Obtain news and background information about sealing technology, get in touch with innovative products – subscribe to the free e-mail newsletter.
13.10.2020 Press Release
Crossing the Divide
Front wheels with suspension are standard for high-quality mountain bikes. But riders still passionately debate whether the rear axle should also be equipped with suspension. The benefit of the classic hardtail version without suspension is that you can ride it more efficiently. Proponents of the full-suspension version, also called “fully”, argue that it offers more comfort and control, since the tire has more contact with the ground even on rough terrain.
Now the manufacturer Trek from Waterloo, Wisconsin (USA), which specializes in bicycles, has the perfect solution for this conflict. The suspension strut is fully integrated into the frame, which significantly reduces the added weight compared to traditional full suspension bike. The wheel is guided by two seatstays that are rigidly connected to the suspension strut. Riders can set the shock spring rate according to their preference. Seals from Freudenberg Sealing Technologies ensure that the high-tech system continues to be low-maintenance even with heavy use on open terrain keeping out all the dirt, dust and mud that comes with mountain biking.
The art of small things
Two sealing rings keep the oil in the suspension strut during the dynamic operation and also protect the system from dust and spray water penetration. For the sealing engineer Simon Watling at Freudenberg Sealing Technologies, the main challenge lay in the dimensions dictated by the design of the suspension inside the frame: “We only had three millimeters of space available for the seals.” This requirement couldn’t be met with a standard product, so Watling found a new design version in which the geometry of the sealing lips is precisely adapted to the assembly space.
“Another challenge of working with these small components is the production tolerances,” Watling explains. “Relative to the component size, even a deviation of a few tenths of a millimeter is too much.” This is why Freudenberg relies on nitrile rubber as a sealing material for this market segment: It has specific deformation behavior in a temperature range of −30 to 100 °C. Furthermore, the design and material are optimized for low friction. From the rider’s perspective, this is particularly important to eliminate stiction in the system so the shock’s damped compression can operate as intended without impact from the seals. Also, in case the bike has been stationary for a few days and there is less lubricating oil on the contact surfaces, if the friction is low, the rider won’t notice any change in the suspension behavior when starting out.
The new sealing solution was first tested with the simulation programs that Freudenberg engineers normally use in automotive development. Then it was subjected to real testing on test stands and, above all, with mountain bike. Since late 2019, the IsoStrut system has proven reliable on the Trek Supercaliber, an innovative cross-country mountain bike, for end consumers and at the Cross-Country World Cup racing.
Reaching the goal together
“The product designers at Trek Bicycle always want only the best solution,” Watling said about the collaboration. “This is very motivating.” He is already working on a new generation of the seals with the bike manufacturer. They should be even more compact to enable greater suspension travel in the future.
“The market segment of high-quality recreational equipment is becoming increasingly important to us,” said Oswaldo Anaya, Marketing Manager at Freudenberg Sealing Technologies. Products that are mainly sold for price reasons still dominate the market for recreational vehicles. But Anaya is optimistic: “The more the customers’ demands increase, the more important it is for the manufacturers to use quality components.”
Ulrike Reich
Head of Media Relations & Internal Communications
Telephone: + 49 (0) 6201 960 5713
ulrike.reich@fst.comCheryl Eberwein
Director, Corporate Communications
Telephone: +1 734 354 5373
cheryl.eberwein@fnst.comDownload Documents
Download Images
News Service
You can subscribe to the Freudenberg Sealing Technologies news alert service, bringing you the news as soon as they are published. You can always unsubscribe from this service.
Subscribe now!Further Articles With These Taggings
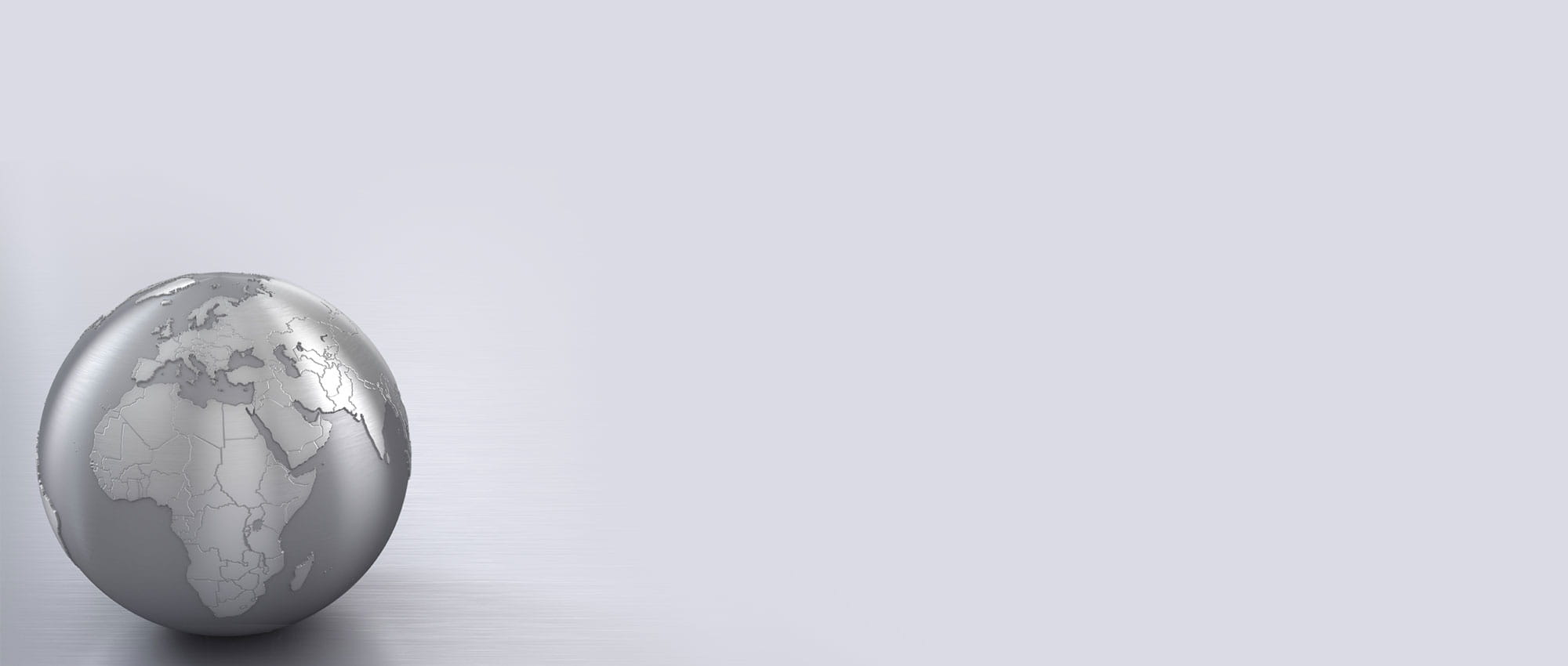
First Hand News
Best of all, keep up with the latest developments
with the Freudenberg Sealing Technologies newsletter.