Obtain news and background information about sealing technology, get in touch with innovative products – subscribe to the free e-mail newsletter.
09.07.2019 | Press release
New Composite Materials for Transmission Components Reduce Friction and Wear
Weinheim (Germany), July 9, 2019. Components made of thermoplastics are mostly produced on the basis of standard compounds. This also applies to high performance plastics (HPP) such as PEEK, a polymer used in applications that produce extremely high operating temperatures. The material developers at Freudenberg Sealing Technologies are taking a different approach and have developed PEEK compounds that are precisely tailored to the respective application. The resulting gear seals and thrust washers are characterized by lower wear, lower friction and lower temperature development.
Off-the shelf material solutions can offer advantages: they are standardized, usually readily available and have already proven themselves in many applications. A standard range of base polymers that are processed with or without commercial fillers is available for simple plastics and technical thermoplastics as well as for HPP materials such as PEEK. Despite their availability, however, these solutions have a significant disadvantage in that material ingredients are not optimized to match specific component and application needs and performance and reliability can be compromised. In light of this situation, the materials researchers at Freudenberg Sealing Technologies have spent several years developing special filler packages for new HPP materials that focus on applications for sealing rings and thrust washers used in automatic transmissions.
The new materials are based on precise knowledge of their application. To optimize the material properties, the experts at Freudenberg Sealing Technologies enrich the base polymer with various ingredients. Fillers such as graphite or glass and carbon fibers, for example, can reinforce the material, reduce friction and wear, or produce conductivity. Additives such as pigments, waxes and stabilizers influence crystallization and flow behavior, while different colors enable the correct assembly of the component. The resulting HPP materials are precisely tailored to address current and even future application challenges.
HPP materials precisely tailored to address current and future challenges
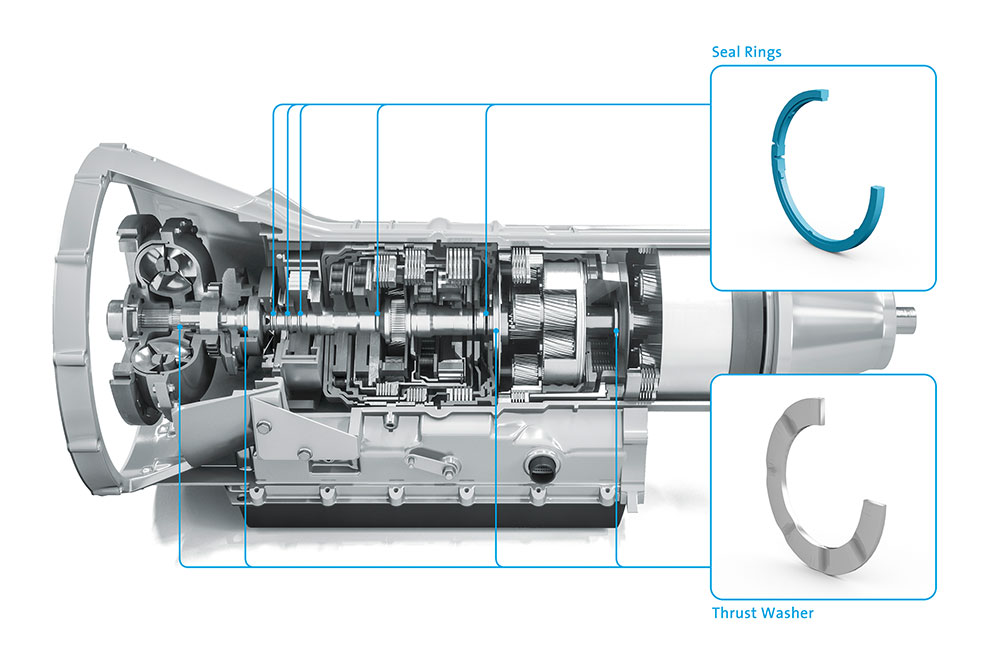
One example is the new material Quantix 55-14, which was developed on the basis of the high performance polymer PEEK. This material is also known as “Low Hardness PEEK” and reduces wear when it comes in contact with steel components. The engineers at Freudenberg Sealing Technologies in Findlay, Ohio, used the material to manufacture sealing rings that function as hydraulic rotary feedthroughs that contain the oil between the clutch and the interior of the transmission shaft in automatic transmissions. The lower incidence of system wear produced by Quantix 55-14 reduces hardness requirements for shafts and lowers customers’ production costs.
Freudenberg’s Levitorq™ thrust washers also use Quantix 55-14. The flat, disc-shaped components are used in torque converters and automatic transmissions where they absorb axial forces from rotating components. Friction needs to be as low as possible in these applications. When the shaft starts to rotate, Freudenberg’s patented groove technology allows fluid to pass under the washer. This creates a hydrodynamic lubricating film that lowers friction and reduces wear in the application. If conditions prevent operation in the hydrodynamic range, the importance of the material’s very low, dry friction will increase durability.
Materials expertise combined with application knowledge
Material experts at Freudenberg Sealing Technologies have conducted comparative wear and friction testing on thrust washers made from Quantix 55-14 and those made from readily available, standard HPP materials designed for applications that require low friction and wear. Thrust washers made from Quantix 55-14 demonstrate a 95 percent reduction in wear, a 55 percent reduction in friction and a decrease in temperature at the interface of 35 °C.
“As these examples show, grabbing a product off the shelf isn’t always the best approach,” says Dr. Christoph Klingshirn, who is responsible for global plastics development at Freudenberg Sealing Technologies. “If materials expertise is combined with application knowledge, this can lead to ever higher performance plastics.”
Ulrike Reich
Head of Media Relations & Internal Communications
Telephone: + 49 (0) 6201 960 5713
ulrike.reich@fst.com chevron_rightNews Service
You can subscribe to the Freudenberg Sealing Technologies news alert service, bringing you the news as soon as they are published. You can always unsubscribe from this service.
Subscribe now! chevron_rightMore news on the subject Technology & Innovation
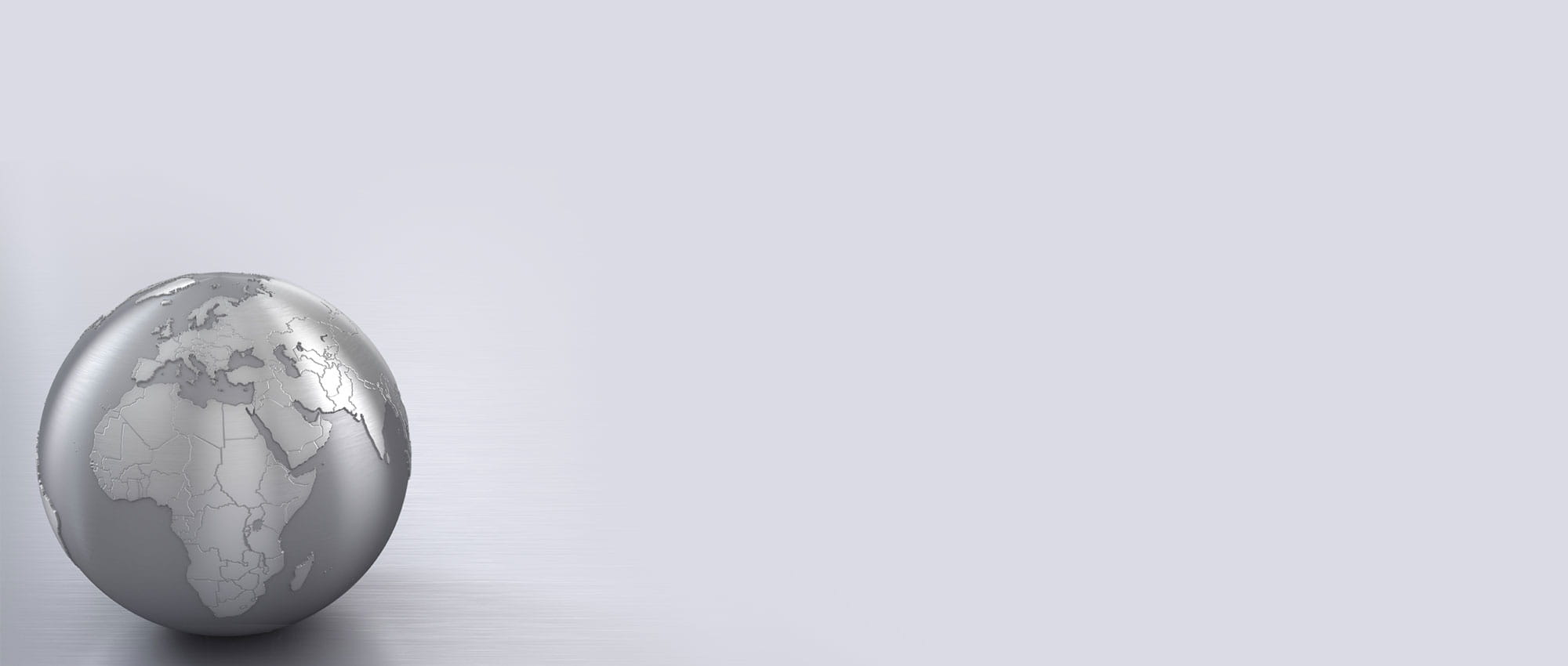
First Hand News
Best of all, keep up with the latest developments
with the Freudenberg Sealing Technologies newsletter.