Obtain news and background information about sealing technology, get in touch with innovative products – subscribe to the free e-mail newsletter.
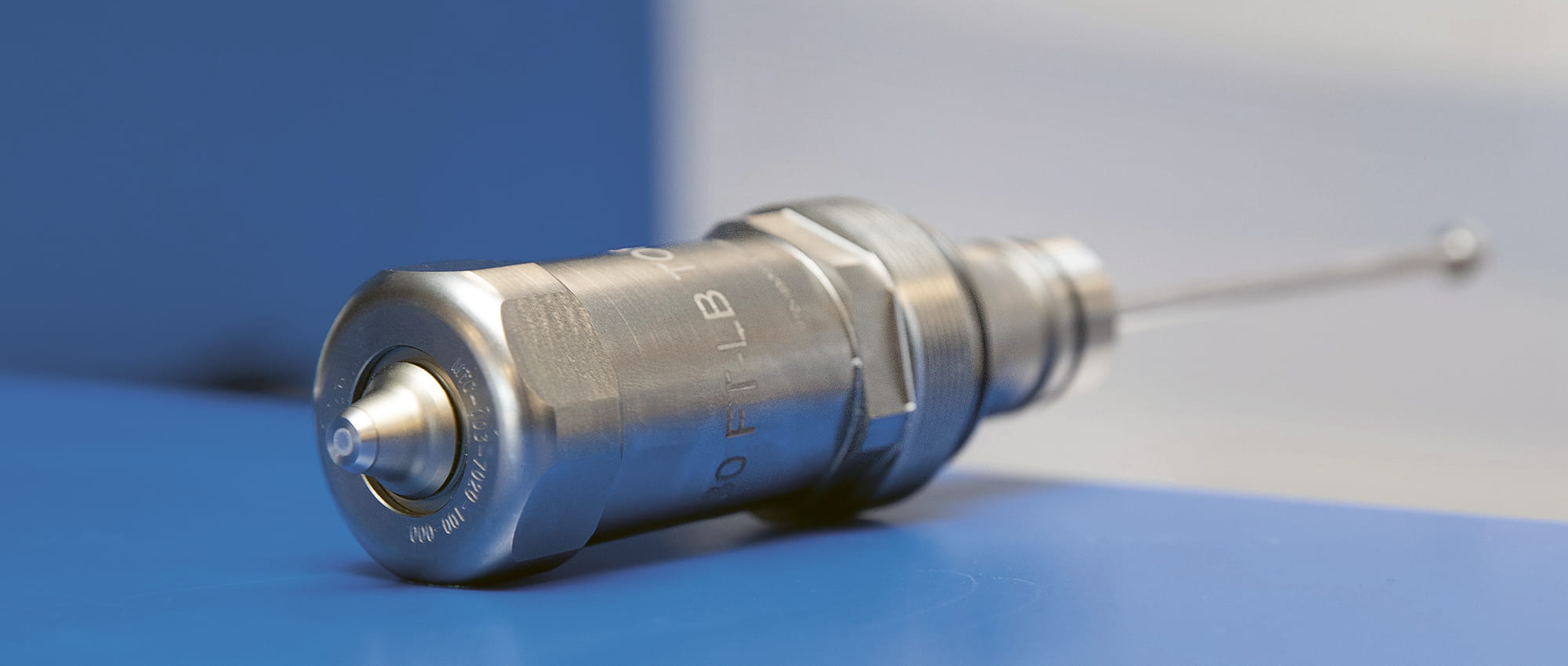
17.07.2022 | Story
With a Cold Runner
Though only used in the United States initially, a new injection molding technology has now spread to many other Freudenberg Sealing Technologies plants worldwide. The example shows that, when every cent counts, technologies that conserve resources pay off.
“Live free or die.” The phrase has only been the official motto of the state of New Hampshire since 1945, but it dates back to the time when the United States was founded. Robert Scavuzzo is responsible for developing new production technologies at Freudenberg Sealing Technologies. In his office, there are always a few signs bearing the motto on his bookshelf. He presses them into the hands of his visitors as they leave. Scavuzzo, who descended from German and Italian immigrants, has personally seen how the combination of freedom and hard work can lead to social advancement. For him, the American dream is still alive, as it is for many people throughout the world. In 2019, according to a survey by the Pew Research Center, more than 44 million people born in another country were residing legally in the U.S.
But the gleam of the star-spangled banner has paled in some parts of the world. No particular president is to blame either, but rather the enormous consumption of resources by the West’s leading power. The typical American generates about four times the global average for carbon dioxide emissions per capita. When it comes to water consumption per capita, the U.S. is the record-holder among OECD countries, a tribute to farming on formerly arid landscapes. To many Europeans, life in America is an example of how not to live a sustainable lifestyle. One suspicion is that a lack of regulation is the main reason for the country’s profligate use of resources.
But as with so many stereotypes, this one fails to grasp every facet of the situation. CO2emissions per capita may be high in the U.S., but the country has recently seen the greatest decline in this metric among all industrialized countries. This is not the result of billions in subsidies for renewable energy but solely due to the switch from coal to less expensive natural gas, which is extracted domestically. The world’s largest electric car manufacturer is not based in Germany, where an official government platform is tackling the mobility of the future, but in California – which has championed air purity for decades.
In turn, freedom is a key condition for an innovation to emerge in the first place.
Avoiding Scrap
That brings us back to the office of Robert Scavuzzo as he passionately explains a complex technical process used in the production of seals. The raw material, an elastomer, is heated inside a cylinder and transformed into a fluid. Then, it flows through a closable nozzle down into a tool not unlike a baking mold. The technology is called valve-gated cold-runner injection. Without the precise operation of the valve gate, small sprue marks are formed in each operation that have to be removed from the cured product. Since individual elastomer molecules cross-link during the curing – the only way to achieve the desired elasticity – the scrap cannot be recycled directly. It is mostly incinerated, releasing its carbon content as CO2. With Freudenberg Sealing Technologies now using the process in its plants worldwide, it is eliminating about 70 tons of scrap each year and emitting 600 tons less CO2.
The Freudenberg plant in Manchester, New Hampshire, is the lead facility for the valve-gate cold-runner injection molding technology. Manchester is a livable city of 100,000 where the company manufactures engine seals and valve stem rings, among other products, producing volumes in the millions. The technology was developed and introduced about 20 years ago. “Our customers are extremely price-sensitive,” explains Robert Lidster, the division’s technical director. “But if we can avoid engineering waste, we are not only improving the environment but we can offer our products at lower prices.” But it is also true that the valve gate technology comes with a higher price tag compared to traditional cold-runner tools. So, in Manchester, a separate decision is made for each product as to whether or not the cold runner valve-gate technology comes into play. There is a simple rule of thumb: the higher the volume and the bigger the product, the greater the savings, and the sooner a more expensive tool is amortized. Lidster points to another advantage as well: “Product quality rises because no excess material can flow back through the closed nozzle. That could otherwise potentially lead to unevenness in the structure of the material.”
Computer-assisted Progress
The success of the cold runner technology is no reason for Scavuzzo, an engineer working on advanced developments, to rest on his laurels. In recent years, much of his work has involved optimizing the geometry of the channels. “Here we used the kind of computer-assisted processes for fluid calculations that are used to design turbochargers and aircraft turbines.”
The result: It now takes up to 35% less pressure to move the raw material through the now-rounded channels. This in turn saves energy and promotes a more even flow. A new generation of the valve drive is still in development. To this point, the valve has only been able to open and close at predetermined intervals. But, as in vehicle engines, a variable valve control system could offer major advantages. “With a servo drive, we could control the opening of the drive almost at will,” Scavuzzo said. “This would make it possible for us to adjust the process to changes in conditions at any time.” It is an Industry 4.0 technology that is also sparking interest in Freudenberg Sealing Technologies factories in Germany. The example of the cold runner technology illustrates how quickly a technology that from an ecological standpoint can make headway, but its spread mainly depends on whether it offers economic advantages, too. In turn, freedom is a key condition for an innovation to emerge in the first place.
This article originally appeared in ESSENTIAL, Freudenberg Sealing Technologies’ corporate magazine that covers trends, industries and new ideas.
More news on the subject Technology & Innovation
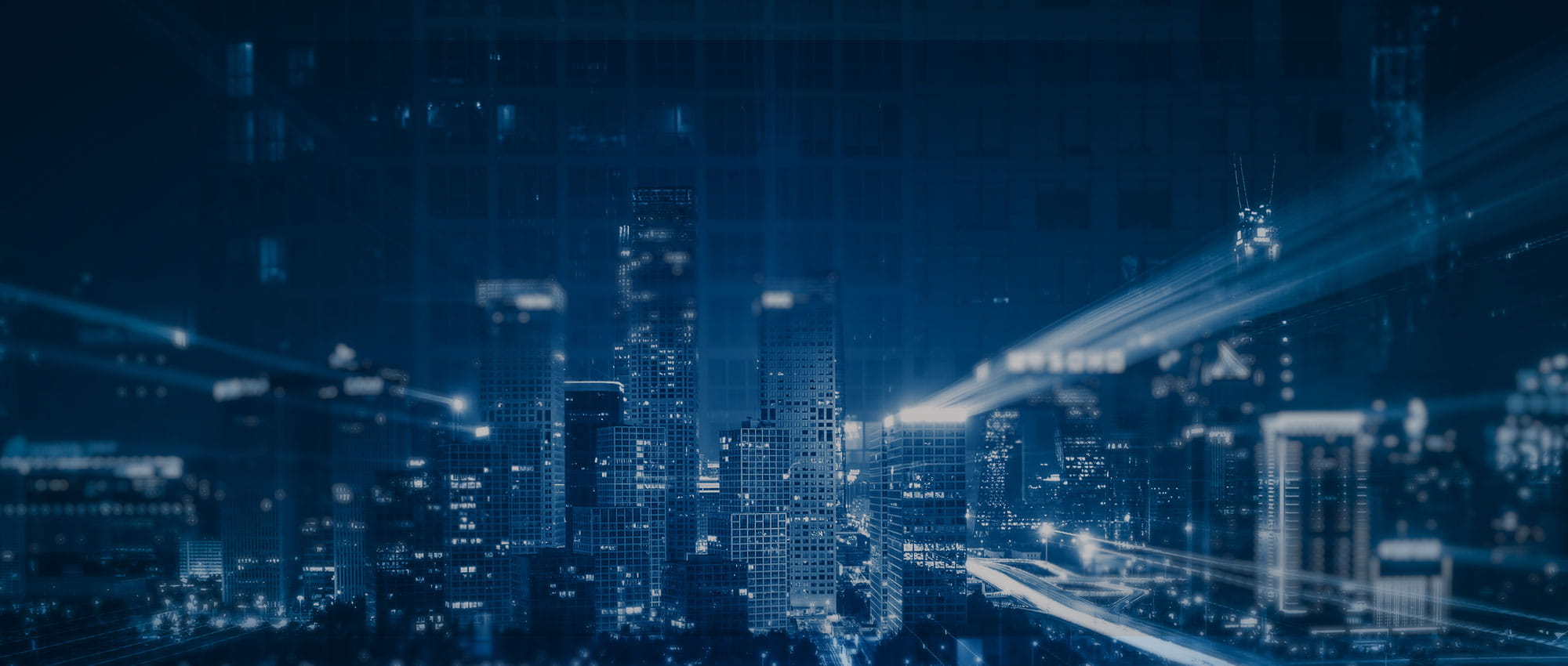
Join Us!
Experience Freudenberg Sealing Technologies, its products and service offerings in text and videos, network with colleagues and stakeholders, and make valuable business contacts.
Connect on LinkedIn! open_in_new