Obtain news and background information about sealing technology, get in touch with innovative products – subscribe to the free e-mail newsletter.
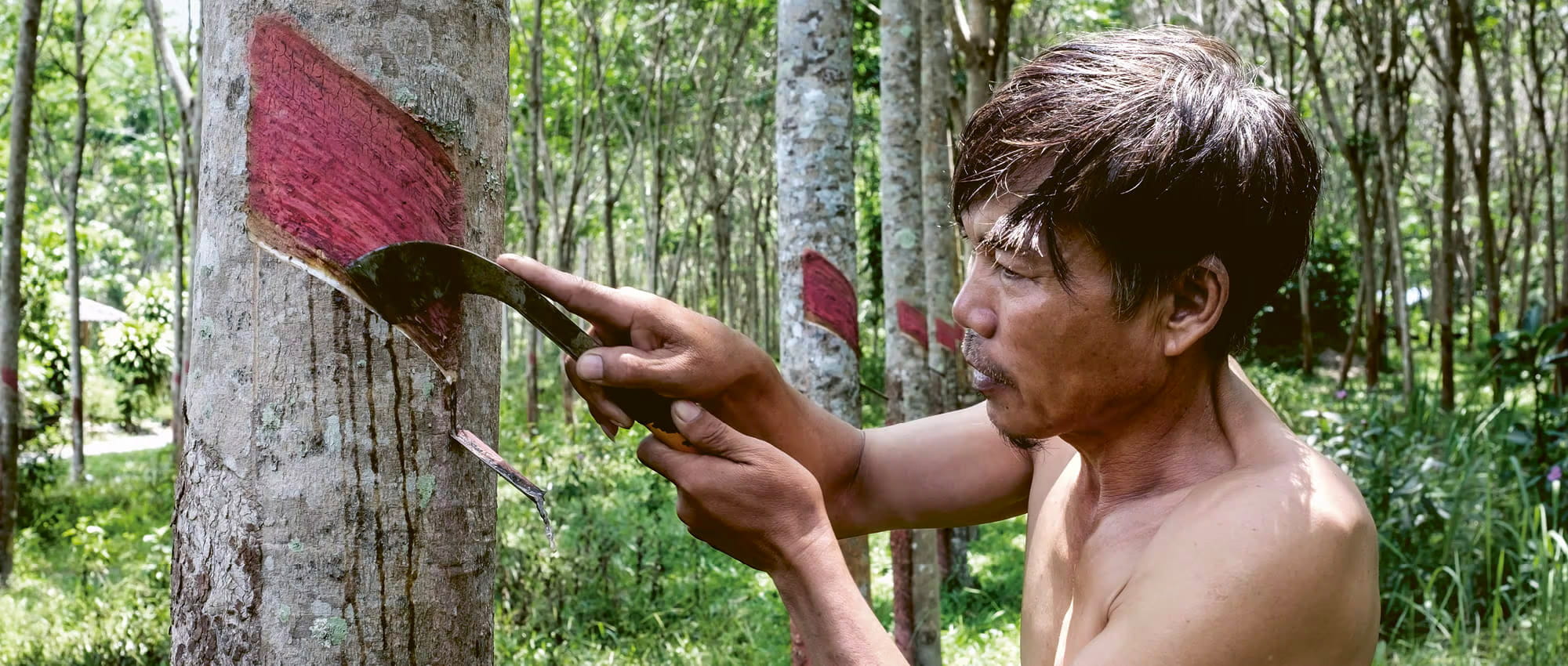
08.03.2022 | Story
A Material From the Bark of a Tree
Natural rubber, sometimes called caoutchouc, is the raw material used in making what we simply call rubber. Thailand is the world’s biggest exporter of natural rubber. It is where the first plantations and producers are turning to sustainable cultivation methods – by abandoning pesticides and monoculture, for example.
The night is pitch black. Only a beam of light from a worker’s headlamp is visible as he makes his way through the high grass to the rows of trees. At the first rubber tree, he carefully draws a fine, diagonal gouge from the upper left to the lower right in its outer bark. The slit immediately fills with a milky fluid that circulates in the capillaries beneath the bark. It drips onto a rail and flows into a plastic bucket attached to the trunk of the tree. The milky fluid is called latex, about one-third of which is natural rubber.
It only takes the worker a few seconds per tree to harvest the material using the so-called “tapping” process. That means he can handle up to 500 trees per night. Hours later, when the early mist rises over the valley at dawn, the buckets are full and the flow has ceased. Latex has to be harvested in the morning before the temperature exceeds 77 °F, explains Sudthida Thantanon, the head of the Phattalung Paratex company. Her firm doesn’t just run the rubber plantation – it exports the latex as well.
The sun is shining at the collection station as the last tappers bring in their harvest – some of them on foot, others by moped from the more distant areas of the plantation. A manager weighs the barrels and draws a sample out of each of them for testing to determine the natural rubber content and quality. The company shares income with the workers, and the measurements are crucial for the tapper’s compensation. Then ammonia is added to the latex to preserve it. An acrid smell immediately wafts through the open space. “Latex spoils quickly – like milk or a curry,” Thantanon says. Now the tappers head off to bed as a tanker truck hauls the latex to the factory, where it is prepared for export and put in barrels.
70 Percent Is Used for Tire Production
Rubber trees grow only in the tropics, and about 80 percent of the global output of natural rubber comes from Southeast Asia. Besides Thailand, the world’s largest exporter, the countries of Vietnam, Malaysia, Indonesia, Cambodia and Myanmar have relatively large market shares. About 70 percent of the global latex harvest is intended for tire production. Other products are rubber components to dampen vibrations in cars, along with mattresses, the soles of shoes, rubber boots and condoms. Under severe stresses, natural rubber is more stable and longer lasting than synthetic versions made from petroleum.
In some countries, primary rainforests have had to give way to rubber plantations.
In the past, the demand for latex-based products has risen steadily. In some countries, primary rain forests have been forced to give way to rubber plantations. As a result, this natural raw material gets more attention when the topic of sustainable supplier chains comes up. The clearing of rain forests is supposed to be avoided as much as possible and the cultivation of the land is expected to become more environmentally friendly. But this isn’t easy to monitor: According to the World Wide Fund for Nature (WWF), small farmers produce 85 percent of the world’s natural rubber. That figure is 93 percent in Thailand, according to the natural rubber importer Weber & Schaer, who has worked with Phattalung Paratex for years. The Thai company obtains latex from a number of these small operations since its own plantation is unable to fully cover the demand.
Forgoing Pesticides
Sudthida Thantanon likes the idea of greater sustainability. She hasn’t used pesticides at the plantation for two years. The family-owned company is working to earn a certification – a newly introduced natural rubber seal of approval from the Forest Stewardship Council (FSC). Next year, the company will be undergoing a preliminary audit to become more familiar with the requirements. She notes that the company is already meeting many of the potential conditions. Besides doing without pesticides, they include trash separation and wastewater treatment. The company recycles all usable byproducts – from latex skin to rubber foam, which is separated at the company’s treatment plant. Old trees are cut down and the wood is sold to furniture-makers and other companies. Thantanon would like her suppliers to earn the FSC seal as well. Weber & Schaer also helps the plantations out financially during audits.
Farewell to Monoculture
As a rule, natural rubber is cultivated as a monoculture. Using pesticides on a large scale, farmers do battle against the high grass where snakes can hide. But that displaces other plants along with the animals that feed on them. The naked ground is less effective at holding moisture and is susceptible to erosion. On Thantanon’s plantation, on the other hand, the spaces between the rubber trees are filled with small palm plants, vines, medicinal herbs and wild ginger, whose blossoms provide pollen for bees. At one time people didn’t care about pesticide use since latex is not a food, she explains. “No one was thinking about the health of the workers who are inhaling the pesticides – or the fact that rain washes pesticides into rivers.” But the conversion comes at a price. To buy pesticides, it cost the entire plantation the equivalent of 300 euros a year. But now Phattalung Paratex pays twenty times that amount to have the weeds cleared manually.
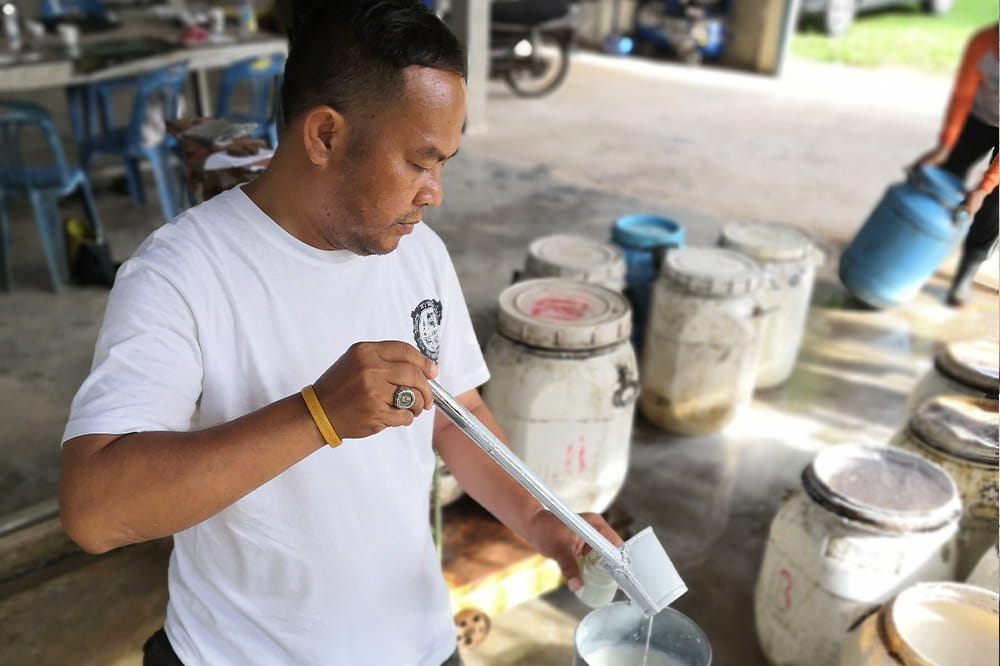
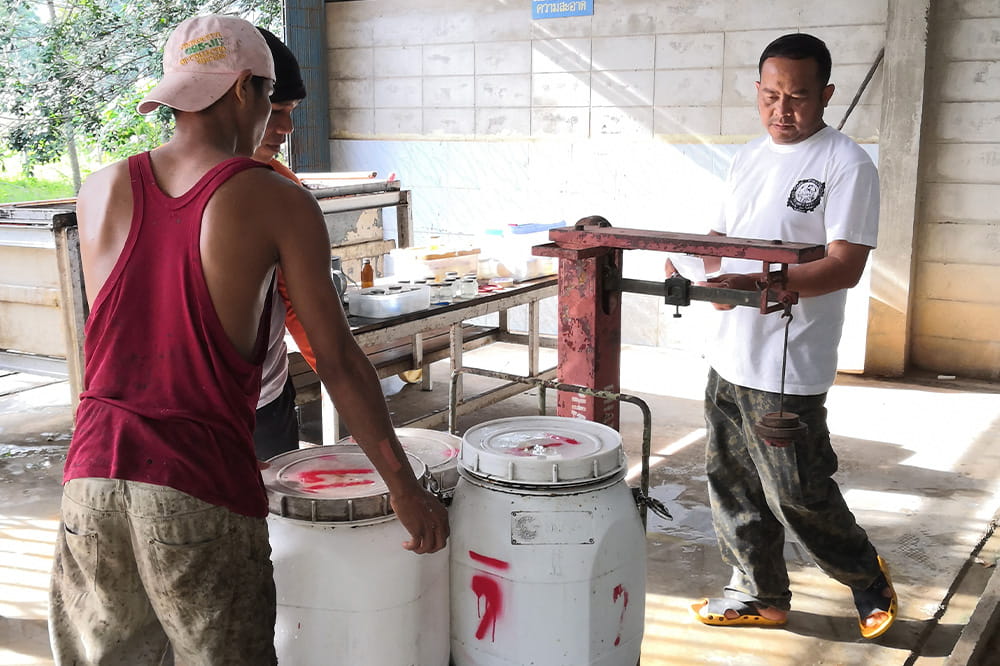
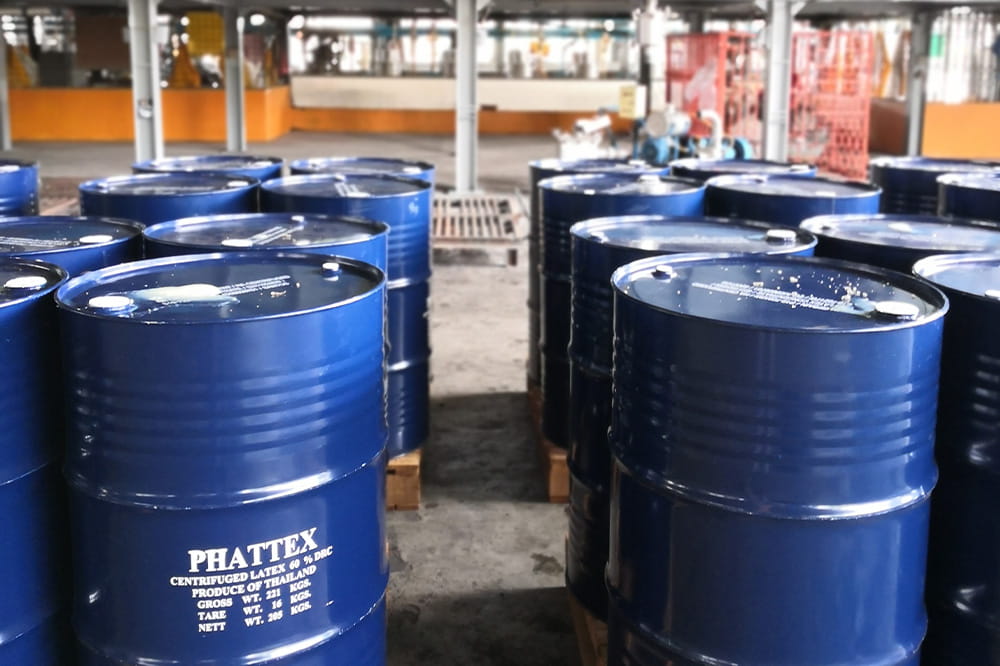
Farmers are grappling with low rubber prices.
Thantanon actually has a very different goal: to bid farewell to monoculture. In the village of Tambon Kampengphect, she is standing with a group of farmers at a plantation that looks a lot like a garden. Bamboo bushes, leafy vegetables and young Hopea trees are growing among the rubber trees. The Hopea trees will one day grow nearly 150 feet into the air. Bees live in wooden boxes and produce a fine, light, tart honey. Everything is greener and moister than what you see in traditional rubber plantations. A neighbor, Niran Suwarno, was the first farmer to plant Hopea seedlings between the rubber trees, launching a village co-op for a “rubber forest garden” in the process. The government provided the seedlings at no charge. “The others saw the result. I now plant several kinds of trees for wood, peppers, herbs, vegetables and fruit,” says Suwarno, who is often invited to give presentations on his project.
Research on Suitable Crops
Thantanon would like to see the co-op supply her company, and she is learning from it in the meantime. Two months ago, in an area cleared of older trees, she began planting new seedlings further apart to create more space for other plants. The first small rubber plants, each less than two feet high, are concealed in the high grass. A soil analysis will indicate what other crops are suited to mixed cultivation here. Teaming up with Weber & Schaer, Phattalung Paratex is supporting the cooperative’s biological research project, which gives farmers insight into crop selection. Aside from an improved natural environment, the project develops additional sources of income for the farmers.
This is important since farmers are grappling with low rubber prices. The uncertain global economic outlook is again depressing demand – and thus prices on the natural rubber exchanges in Tokyo and Singapore. It is difficult to get customers to pay a surcharge for sustainable agriculture. “It takes a great deal of persuasion,” Thantanon said. But she is convinced that a forest garden with rubber trees and numerous crops is the right path to the future.
Copyright: Adirekjob / Istockphoto, Gastuner19 / Istockphoto, Christiane Kühl
More news on the subject Sustainability
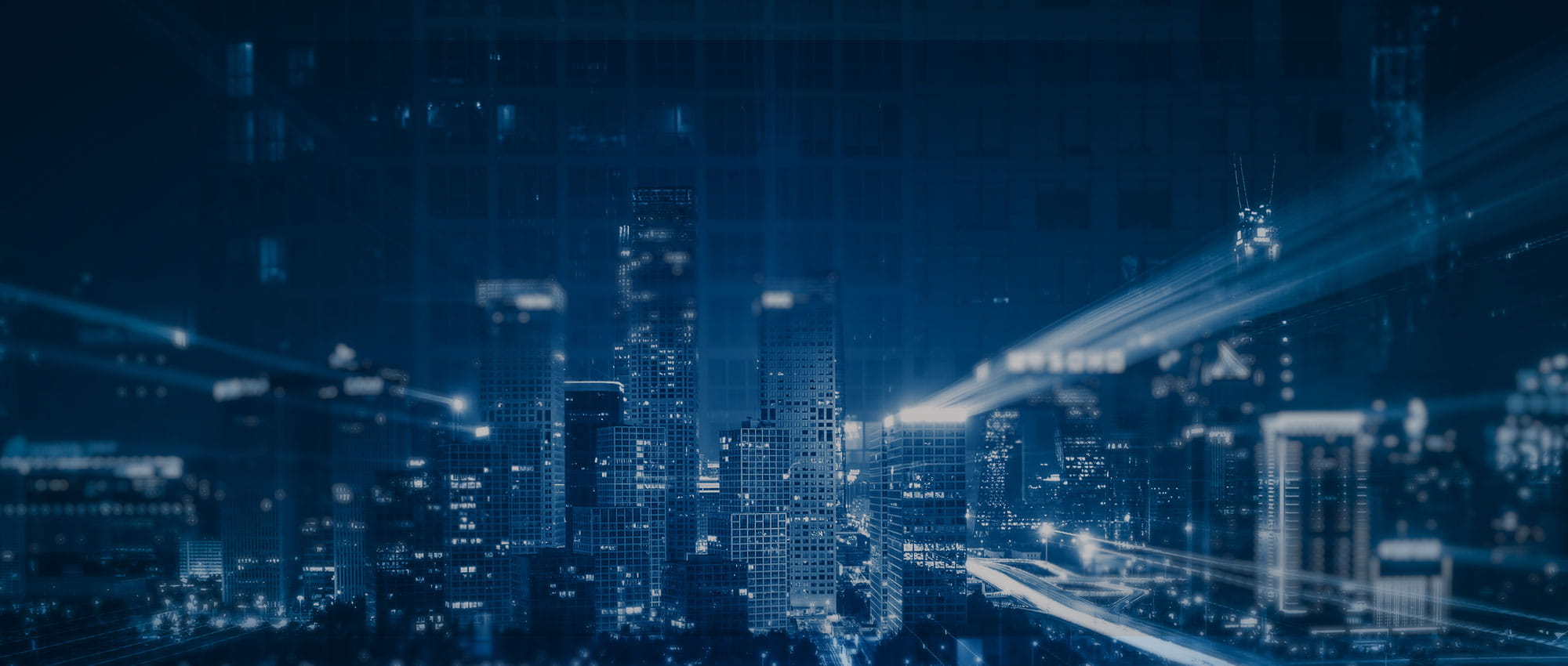
Join Us!
Experience Freudenberg Sealing Technologies, its products and service offerings in text and videos, network with colleagues and stakeholders, and make valuable business contacts.
Connect on LinkedIn! open_in_new