirms the high reliability of the simulation process,” Dr. Frölich concludes.
FIRS³T is set to be a standard tool at Freudenberg Sealing Technologies in the future. The highly flexible simulation model can be used to develop wind turbine seals, for example. They have a diameter of around two meters, which means high prototype and testing costs. FIRS³T can reduce these factors – but above all, it can offer seal designs with superior performance in this case as well. The experts are continuously refining the simulation model as their practical experience accumulates, so they can obtain increasingly precise information about the sealing performance and properties.
Press Release Downloads
Breakthrough: Simulation Transforms Seal Development
Last update: 15.07.2025
English | DOCX | 278 KB
DownloadDownload Images
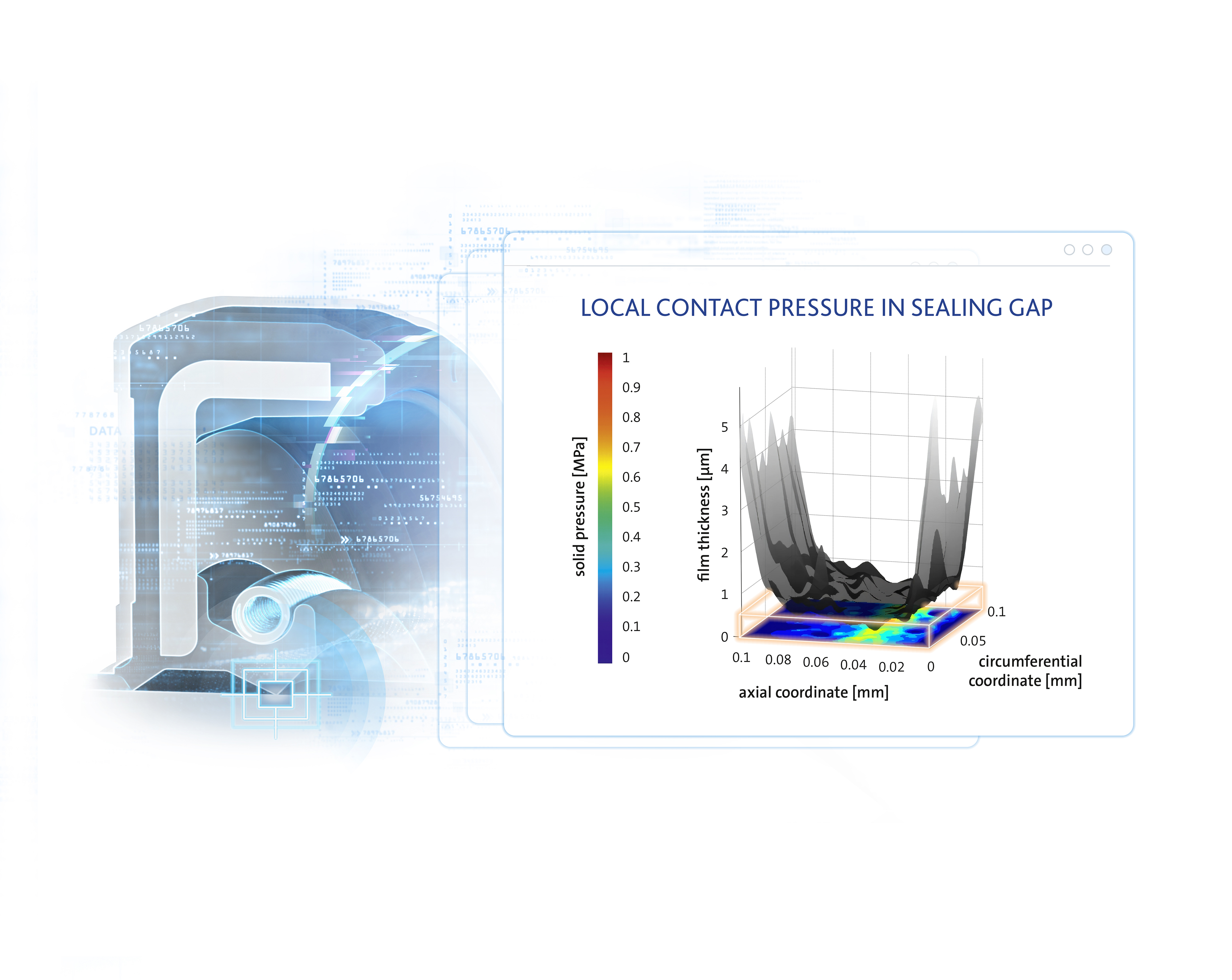
FST Press Image - Simulation-based seal development
FST Press Image - Simulation-based seal development
© Freudenberg Sealing Technologies 2025 | JPG | 2.22 MB
DownloadJosh Barnett
Corporate Communications Manager
Telephone: + 1 734 354 2406
josh.barnett@fnst.com chevron_rightSilke Herzog
Senior Manager Corporate Communications
Telephone: + 49 (0) 6201 960 6385
silke.herzog@fst.com chevron_rightNews Service
You can subscribe to the Freudenberg Sealing Technologies news alert service, bringing you the news as soon as they are published. You can always unsubscribe from this service.
Subscribe now! chevron_rightMore news on the subject Material Expertise
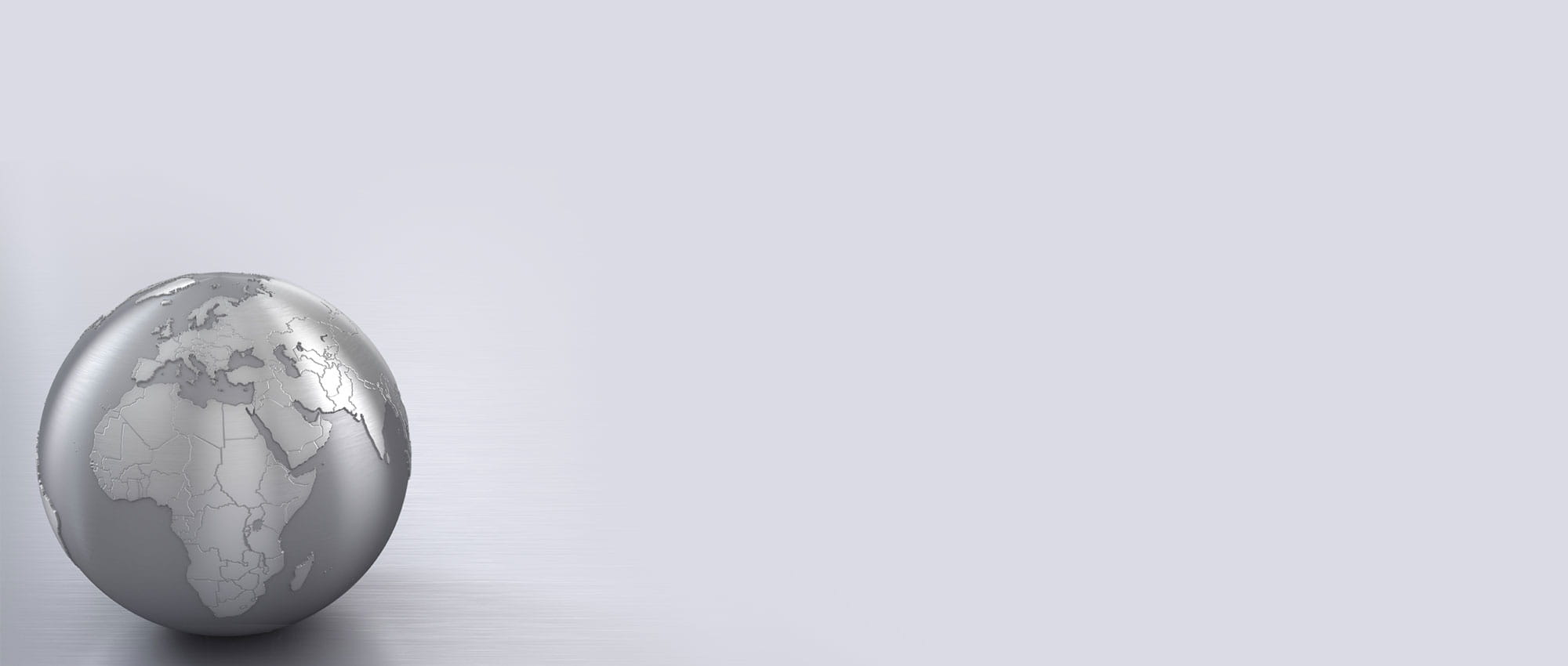
First Hand News
Best of all, keep up with the latest developments
with the Freudenberg Sealing Technologies newsletter.