Obtain news and background information about sealing technology, get in touch with innovative products – subscribe to the free e-mail newsletter.
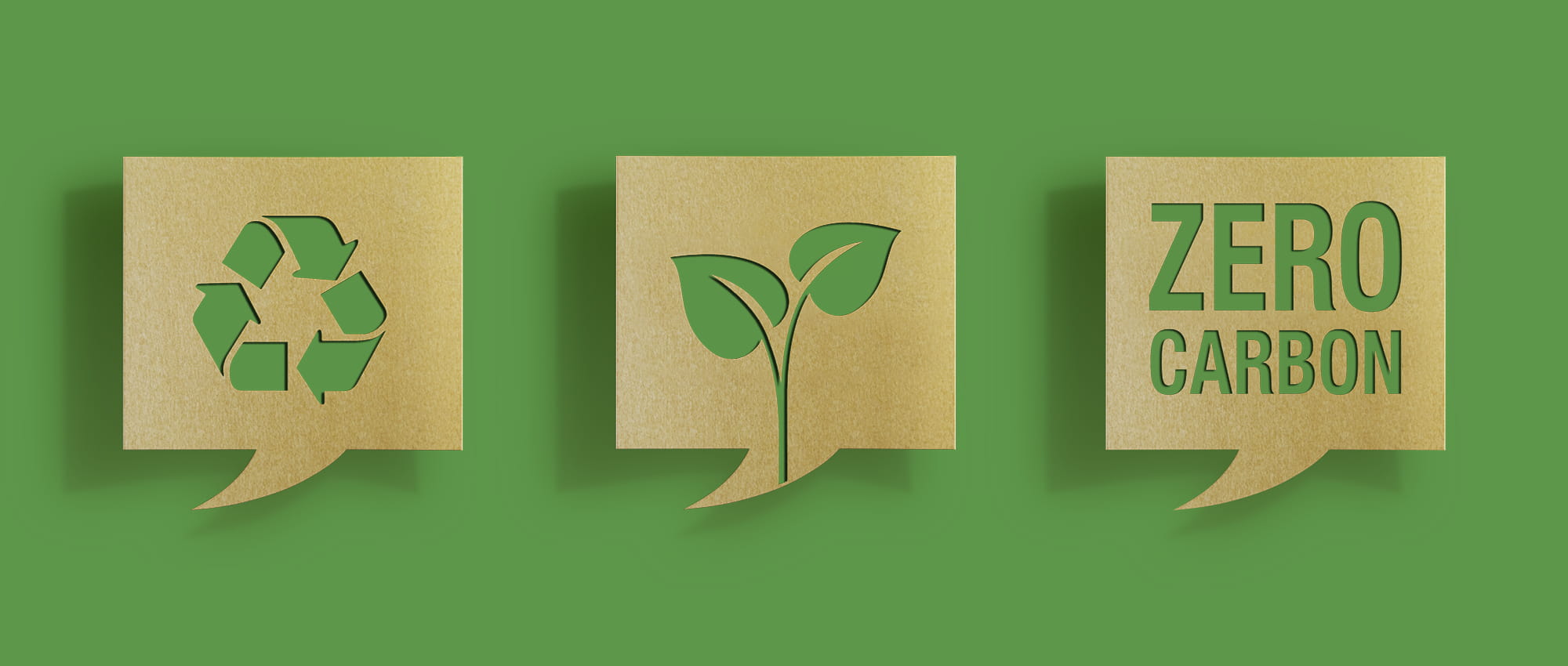
09.08.2022 | Story
Making Carbon
The world cannot do without technical plastics. But if the extraction of fossil materials comes to an end, new sources of carbon will be needed. Successes have been already achieved in the lab, but new industrial options are still in the works.
Consider a world without petroleum and natural gas. It would do the climate some good, but would also mean that we would have to obtain carbon, the basis of all organic compounds, in other ways. Or the world would have to completely do without the element. But substitution with another material is often impossible in the case of technical plastics, which account for about 10 percent of the global annual plastic production. Some examples are the seals that are used in electric household appliances and wind turbines. They contain materials that address unique environmental challenges and thus promote longer product life cycles. Plastic components also significantly reduce the weight of today’s vehicles – and thus their energy consumption.
Recycled
So what would you do if natural gas and oil are no longer available as sources of carbon at some point? “In theory, there are three alternative approaches,” said Dr. Ruth Bieringer, lead materials researcher at Freudenberg Sealing Technologies. “One involves the use of recyclates for the production of new plastics.” Recyclates are used materials that have been cleaned and crushed. “Carbon dioxide can also be obtained from biomass or carbon dioxide,” she said. Methods of carbon recycling are the furthest along – in the recycling of PET (polyethylene terephthalate), for example. Fibers for running shoes are salvaged from discarded plastic bottles. Production scrap from certain thermoplastics can be fed back into the production process. Freudenberg already does this, for example, with polyether ketone (PEEK). But in many cases, classic recycling – collecting, crushing, melting down – faces serious limitations, if only because plastics are not fully sorted when collected. In addition, long carbon molecules become shorter during their use, when exposed to ultraviolet radiation or during processing, for instance. In the case of elastomers, the carbon chains are interconnected with molecular bridges – a process that is not reversible. “We would have to use chemical reduction and recycle individual components, not the complete carbon compounds,” Bieringer said. In-depth research is now underway on what is called chemical recycling. The solution would be a crazy professor-style automated system. The old material would go in on top and separate molecular building blocks would come out at the bottom. But that would take some time to develop.
Grown
Biogenic plastics based on plant matter – and not on foodstuffs – could offer a sustainable way to provide a supply of carbon. Here, the problem is not the available volume: About 400 million tons of plastics are currently produced per year, while the global renewable quantity of biomass is more than a thousand times greater. Furthermore, the percentage of water is not included in the calculation. For example, wood is 20 to 30 percent lignin, a substance left as a residue when paper is produced. “Biochemical processes could help us produce high-quality basic materials,” Bieringer said, highlighting a field that is also heavily researched. The situation is similar with the cultivation of algae. It not only can be directly used as biomass. Organic compounds can even be excreted from it by modifying its metabolism.
Separated
A third way is the extraction of carbon dioxide using technical processes or from the air. In cement production, for example, one carbon dioxide molecule is released for each lime molecule over the course of a chemical reaction. The disadvantage: Both the separation process and the unlocking of the very stable CO2 molecule are energy-intensive. New catalytic materials, also a subject of research, could reduce the energy requirements and thus simplify the recycling of the greenhouse gas.
It is still not clear which option will make it possible to create plastics without fossil materials, according to Bieringer. “A lot can be done in the lab, but there are hardly any solutions that industry can use.” “Developing them is a challenge for the chemical industry,” she added. But she offers this assurance: “As users, we are ready to work with our suppliers and customers to test new approaches.
More news on the subject Sustainability
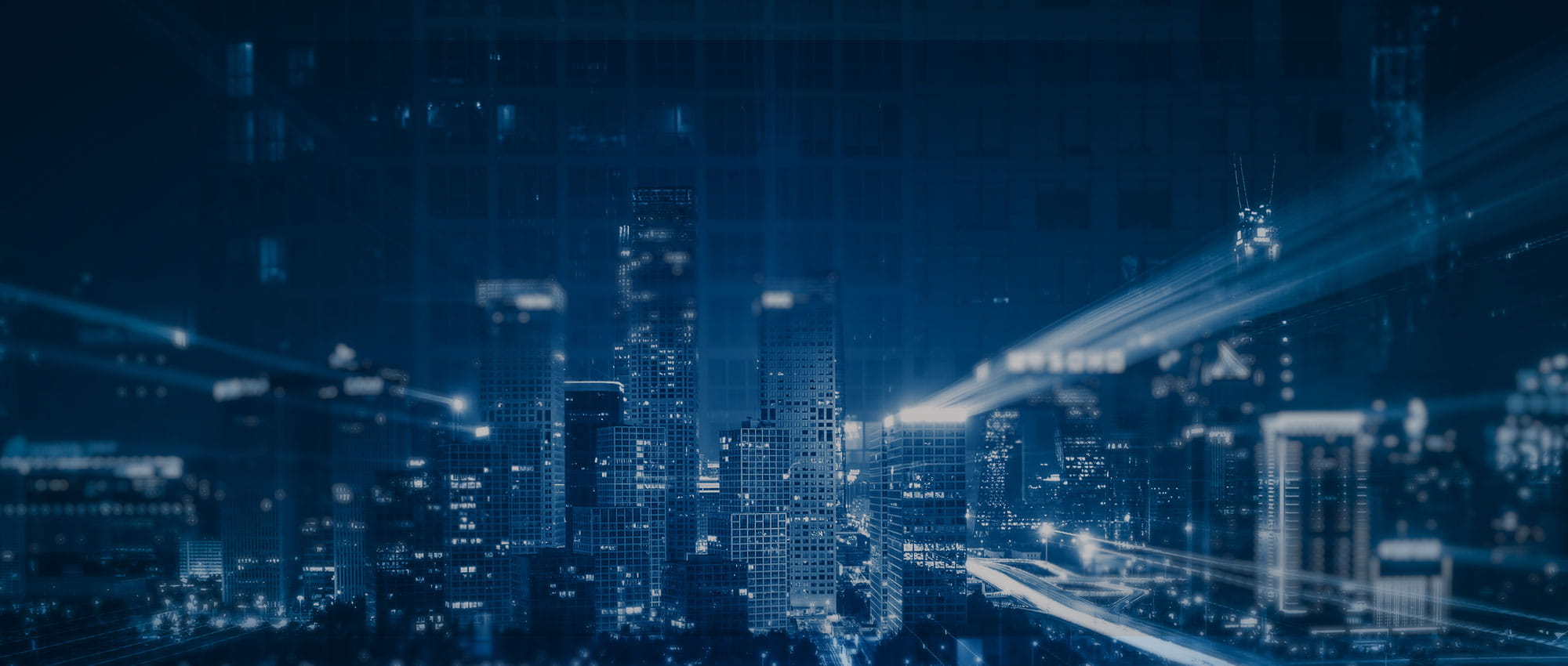
Join Us!
Experience Freudenberg Sealing Technologies, its products and service offerings in text and videos, network with colleagues and stakeholders, and make valuable business contacts.
Connect on LinkedIn! open_in_new