Obtain news and background information about sealing technology, get in touch with innovative products – subscribe to the free e-mail newsletter.
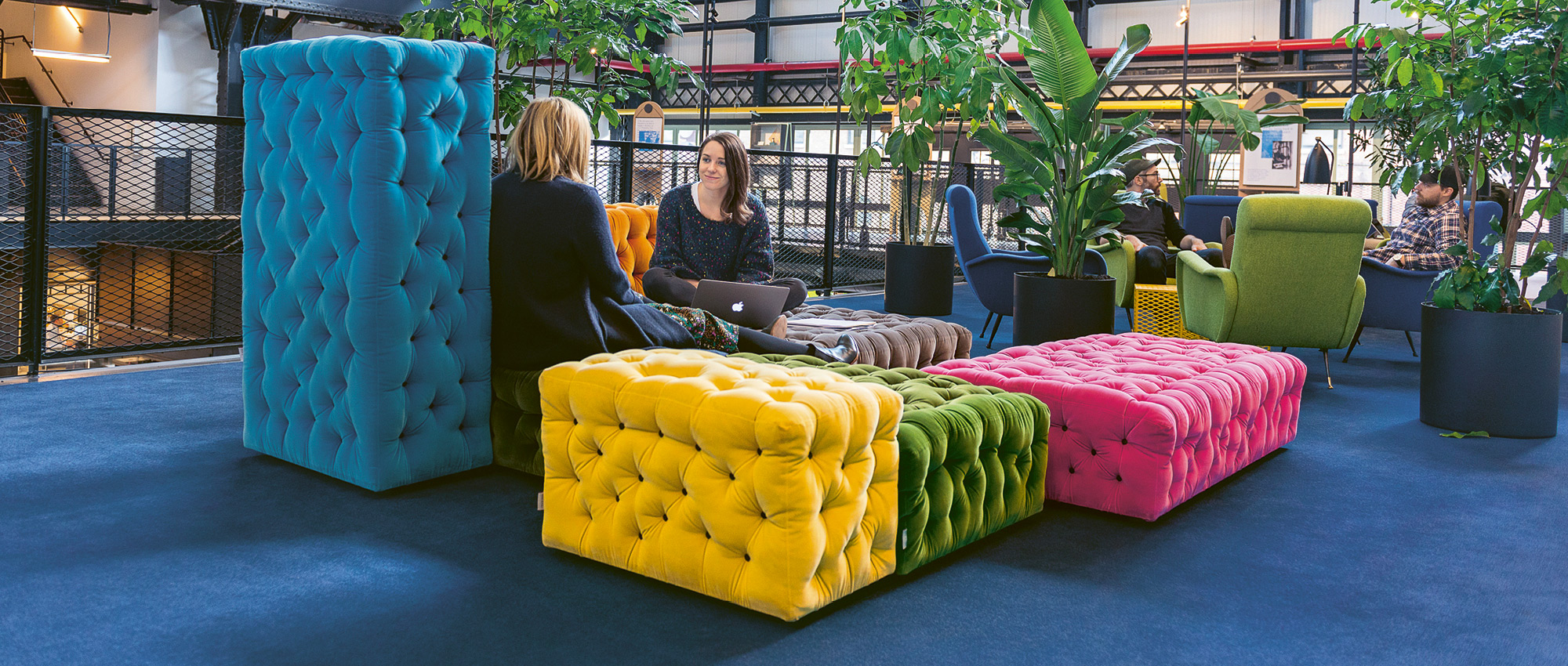
25.06.2019 | Story
Back to the Future
America is still considered the country where a pioneering spirit has especially taken root. Over the past two years, a technology center in Brooklyn has given startups the space and digital support they need to help shape the world of tomorrow.
The pictures of the visionaries of space flight and rocket technology catch the eye: Wernher von Braun, Richard Branson and, of course, Elon Musk. A cylinder made of whitish transparent nylon that is tapered in the shape of a cone stands on the floor of the large loft – the first model of a rocket engine totally constructed with a 3D printer. In eight years, this type of engine is supposed to be able to shoot mini-satellites into space inexpensively. That’s the vision of Max Haot, founder of a company called Launcher. “Satellites are being shrunk from the size of buses to the size of a loaf of bread – this requires entirely different carrier rockets,” said said 41-year-old Haot. They could make it possible to launch a network of mini-satellites into orbit and provide Internet services worldwide. Launcher is one example of a large number of startups that have found the home they need at New Lab in New York. New Lab offers young companies a creative environment where they can use and share innovative production technologies, hands-on-advice and a community of like-minded thinkers. Their home is the Brooklyn Navy Yard, a decommissioned shipyard of the U.S. Navy. Warships were built here during the Second World War. Now its huge manufacturing spaces are a playground for startups.
Huge Creative Center with Digitalized Production
New Lab spent nearly $60 million on renovations for the industrial building two years ago. It is a partnership between private investors, New York City and the state of New York. “We wanted to revive the location of state-of-the-art manufacturing of the past century in a fitting way,” New Lab founder Scott Cohen said. He and cofounder David Belt visited top universities such as MIT and Stanford to assess the status quo of the most advanced production technologies today. Digital processes play a main role here. New Lab is more than just a huge creative center for startups in a cool location: “We are in the business of supporting entrepreneurs, growing companies,” Cohen said. It gives its members access to a mix of equipment – 3D printers, laser cutters and CNC milling machines – that can produce blanks based on digital templates. Leading companies in additive and subtractive production processes, such as the German firm EOS, Southwest Industries, and Hass Machinery, have made their most sophisticated equipment available to New Lab. This allows the transformation of new ideas into prototypes quickly and cost-effectively on site. They can be presented and enhanced immediately.
The New Lab
New Lab offers young companies a creative environment where they can use and share innovative production technologies, hands-on-advice and a community of like-minded thinkers. Their home is the Brooklyn Navy Yard, a decommissioned shipyard of the U.S. Navy. Warships were built here during the Second World War. Now its huge manufacturing spaces are a playground for startups. New Lab spent nearly $60 million on renovations for the industrial building two years ago. It is a partnership between private investors, New York City and the state of New York. It gives its members access to a mix of equipment – 3D printers, laser cutters and CNC milling machines – that can produce blanks based on digital templates.
Products that Solve the Problems of the Future
Over the past few decades, the largest share of software innovations has come from the United States. Breakthroughs in hardware are considered more complicated, but they are exactly at the heart in Brooklyn. Since much of its production capacity has been moved to less expensive foreign countries, America has lost some of its manufacturing expertise. But the United States is still a country with a great many mechanical and automotive engineers as well as tinkerers. New Lab offers the founders of hardware companies a nurturing environment. “Here we are involved with tangible products that solve the problems of the future,” Cohen said. “We expect a manufacturing renaissance.” But it will have little to do with the billowing factory smokestacks and the piecework labor of the Industrial Revolution. “The perception of fabrication and how we interact with the physical world is changing,” he said. “In our times, digitalization of manufacturing is central. Mass customization is possible. The trend around Lot-size One that we see in apparel and sport shoes will extend to all kinds of products.”
On a Space Mission: Honeybee engineer Yoni Saltzman develops custom-made products for NASA, such as a device that can collect sediment on other planets.
Rocket Engines from a Printer
Launcher is one of more than 100 companies – which employ more than 600 workers in all – that want to change the world from their base in New Lab. Taken together, these startups have attracted risk capital of more than $250 million. The process of choosing interested companies is highly selective: New Lab only accepts 15 percent of all applicants. New Lab has even taken an equity stake in 14 of them. Launcher founder Haot is inspired by the Soviet Union’s rocket engines, designed in the 1980s, which reached the highest performance ever and are still in use. “Our goal is to bring this proven high-performance technology to the USA and use 3D printing to reduce its cost by a factor of 10.” In these engines, cold liquid jet fuel flows through a complicated geometric system of channels in the metal of the combustion chamber. This cools the engine and keeps it from melting at high temperatures. It is expensive to mill the channels in the metal – but the process is affordable if it is done additively. Haot managed to attract an expert with 35 years of experience from the Ukraine to New York. Together they printed their first small prototype made of plastic. Haot then used New Lab’s contacts with EOS in Germany to print the combustion chamber out of metal. To realize his vision, Haot, a native of Belgium, became an American citizen so he could work on rockets in the United States.
At New Lab, we design faster and more flexibly, because we can create and modify prototypes at little cost.
Yoni Saltzman, 35, Honeybee-Ingenieur
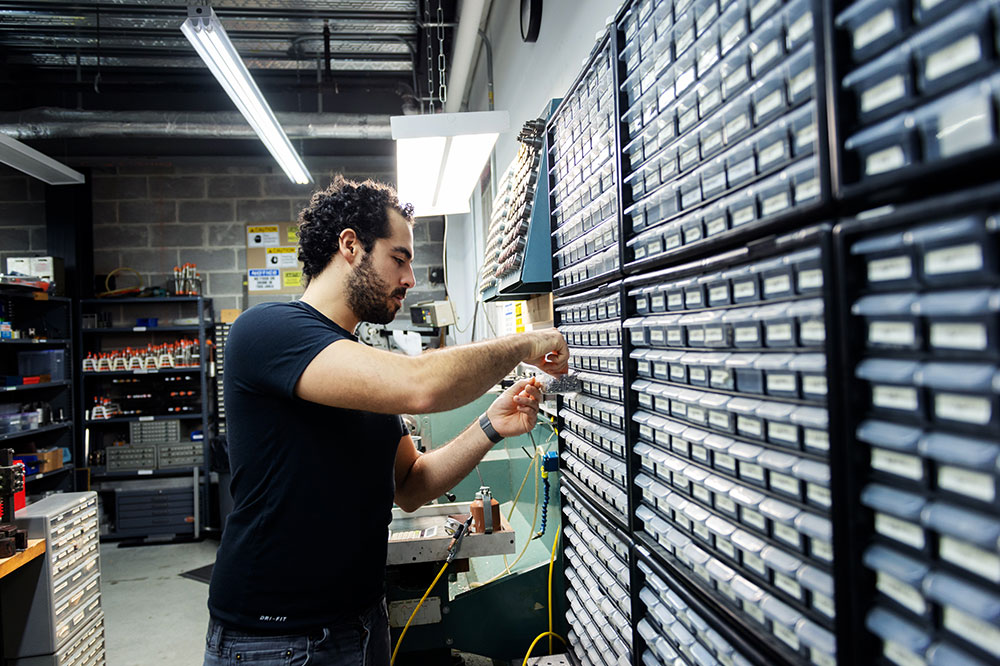
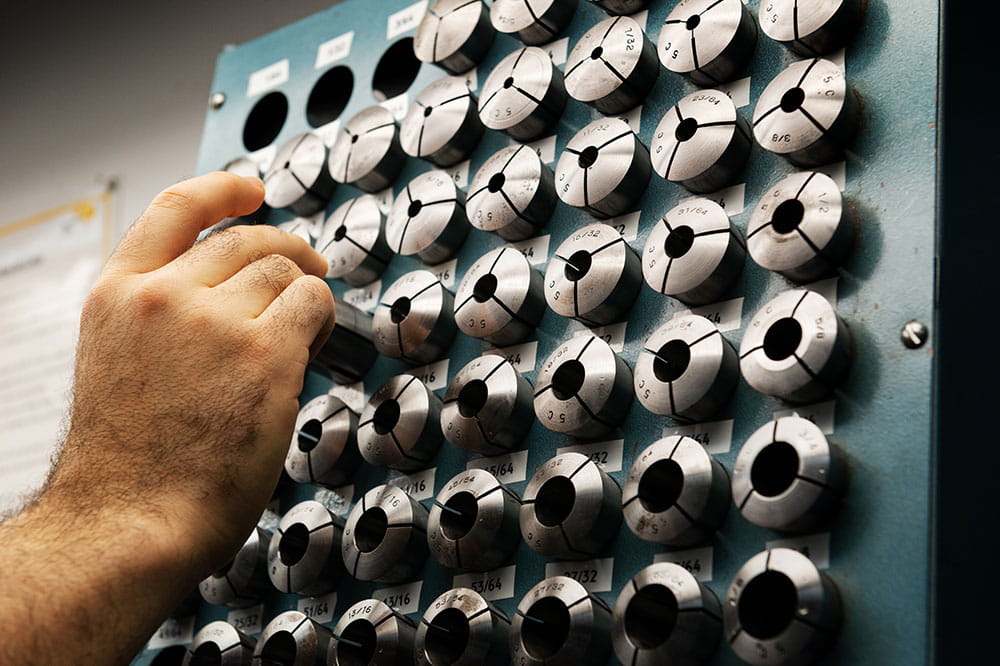
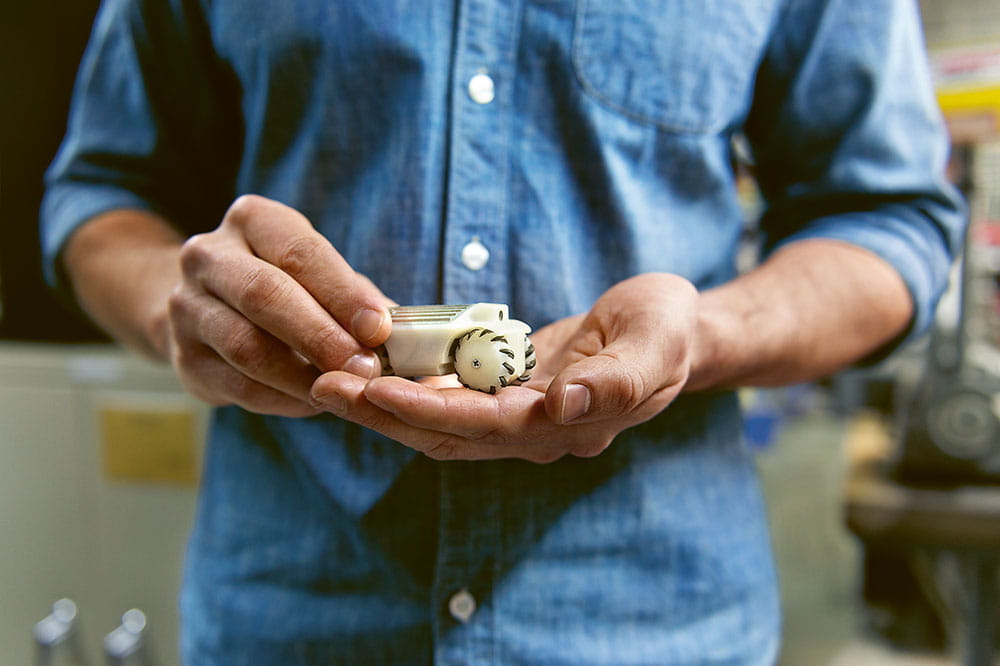
Digitalization Is Expected to Contribute to Space Missions’ Success
During the summer of 2016, Honeybee was one of the very first members of New Lab. The company produces special orders for NASA and other clients. At 35 years old, Honeybee hardly qualifies as a startup, but it works on very sophisticated technical ideas. “New Lab with its advanced prototyping equipment is ideal, because small and medium-sized companies often can’t afford these expensive machines,” said Honeybee engineer Yoni Saltzman, who is now working on a project for NASA’s Langley Research Center on In-Space Assembly. “We are creating a strut assembly system for a truss structure that robots can put together in space,” he said. The idea is to assemble the individual pieces together with a click like a child’s toy. Robots could later use the system to construct buildings in space. Honeybee prints the many prototypes for the click system on 3D printers. Later, in a special workshop, they are supposed to be milled from metals suited for use in outer space. Digitalization is revolutionizing Saltzman’s work. “At New Lab, we design faster and more flexibly, because we can create and modify prototypes at little cost.”
Freedom for Manufacturers and Customers
Taras Kravtchouk, 34, is thrilled as well. He printed the prototypes for his electric motorcycle, Tarform, completely using 3D. He simultaneously experimented with various materials, including biodegradable plastic. Kravtchouk, a Swedish product designer who came to the United States eight years ago, collects old motorcycles. “What Elon Musk showed with Tesla is that electric cars can be beautiful, and that inspired me to create an electrical motorbike. The traditional brands did not show much initiative,” he said. Kravtchouk equipped his motorcycles with sensors that, for instance, warn riders if a car is threatening to cut them off. “Biking is all about the experience of the ride and being in control of the vehicle – autonomous driving would be wrong. We bring more security without compromising the rider’s sense of freedom,” he said. This year, Kravtchouk plans to 3D print various external parts at their own facility close to New Lab. “Additive technologies are already more capable of producing just prototypes,” he said. “Today, we already can utilize additive manufacturing during our low volume production of the first 100 vehicles – and each one can be customized.” Everything is indeed looking up for New Lab and its members.
More news on the subject Robotics
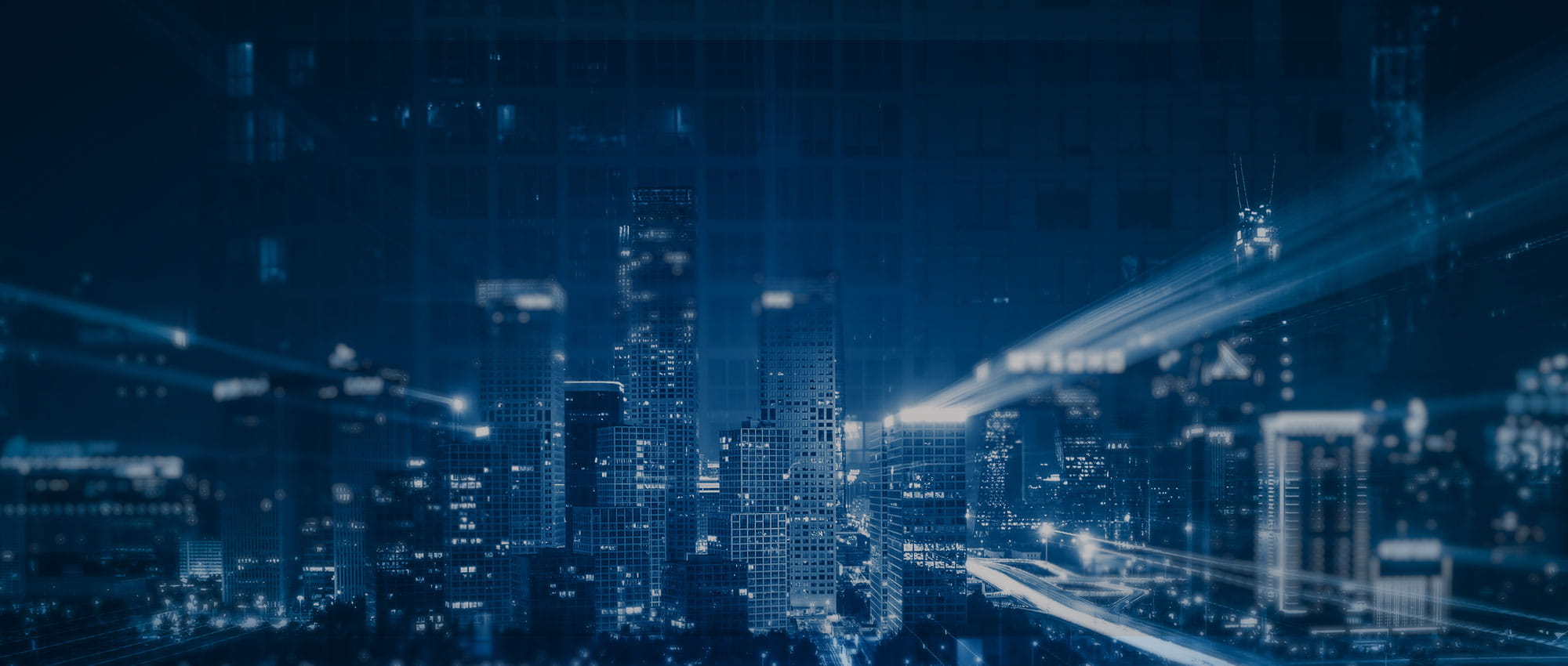
Join Us!
Experience Freudenberg Sealing Technologies, its products and service offerings in text and videos, network with colleagues and stakeholders, and make valuable business contacts.
Connect on LinkedIn! open_in_new