Obtain news and background information about sealing technology, get in touch with innovative products – subscribe to the free e-mail newsletter.
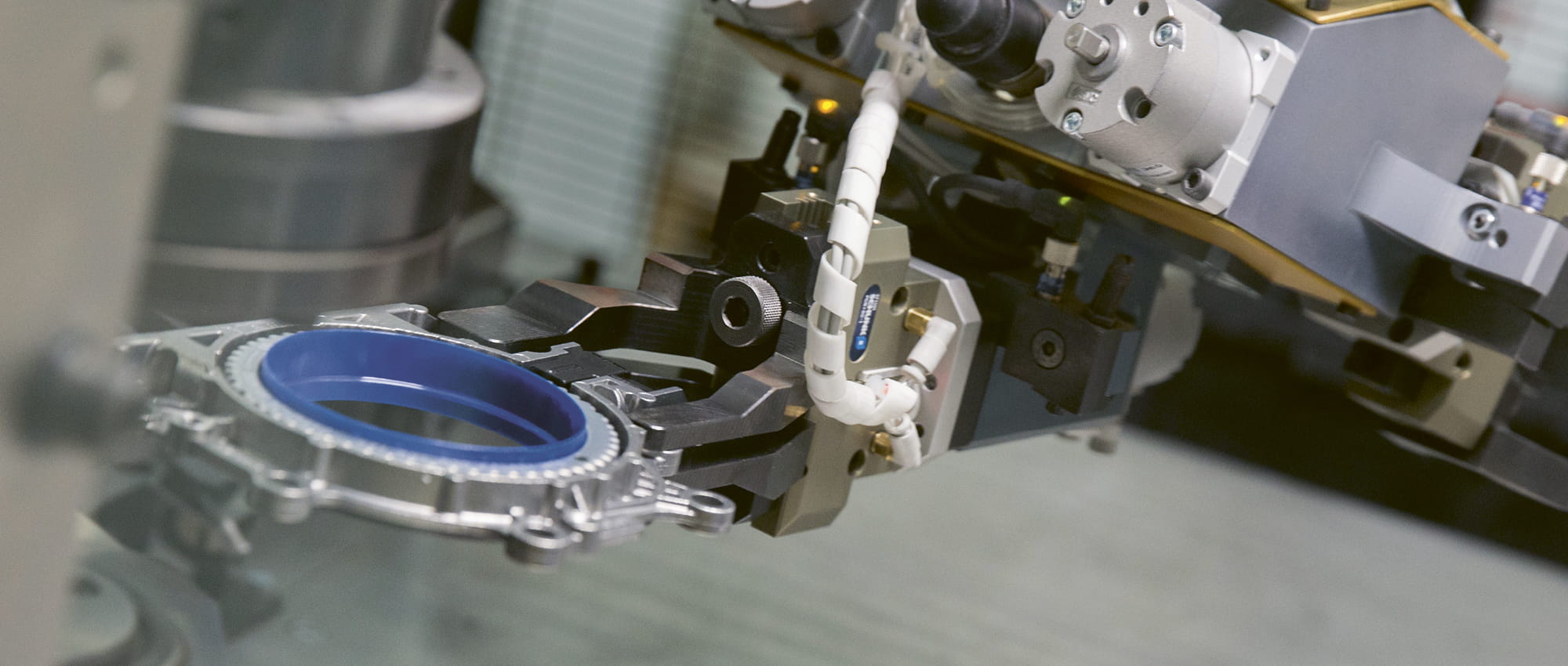
30.03.2021 | Story
Friction-Free Process
With its innovative Levitex mechanical face seal, Freudenberg Sealing Technologies seals the crankshaft almost without friction. It helps to reduce fuel consumption and CO₂ emissions. Series production of the seal takes place at the Pinerolo plant in northern Italy. Important factors: the greatest possible automation and integrated quality control.
The small Italian city of Pinerolo in winter. The Cottian Alps rise in the southwest. The nearly 4,000-meter-high Monte Viso is still snow-covered. The air is cold and clear, and the sun shines low in the valley. On the way to Freudenberg Sealing Technologies’ Piedmont facility, you have to pay attention. The puddles in the road have frozen, and tires keep losing their grip. There are times when friction is crucial. At the Pinerolo plant, however, Freudenberg engineers help to avoid friction, not in tires but rather in the engine compartment, at the transition between the engine and the transmission. Friction is undesirable there. It transforms valuable torque into lost waste heat. A few years ago, series production for totally friction-free seals for crankshafts started in Pinerolo. The primary objective of these mechanical face seals, whose trade name is “Levitex,” is to cut vehicles’ fuel consumption and emissions.
From Pinerolo to the World
In late 2016 at the Pinerolo facility, Freudenberg Sealing Technologies put a manufacturing line into operation for short production runs of Levitex seals. Since then the cooperation with a major European automaker lead to the further development of the seals to series readiness. Since 2010, Freudenberg Sealing Technologies had been involved in intensive research on the new technology. From January 2016, the production of prototypes followed on its own production line to validate its production goals with real components, resulting in the automation of the production. In all, seven robot arms are in use at the production line’s individual stations. Since the robots always carry out the individual work steps in the same way, the assembly process can be effectively replicated. That was crucial since the Levitex seal production had to be rapidly transferred to other assembly lines.
The design of the new Levitex seals imposes very high requirements: The material composition must be exactly right, and the geometric form must strictly be adhered to. That is why there are quality checks incorporated at several points in the production process. After each assembly step, laser sensors in the subsequent equipment precisely measure the geometry and position of the particular component. To some extent, that means the production process is self-monitoring. In a separate work step, the engineers also use a tool called an interferometer to check the condition of the ring surfaces. When the assembly is complete, a leakage test is carried out with air to ensure the component’s reliable operation.
Levitex, the seal with the cushion of air
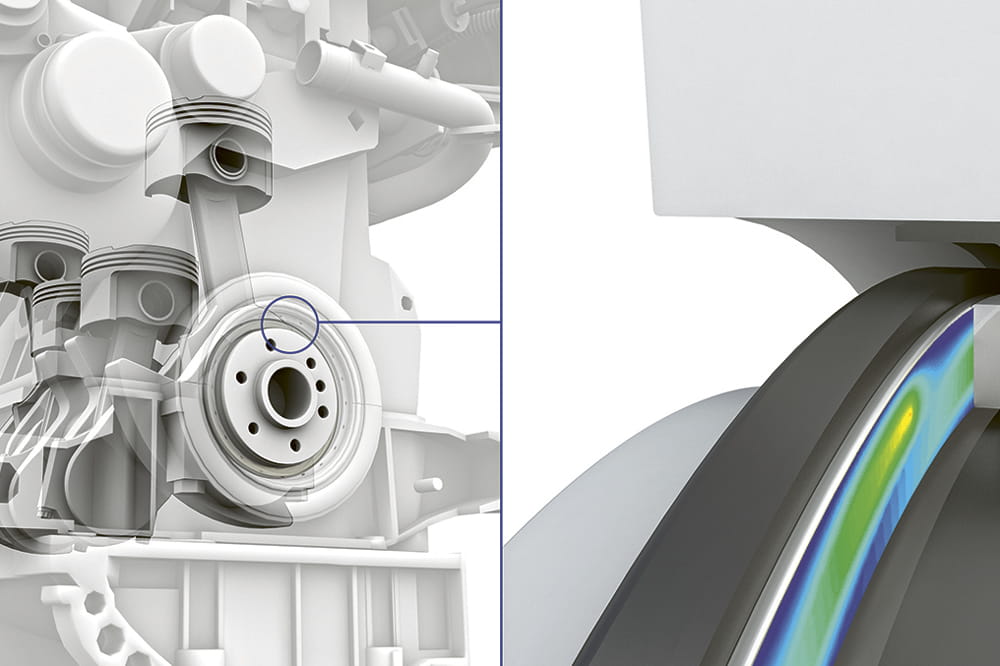
Lifting and floating: As soon as the crankshaft rotates, the Levitex seal builds up a cushion of air.
In every internal combustion engine, seals ensure that oil stays in the engine compartment. An important sealing point in this system is the transition from the engine to the transmission, where the crankshaft is closed off with a ring seal at the crankcase. This is exactly where the new Levitex seals are used. At their core, they consist of two metal rings, one of which is firmly connected to the crankcase and the other to the crankshaft. The surfaces of the rings have small indentations with a depth of only a few microns. When the crankshaft rotates, the surrounding air is pressed into the indentations; the result is a cushion of air that separates the sealing surfaces from one another and enables a nearly friction- free rotation of the shaft – this saves fuel and reduces CO2 emissions. At the same time, to reduce the crankcase’s vibrations and guarantee a functional air cushion, the carrier housing for the static metal ring is equipped with a rubber spring. When the shaft is no longer rotating, the metal rings close, preventing the escape of oil from the engine compartment during the stoppage. So that this occurs completely reliably, the mechanical face seals are given an additional coating. Previously, gas-filled ring seals were only used in large industrial equipment. It was only their design, patented by Freudenberg Sealing Technologies, and the associated production processes that made it possible to transfer the idea to vehicle engines, where very little space is available for mounting.
Technically Demanding, but Easy to Assemble
The numerous quality checks are necessary because the assembly process has many separate steps. The company settled on a decentralized approach with the maximum simplicity, in which the individual production modules work independently of one another. Each individual module is laid out so that it can execute its particular work step as effectively as possible. As a result, these technically demanding seals can be produced with a relatively simple architecture.
Measuring and Testing: In order to rule out errors in the many steps involved, several quality checks are built into the process.
But the production data are then consolidated centrally: After assembly, a laser engraves a serial number on each separate seal ring, under which individual product characteristics such as surface condition, geometry, weight and date of manufacture are recorded. The possibility of tracing every single product is a special feature and was a main requirement for production planning.
Customer Requests Realisable
Modular assembly offers still other advantages by making it possible to integrate customer requests into the production process relatively easily. For example, the sealing rings are equipped with an extra sensor, which passes an electric signal on to the engine control unit for positioning. Thanks to a modular approach, it was possible to effectively carry out this specification and set up an anti-static area, which it required, within the production line. For the layout of final assembly, the Pinerolo engineers learned from experiences with similar approaches used at other Freudenberg Sealing Technologies facilities, such as those of their colleagues at Langres, France, where crankshaft seals are also produced. In any case, the new sealing ring is having a measurable effect. The potential savings due to reduced friction on the crankshaft are up to 1 gram per kilometer driven. That adds up quickly – and takes on even greater significance in light of demanding CO2 goals. Ideally, friction should only occur where it is really needed.
This article originally appeared in ESSENTIAL, Freudenberg Sealing Technologies’ corporate magazine that covers trends, industries and new ideas.
More news on the subject Sustainability
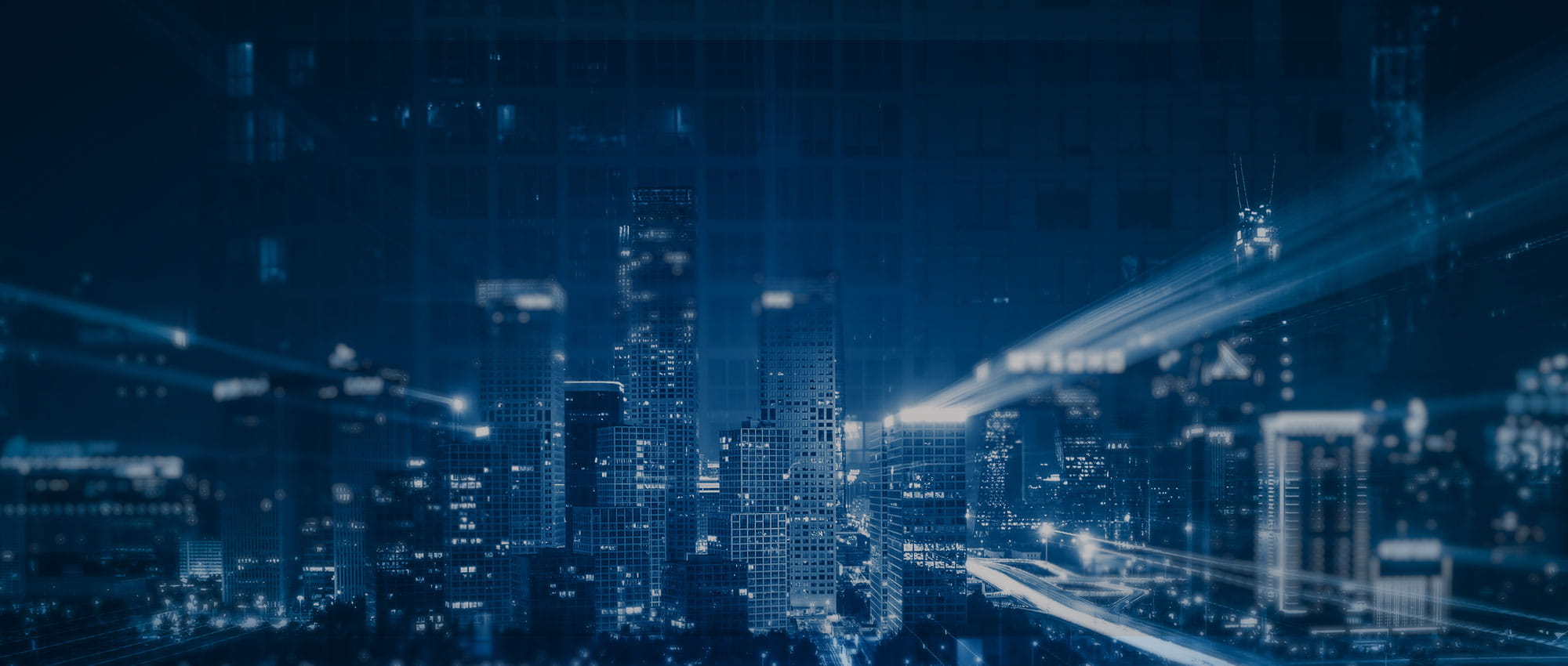
Join Us!
Experience Freudenberg Sealing Technologies, its products and service offerings in text and videos, network with colleagues and stakeholders, and make valuable business contacts.
Connect on LinkedIn! open_in_new