Obtain news and background information about sealing technology, get in touch with innovative products – subscribe to the free e-mail newsletter.
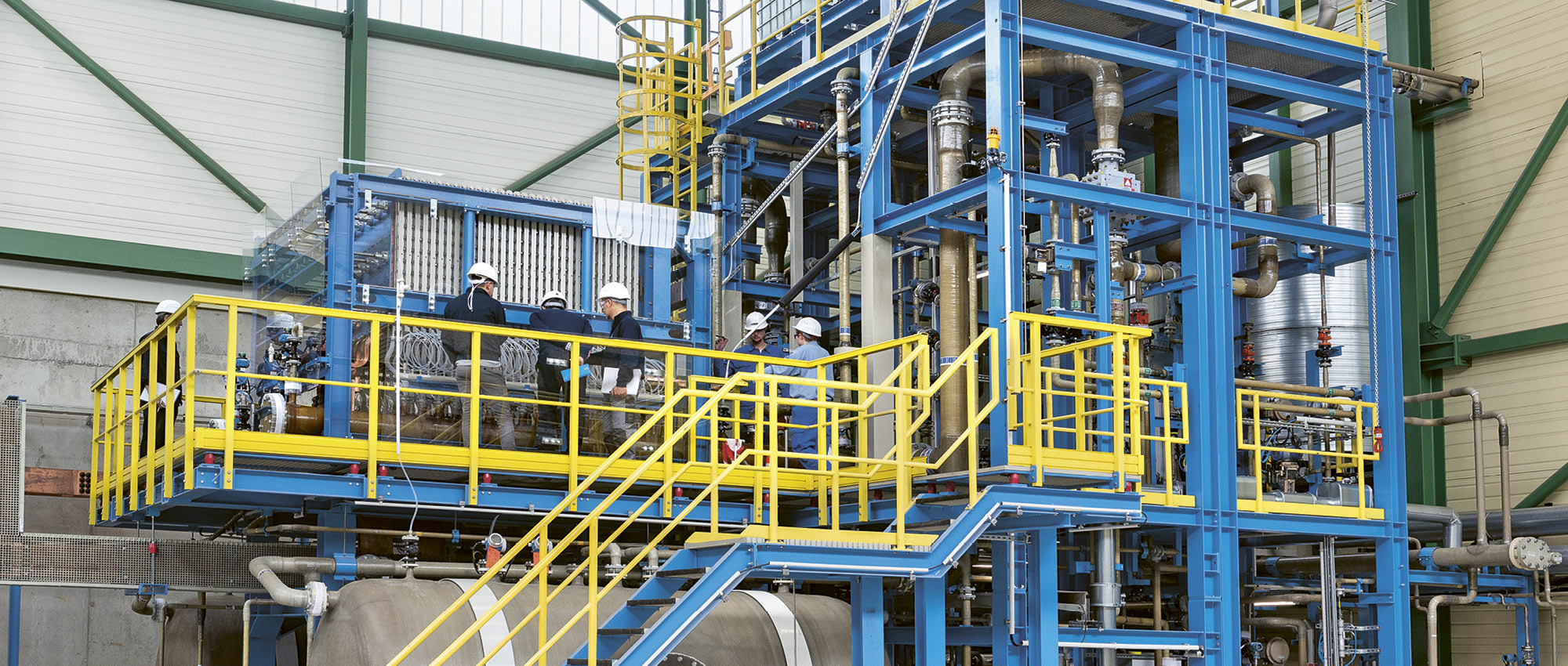
05.10.2022 | Story
From Climate Villain to Useful Material
Steel-making in blast furnaces has a major impact on the climate – just as the production of base materials for the chemical industry does. If you tie processes together, you can reduce emissions significantly. A tour of the Carbon2Chem Technical Center run by thyssenkrupp.
The taxi driver gets lost twice. The thyssenkrupp steel plant in Duisburg is the size of a medium-size city. Its Technical Center, on the other hand, is a small pilot facility. That spurs Dr. Markus Oles to ever-greater ambition. He is in charge of the conglomerate’s innovation strategy and wants to make the steel industry more climate-friendly with the help of the “Carbon2Chem” project. But that’s not easy. It turns out that coke is not just a source of energy in steel-making – it also removes oxygen from iron ore. There’s no steel without coke. The equation is just that simple when the conversation turns to blast furnaces. This has consequences: Blast furnaces emit carbon dioxide as well as other smelter gases, such as carbon monoxide, nitrogen and hydrogen. Certainly, the smelter gases can still be used as a source of energy in a downstream gas power plant, but the process sends the carbon portion of the gases into the air as CO2, contributing to the greenhouse effect. Each year, the steel industry in Germany alone emits about 37 million tons of the climate destroyer.
Carbon2Chem is a joint project drawing on the expertise of several Fraunhofer Institutes as well as the Max Planck Society, in addition to thyssenkrupp and other industrial partners. It is based on a simple idea. “We no longer consider smelter gases to be exhaust gases. Instead, we want to use them as a chemical raw material,” Oles said. In the future, fuels, fertilizers and plastics are expected to be based on these materials. At the Duisburg Technical Center, which has received more than 40 million euros in investment, chemists and engineers are jointly investigating whether the process, which has already been tested in the lab, also works under real-life conditions.
Oles first heads into a green building where hydrogen is produced. The gas is needed in great quantities for the subsequent steps – the proportion of hydrogen in smelting gases is insufficient for the process. To this point, chemical companies have generally broken down natural gas to produce hydrogen. “That didn’t make sense to us since it generated even more carbon dioxide,” Oles explains. So hydrolysis, which only uses water as a raw material, is used in his facility. Using electricity from renewable sources, the water is broken down into hydrogen and oxygen. It is a familiar process, but the trick is to operate this kind of installation with high efficiency when electric current from volatile renewable sources is used. That is precisely what researchers are investigating at the installation in the Technical Center right now – the electric current load changes every 15 minutes. The equipment has been running like this since April 2018, with high-efficiency and practically without demonstrable cell aging.
So far, we haven’t found elements in smelter gas that we were unable to eliminate with our process.
Dr. Markus Oles, Head of innovation strategy at ThyssenKrupp
A small-scale chemical plant is adjacent to the building. The smelting gas is fed into it directly from a nearby blast furnace. A total of 314 standard cubic yards of the gas are prepared per hour. First, it is essential to remove water and sulfur from the gas. The latter would otherwise destroy the equipment’s catalytic converters very quickly. With high resolution measurement technology, the gases are investigated for additional trace elements. “Until now, we have found no ingredient of smelting gas that we could not eliminate in this way,” Oles said. The separation of the gases follows the cleaning process. The goal is for carbon monoxide, carbon dioxide, nitrogen and hydrogen to be present in a precisely defined ratio, creating what is called “synthesis gas.” This gas is used to produce the precursors that are the basis for plastics, fuels and fertilizers: ammonia, methanol and high-quality alcohols. Tests on ways to separate hydrogen are underway with Linde, a thyssenkrupp partner. The hydrogen can then be fed into the process separately. The process is not only generating interest among steel manufacturers. Other industrial processes that release contaminated hydrogen – which is a much sought-after raw material in its pure form – could be improved as well.
Process technicians control the entire facility using a central master display. All processes are continually observed on monitors – even the details relating to individual cells in the electrolysis process. Part of the research project is creating control software that functions optimally with different compositions of the smelting gas and varying load profiles. It is hoped that automation technology now being developed will be used in a cross-industry network throughout the world
After a two-year preparatory phase, the Carbon2Chem Technology Center went into operation in the spring of 2018. By September of that year, it had already succeeded in producing its first synthetic methanol. Meanwhile, the facility, which is merely container-sized, is being retrofitted for the production of high-quality alcohols. Ammonia was first produced in December 2018. “Frankly, it surprised us how stable the processes run,” Oles said. The research project will continue until 2020. At its end, the participants not only expect as many scientific articles as possible to be published – but also an economical facility concept that can quickly be deployed worldwide. To put it another way: If the base materials from the Carbon2Chem are going to compete with petroleum and natural gas products, they must be cost-effective. The results so far show that the best possible sustainability and economy can be achieved when steel manufacturers and the chemical industry work together.
More news on the subject Sustainability
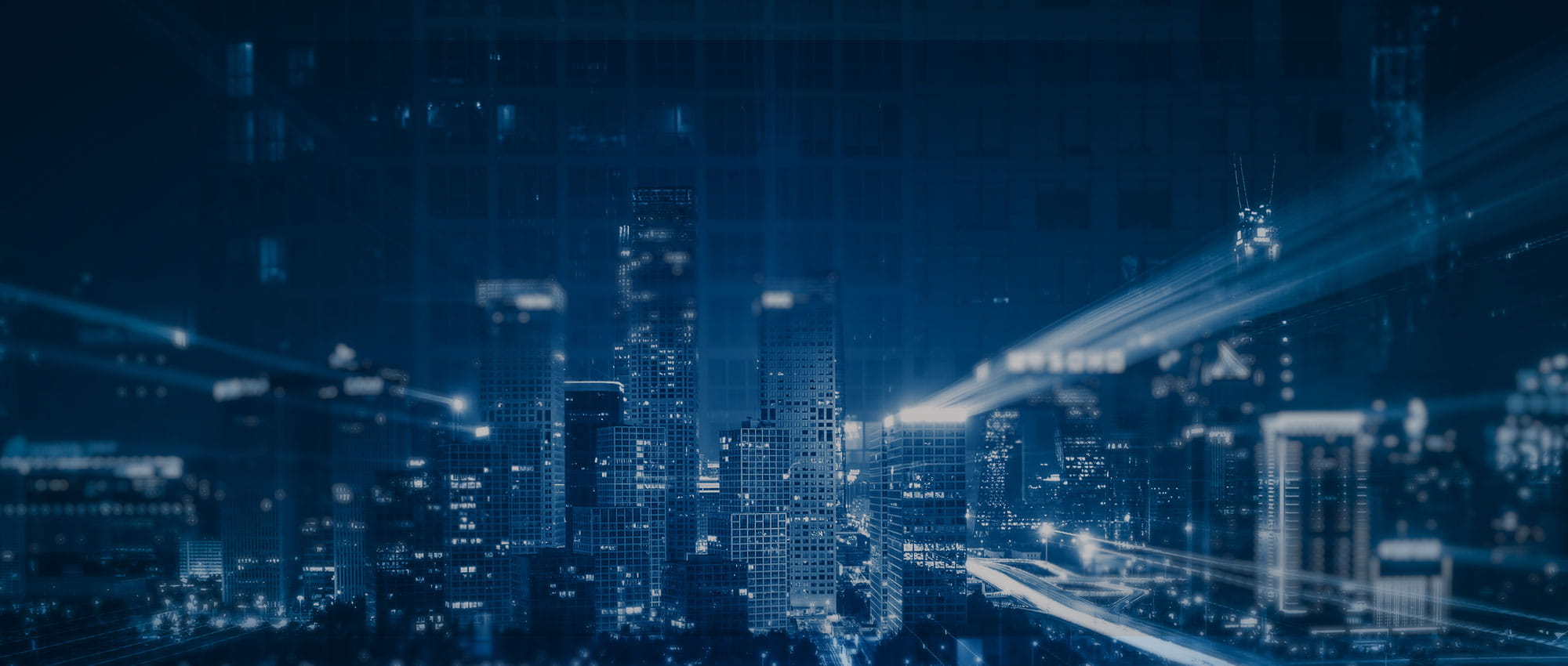
Join Us!
Experience Freudenberg Sealing Technologies, its products and service offerings in text and videos, network with colleagues and stakeholders, and make valuable business contacts.
Connect on LinkedIn! open_in_new