Obtain news and background information about sealing technology, get in touch with innovative products – subscribe to the free e-mail newsletter.
09.06.2020 | Press release
High Pressures? No Problem!
Weinheim (Germany), June 9, 2020. With the introduction of a new single-seated valve, Italian valve manufacturer Bardiani Valvole has launched the first and only high-pressure valve available for hygienic applications certified according to global 3-A® Sanitary Standards. Freudenberg Sealing Technologies worked closely with Bardiani Valvole to engineer a unique seal that supports this new valve design.
Valves are indispensable components in the hygienically sensitive systems used in the food, beverage and pharmaceutical industries. Until now, there were no high-pressure valves available for food-product contact applications that conformed to 3-A® standards. These global hygiene standards address the design and manufacturing of components that come into contact with food.
The seal developed for this new valve design had to similarly meet 3-A® sanitary requirements. Bardiani Valvole approached Freudenberg Sealing Technologies for help in developing a solution to tap into its material expertise. As a result of joint cooperation, Freudenberg engineers developed a main rod seal that was both 3-A® compliant and capable of handling high-pressure of up to 150 bar that the customer’s valve required. The main rod seal incorporates proven Freudenberg technology with advanced component design in an entirely new combination that is also compatible with other industrial high-pressure valves.
Prototypes produced without any tools
The 3-A® compliant main rod seal combines a sealing lip, manufactured from EPDM 302 or Fluoroprene® XP 43, with a backup ring made of PTFE. Freudenberg’s product engineers were inspired by the design of a proven shaft seal and an O-ring with a backup ring. In order to meet development and cost deadlines, the team initially produced one-off prototypes to share with Bardiani Valvole using the unique capabilities of Freudenberg Xpress®, a fast turnaround, high-quality manufacturing service that can generate custom seals in as little as a day. It offers machined seals made of original materials and original profiles for prototypes, spare parts or economical small series.
By eliminating the need to set up manufacturing tooling to produce sample parts, this results in considerable cost and time advantages for the customer. Thanks to special turning and milling techniques individual designs can be exactly realized. The tailor-made sealing solution for the new high-pressure valve could also be produced economically in an extremely short time. The Freudenberg Xpress® Service is represented at numerous Freudenberg sites worldwide, enabling rapid delivery of spare parts, for example.
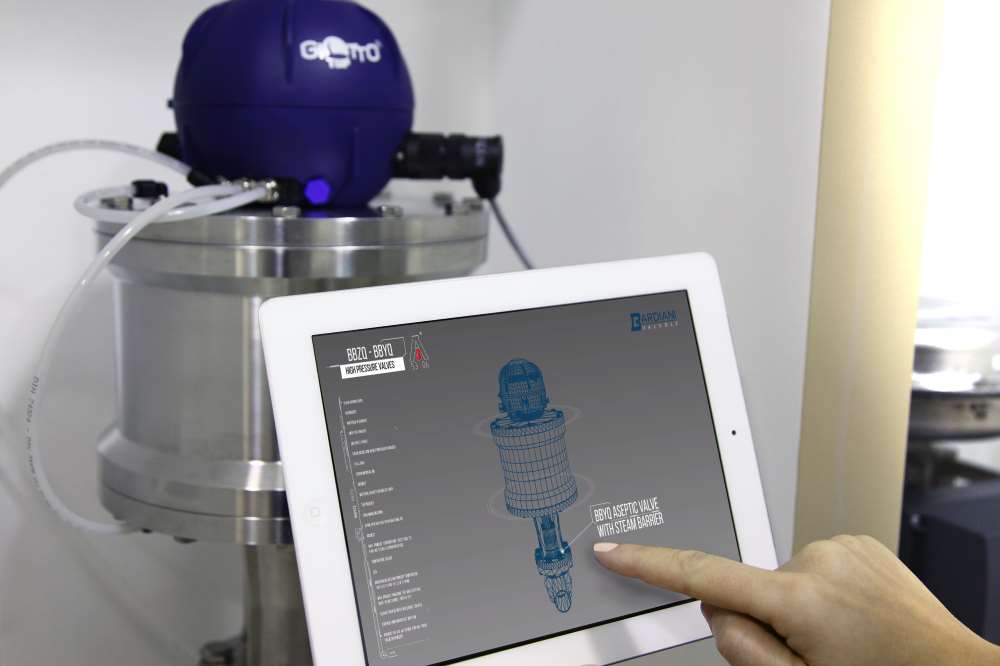
Copyright: Bardiani Valvole Spa
The seal’s design is free of dead space and prevents residue infiltration from process and cleaning media. It is hygienic, easier to clean and compliant with all relevant material specifications for food, beverage and pharmaceutical industry applications. Both materials used have very good thermal resistance and excellent mechanical properties. They also meet the demanding requirements for use in Cleaning in Place and Sterilization in Place (CIP/SIP) processes.
Standard-compliant sealing materials
Fluoroprene® XP is a highly fluorinated material specially developed for extreme applications in the food and pharmaceutical industries. It is suited for all applications involving disinfectants and cleaning agents with extreme concentrations, steam sterilization, high temperatures (up to +200 °C), high concentrations of fats and flavors, and edible oils. The combination of an elastic sealing lip with a PTFE support ring makes the solution extremely pressure resistant. All sealing materials used are compliant with EU (Reg.) 1935/2004, FDA, USP Chapter 87 and 88 and 3-A® Sanitary Standards.
The combination of a new sealing geometry and proven materials has resulted in a customer-specific sealing solution that has been very quickly developed on the basis of customer requirements without the expense of tooling costs. Following extensive testing of the samples on its own test bench, Bardiani Valvole was more than satisfied with the results of the collaboration. Freudenberg was likewise satisfied with the project. “Bardiani Valvole’s technical inquiry for a hygienic high-pressure rod seal was a great challenge at first glance,” said David Brenière, Sales Manager Process Industry at Freudenberg Sealing Technologies. “Nevertheless, we were able to come up with an outstanding solution very quickly, not only on paper, but also in the form of samples produced using turning technology for short-term validation of the new seals.”
Thanks to very productive collaboration, a unique sealing solution was developed and produced, insuring that the high pressure valve from Bardiani Valvole is the first certified to meet 3-A® Sanitary Standards.
Ulrike Reich
Head of Media Relations & Internal Communications
Telephone: + 49 (0) 6201 960 5713
ulrike.reich@fst.com chevron_rightNews Service
You can subscribe to the Freudenberg Sealing Technologies news alert service, bringing you the news as soon as they are published. You can always unsubscribe from this service.
Subscribe now! chevron_rightMore news on the subject Technology & Innovation
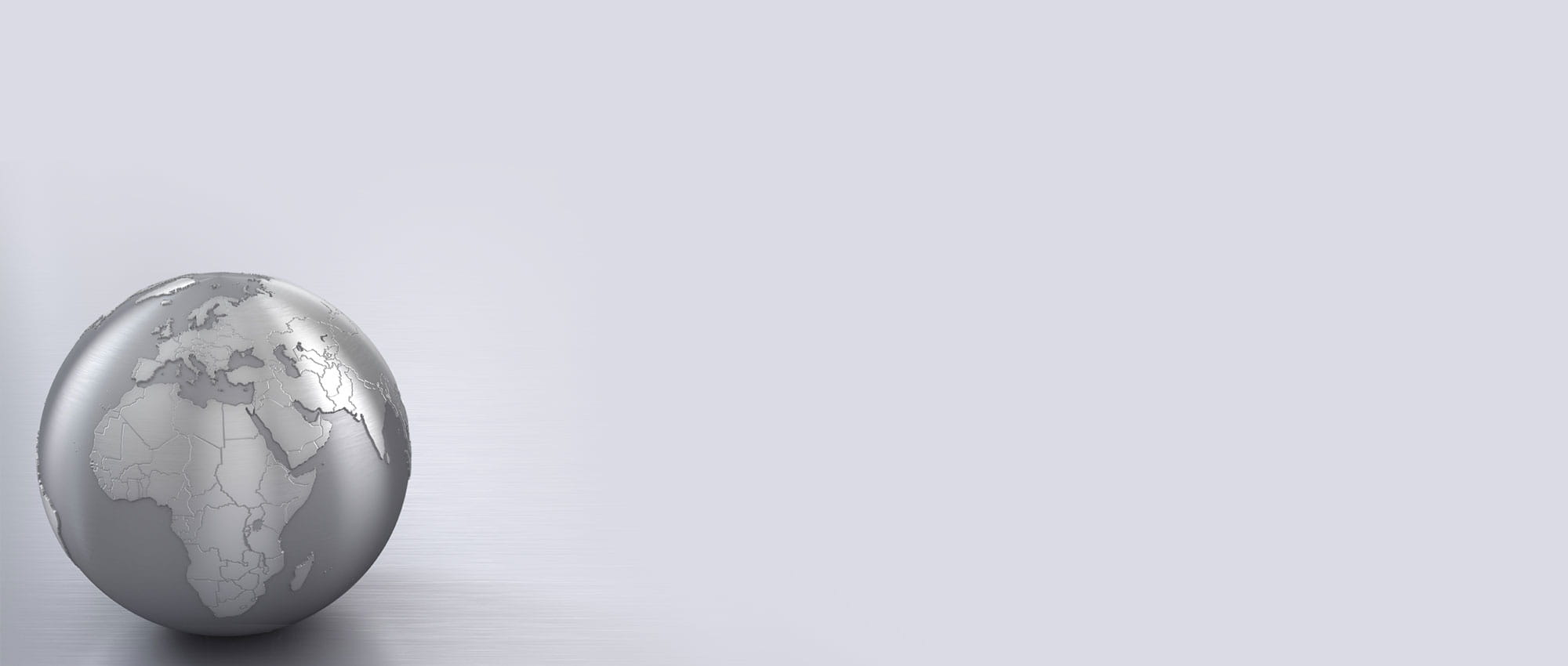
First Hand News
Best of all, keep up with the latest developments
with the Freudenberg Sealing Technologies newsletter.