Obtain news and background information about sealing technology, get in touch with innovative products – subscribe to the free e-mail newsletter.
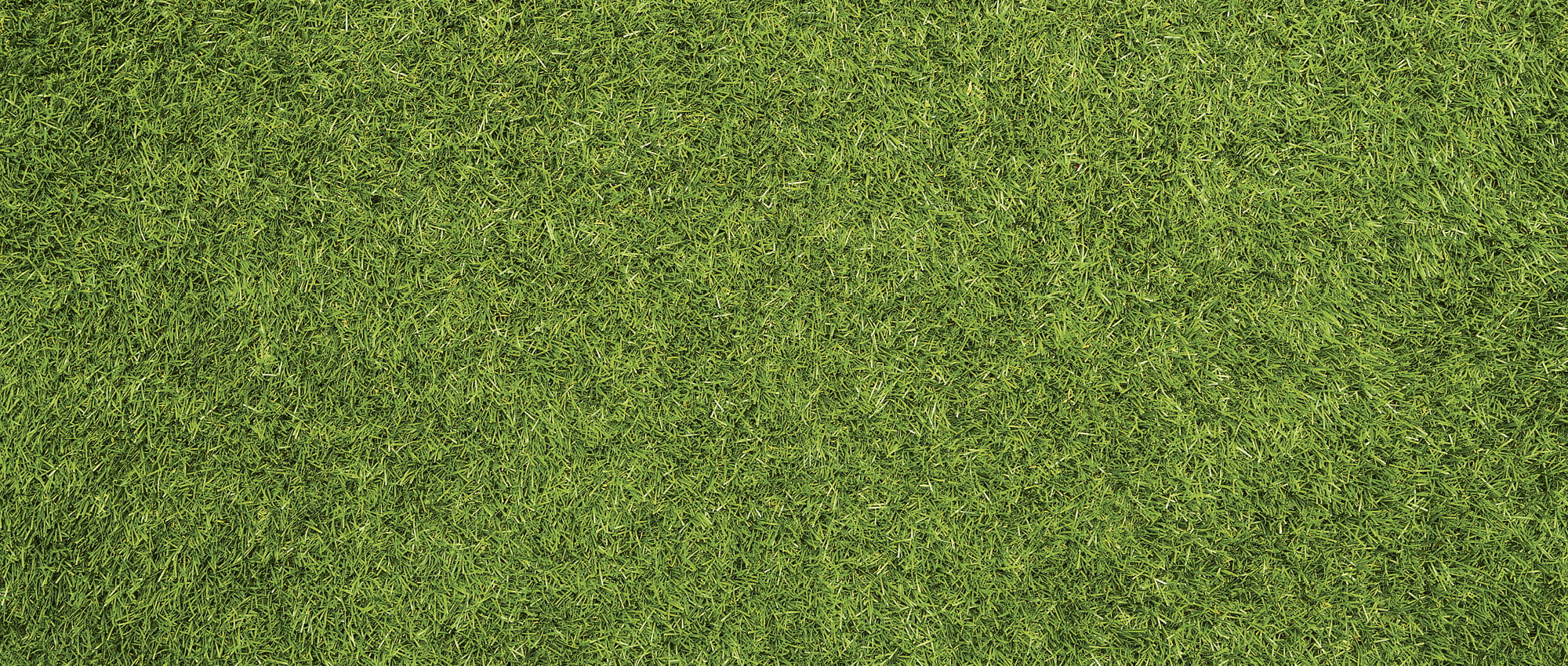
19.11.2024 | Story
Wanted: Innovation for Hydrogen Compressors
Hydrogen must be highly compressed so it can be transported and used. But the process pushes existing compressor seals to their limits. They wear out more quickly than they should. Wanted: a new idea.
About two years ago, customers began telling Dominik Schneider, Segment Manager, Fluid Handling Europe, about a problem. Their compressors, which subjected hydrogen to pressures ranging from 700 to more than 1000 bar, often needed maintenance. It turned out that the seals are exposed to enormous stresses and wear out very quickly. “The users would prefer to service their equipment once a year,” Schneider estimated. The current interval for small, unlubricated compressors is closer to every four months. And every breakdown costs money.
Here we are talking about the famous green field.
Dominik Schneider, Segment Manager Fluid Handling Europe
Hydrogen needs space. In most cases, it emerges from electrolysis at a pressure of about 20 bar. That means it takes roughly the volume of an Olympic pool to store 100 kilograms of hydrogen at this point. That’s too large a volume for transport. The obvious solution is to compress the hydrogen. It is pumped through lines at about 70 bar. At the point of fueling an automobile, if not sooner, the pressures of 700 to more than 1000 bar, cited above, are required. Then a kilo of hydrogen would fit in a typical commercial refrigerator. A variety of different methods and tools can be used to compress hydrogen. One is the piston compressor, a technology that dates back to the 18th century. It can produce very high pressures. But hydrogen is a challenge: The gas has to be compressed in a dry-running process and diffused through metal in the bargain. The high pressure leads to very high temperatures and puts a strain on the seal. There was a reason why Freudenberg Sealing Technologies did not occur to Schneider’s customers at first. “Many people were not aware that we had piston seals in our portfolio,” he said. The quantities also tended to be small, leading customers to source them directly from distributors.
Piston Compressors Are Versatile and Vary Widely
Much like other processes involving hydrogen, it is not clear which technology will prevail. They are versatile, vary widely, and can regulate flow rates. “This makes it possible to repeatedly compress hydrogen to gradually increase the pressure – and do it very elegantly,” Schneider said. But the way seals have been designed so far, they wear out too quickly. What is needed is a new idea, an innovation that charts a new course.
In all probability, the seal for high hydrogen compression would have to be completely reimagined. “Here we are talking about the famous green field,” Schneider said. The functionality would have to be impressive, and none of the options are today. Engineers won’t be getting a finished drawing – they have to set out on their own. “You don’t see much of that.” That means Freudenberg Sealing Technologies can play to its own strengths as a company: a knowledge of materials as well as expertise in design and scaling. And most of all, an inventive spirit.
Wanted: The Right Combination of Material and Design
The design and the choice of material, will likely be the crucial challenges. A combination is needed that produces little wear at high pressures and temperatures, and at sliding speeds up to 5 meters per second. Freudenberg Sealing Technologies has extensive materials expertise, in part due to projects involving high-performance plastics in recent years. Testing is a watchword since the solutions are only possible when there is cooperation with customers. That’s another reason why Schneider is thankful that companies have been approaching him. One thing is clear: “The solution will take time.” It will require tests and trial runs. “With their own tests, it is impossible for customers to know why something doesn’t work – that is our job.” In turn, engineers cannot do their development work without an error analysis onsite when the compressor is in operation. “With our know-how and our technology, we can assess and analyze a great deal ahead of time,” Schneider said.
Freudenberg Sealing Technologies is imposing a restriction of its own on the product, stipulating that it be PFAS-free. That means it will do without per- and polyfluorinated chemicals. “When we are doing the development work, we want to seize the opportunity to keep the production process clean, including the production of materials,” Schneider said. That is just being consistent with the energy source’s promise of a clean future. Schneider is convinced that this promise will soon be a reality. “Hydrogen is here to stay.”
The Future Is Hydrogen
From H₂ Production to Usage: Comprehensive Insights on Production, Distribution, Storage, and Future Applications with Solutions. Explore full spectrum in our webspecial!
Hydrogen Webspecial open_in_newMore news on the subject Renewable Energies
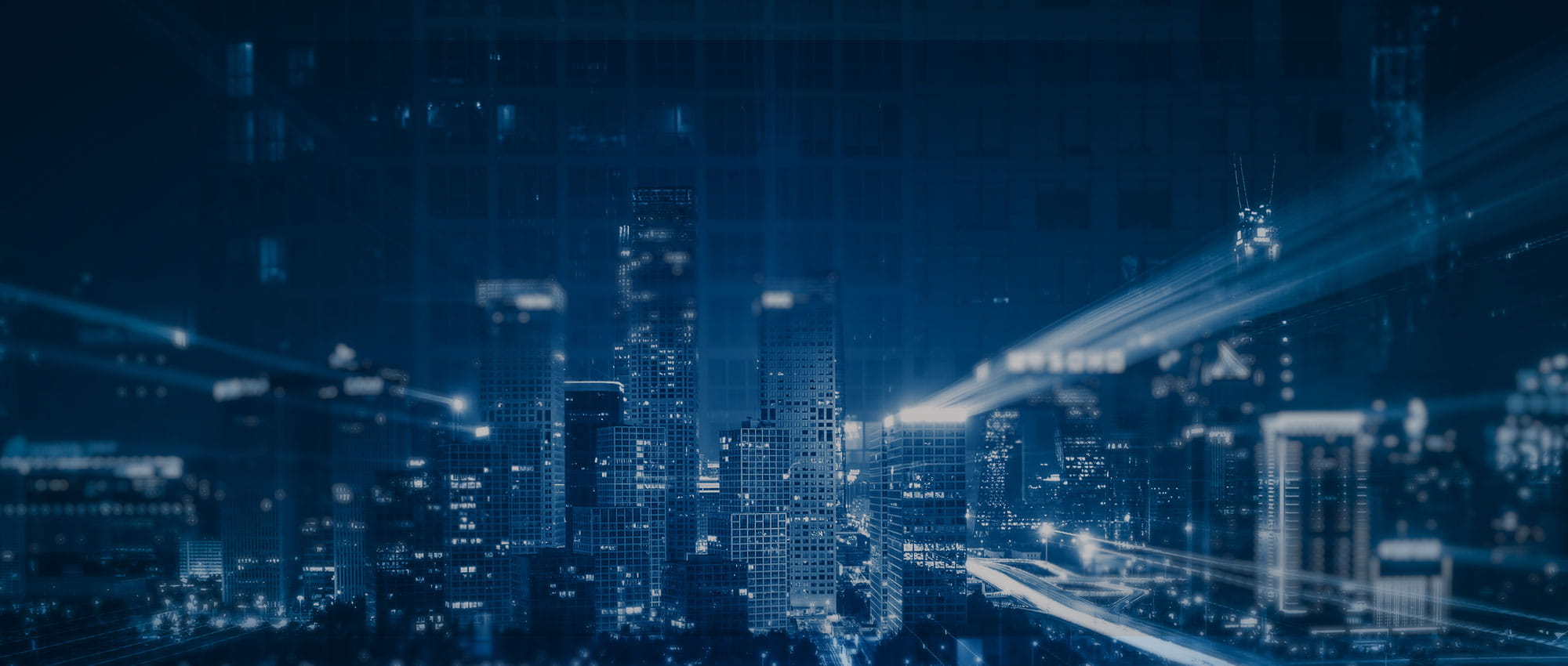
Join Us!
Experience Freudenberg Sealing Technologies, its products and service offerings in text and videos, network with colleagues and stakeholders, and make valuable business contacts.
Connect on LinkedIn! open_in_new