Neuigkeiten und Hintergründe aus der Dichtungstechnik erfahren, innovative Produkte kennenlernen – im kostenlosen E-Mail-Newsletter von Freudenberg Sealing Technologies.
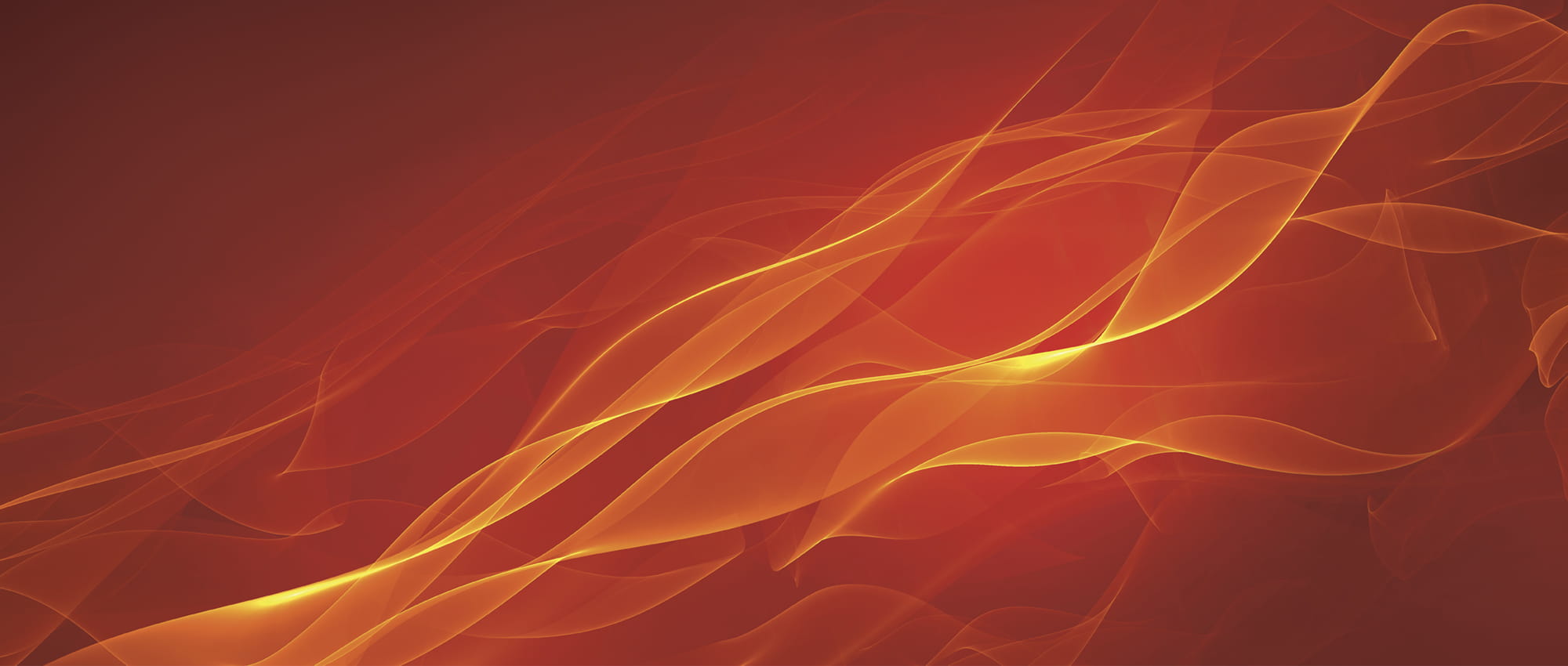
17.01.2023 | Story
Raus aus dem Ofen
Einige Werkstoffe erhalten ihren notwendigen letzten Schliff, indem sie im Ofen unter hohen Temperaturen nachhärten. Das kostet Energie – und müsste vielleicht gar nicht sein. Warum es innovativ sein kann, darauf zu verzichten, erklärt Materialexperte Joe Walker.
Manchmal entsteht Innovation durch Zufall. Im Jahr 2001 sollten Joe Walker, Global Technology Director Materials and Laboratories bei Freudenberg Sealing Technologies, und sein Team eine statische Kunststoffdichtung für einen Kunden entwickeln. Die Konkurrenz setzte auf ein Material, das nachheizen musste – aber sich im Ofen unter der Hitze verformte. „Eine sehr unerwünschte Eigenschaft“, kommentiert Walker. Also experimentierten sie. Und entwickelten erstmals ein Produkt, das auch ohne anschließende Zeit im Ofen auskam. Am Ende stand eine Lösung, die gleichzeitig alle wichtigen Funktionen erfüllt, langlebig ist und nachhaltig obendrein.
Die Welt verlangt von uns, dass wir die Art und Weise, wie wir Dinge tun, verändern. Deshalb müssen wir mit den Kunden über umweltfreundlichere Alternativen sprechen, die gleichzeitig die Herstellungskosten senken.
Nachhärten für saubere Werkstoffe
Hierzu muss man wissen: Einer der üblichen Nachbearbeitungsschritte für einige Werkstoffe aus Kunststoff und Gummi lautet: ab in den Ofen. Denn unter Hitze ändern die Materialien ihre Eigenschaften. Dabei sind die Begriffe nachheizen oder nachhärten etwas ungenau, erklärt Walker, der die Materialentwicklung und Labore für Freudenberg Sealing Technologies in den USA leitet: „Beim Aushärten denken wir meist daran, dass sich Molekülketten verdichten, also ein Material seine mechanischen und physikalischen Eigenschaften verändert.“ Den Zusammenhang gebe es durchaus, es sei aber nicht der einzige Grund für den Gang in den Ofen: Gummi muss beispielsweise schon allein deswegen nachgeheizt werden, um unerwünschte Nebenprodukte loszuwerden. Diese entstehen, wenn die einzelnen Zutaten sich vermischen und chemisch miteinander reagieren. Verbleiben sie aber im Werkstoff, können sie dessen Eigenschaften verändern – oder sogar schädigen. Andere Werkstoffe, die in der Lebensmittel- oder Arzneimittelindustrie zum Einsatz kommen, müssen wiederum in den Ofen, um einen bestimmten Reinheitsgrad zu erreichen. Und auch die Produktivität kann sich bei den hohen Temperaturen verbessern: etwa bei Polymeren, die unter Druck und Hitze geformt und anschließend in einem Ofen fertiggestellt werden. „Solche Materialien ermöglichen kurze Zyklen in den Maschinen“, erklärt Walker. Denn die Formgebungswerkzeuge sind schneller wieder frei, während große Chargen in den Öfen nachhärten.
Francis Joseph Walker: Joe Walker arbeitet seit mehr als 43 Jahren mit Elastomeren und Kunststoffen. Bei Freudenberg Sealing Technologies überwacht er alle Entwicklungen im Bereich moderne Werkstoffe in den USA. Der Experte ist bereits mehrfach für seine Verdienste in der Gummiindustrie ausgezeichnet worden. So ernannten ihn Mitglieder des Rubber Technologists Network zum US-Kautschuk-Technologen des Jahres 2016.
Öfen abschalten und Energie sparen
Trotz all dieser guten Gründe entwickeln Walker und sein Team seit damals gezielt Werkstoffe, die ohne Nachheizen auskommen. „Typischerweise sind das FKM- und EPDM-Materialien“, sagt Walker. Beide Werkstoffe basieren auf Kautschuk und werden für Dichtungen in unterschiedlichen Bereichen eingesetzt – FKM beispielsweise in der Automobil-, Luftfahrt- und Nutzfahrzeugindustrie, EPDM in der Lebensmittel- und Pharmabranche. Warum es sich lohnt, in manchen Fällen nicht nachzuheizen, hat insbesondere mit dem immens hohen Energieverbrauch zu tun, den der Vorgang verursacht: „Ein Zyklus im Ofen einer unserer Simmerring®-Fertigungen verbraucht etwa 41 Kilowattstunden Strom“, führt Walker an. Pro Tag sind drei solcher Zyklen möglich, und das an 250 Tagen im Jahr. Übersetzt man diesen Stromverbrauch in CO2, das dabei entsteht, kommt man auf Emissionsmengen in Millionenhöhe – Emissionsmengen, die ohne Öfen erst gar nicht anfallen müssten. „Wir werden nie in der Lage sein, vollständig auf die Öfen zu verzichten“, schränkt Walker ein: „Denn einige Polymere müssen wir wie gesagt nachheizen, um schädliche Nebenprodukte zu eliminieren und um spezielle Eigenschaften zu erhalten.“ Aber es wäre durchaus höchst lohnenswert, Öfen dort herunterzufahren oder sogar abzuschalten, wo sie nicht zwingend notwendig sind. CO2-Emissionen ließen sich erheblich reduzieren. Obendrein würden weniger Kosten anfallen – für die Energie selbst sowie auch Personalkosten, schließlich müssen die Öfen be- und entladen und gewartet werden. Zykluszeiten würden sich verkürzen.
Erst der Werkstoff, dann die Spezifikation
Warum aber sind Öfen bis heute standardmäßig Teil des Prozesses? „Ein Problem sind die Spezifikationen“, antwortet Walker. Also jene genau festgelegten Eigenschaften, auf die sich Kunden und Freudenberg Sealing Technologies bei der Entwicklung eines Werkstoffs geeinigt haben. Dabei wird meist in umgedrehter Reihenfolge entwickelt: Zunächst wird im Labor gemischt und getestet. Und sobald ein Werkstoff funktioniert, werden rückwirkend die Eigenschaften als Spezifikationen festgehalten: Wie fest ist er, welchen Druckwiderstand besitzt er, welches mechanische Profil weist er auf? Das ist wichtig, um gleichbleibende Qualität zu garantieren. „Manchmal aber müssen wir Materialien nachheizen, um gewisse Spezifikationen zu erfüllen“, sagt Joe Walker: „Und das, obwohl es die Leistung des Werkstoffs nicht erfordert.“ Eben weil es im Vorfeld so festgelegt wurde.
Innovation braucht Dialog
Umso wichtiger also, sich bereits im Vorfeld Gedanken zu machen, ob nachgeheizt werden muss oder nicht – und Spezifikationen entsprechend zu planen. Bei einigen Werkstoffen war das für Walkers Team möglich. So sind zum jetzigen Zeitpunkt bereits diverse Werkstofftypen von Freudenberg Sealing Technologies global im Einsatz, die nicht nachgeheizt werden. Schwieriger gestaltet es sich bei Werkstoffen, die bei den Kunden bereits etabliert sind. Denn um neue Werkstoffe einzuführen, braucht man sowohl auf Kunden- als auch auf Herstellerseite Mitarbeitende, die diese bewerten, testen und Prozesse anpassen. Das wiederum nimmt Zeit und Ressourcen in Anspruch. Unternehmen stehen aber aktuell bereits vor anderen schwerwiegenden Herausforderungen: etwa davor, dass Rohstoffe knapp werden, Lieferketten unterbrochen werden und sich infolgedessen viele Abläufe ändern. Trotzdem lohne es sich, in den Dialog zu treten, meint Walker: „Die Welt verlangt von uns, dass wir die Art und Weise, wie wir Dinge tun, verändern. Deshalb müssen wir mit den Kunden über umweltfreundlichere Alternativen sprechen, die gleichzeitig die Herstellungskosten senken.“
Dieser Beitrag stammt aus unserem Unternehmensmagazin „ESSENTIAL“, in dem wir kontinuierlich über Trends und Schwerpunktthemen aus unseren Zielindustrien und -märkten berichten.
Weitere News zum Thema Technology & Innovation
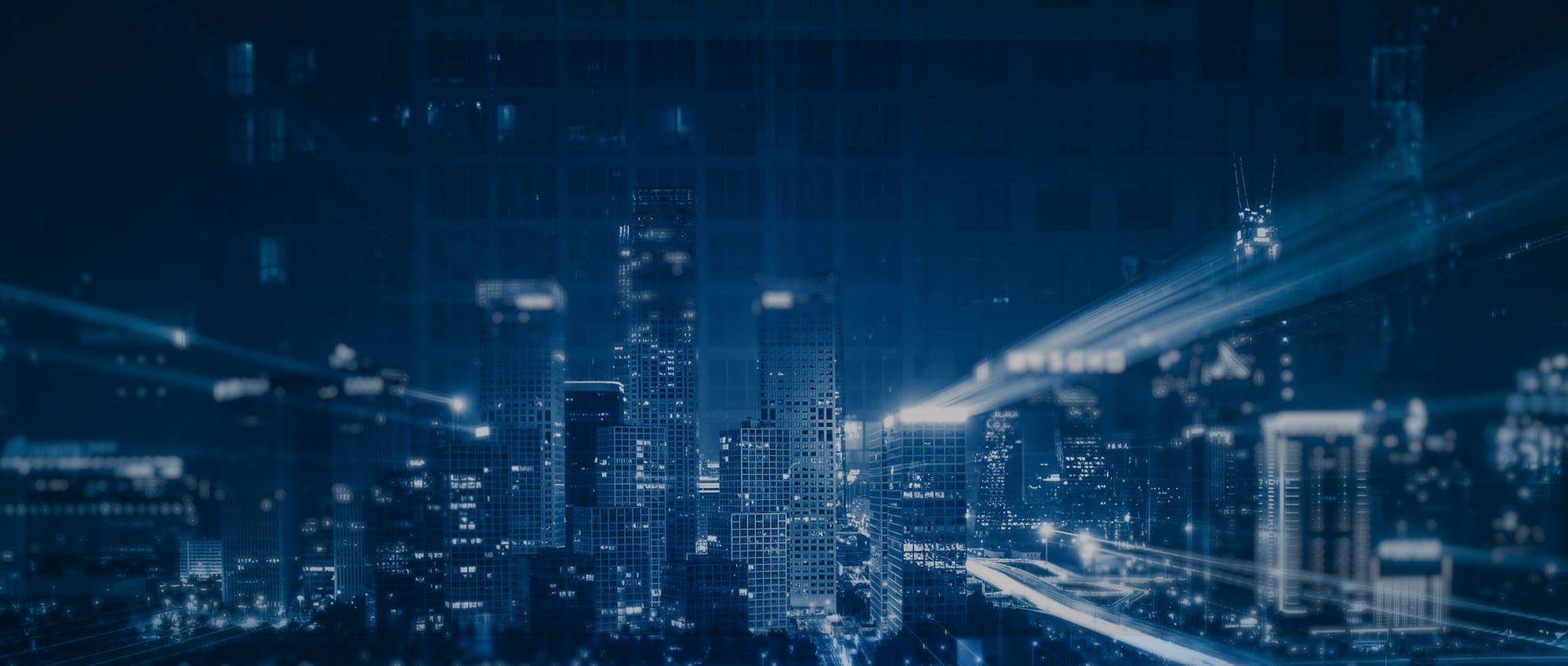
Join Us!
Freudenberg Sealing Technologies, seine Produkte und Serviceangebote in Wort und bewegten Bildern erleben, sich mit Mitarbeitenden und Stakeholdern vernetzen und dabei wertvolle geschäftliche Kontakte knüpfen.
Auf LinkedIn vernetzen! open_in_new