Neuigkeiten und Hintergründe aus der Dichtungstechnik erfahren, innovative Produkte kennenlernen – im kostenlosen E-Mail-Newsletter von Freudenberg Sealing Technologies.
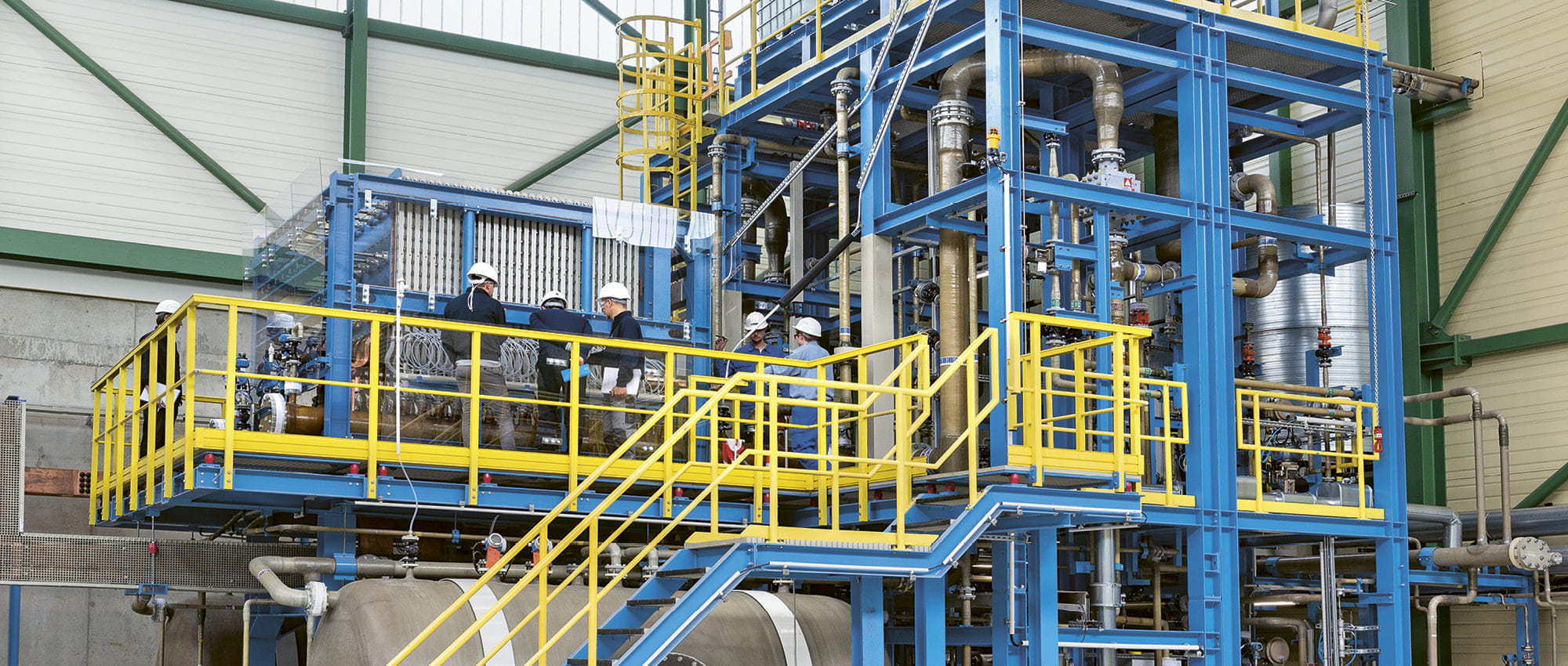
Vom Klimakiller zum Wertstoff
Die Stahlproduktion im Hochofen belastet das Klima genauso wie die Herstellung von Grundstoffen für die chemische Industrie. Koppelt man die Prozesse, können die Emissionen deutlich sinken. Ein Rundgang durch das von ThyssenKrupp verantwortete Carbon2Chem-Technikum.
Zweimal verfährt sich der Taxifahrer. Das Duisburger Stahlwerk von ThyssenKrupp hat die Ausmaße einer mittleren Stadt, das Technikum hingegen ist eine kleine Pilotanlage. Umso größer sind die Ambitionen, die Dr. Markus Oles hat. Er verantwortet die Innovationsstrategie des Mischkonzerns und will mit dem Projekt „Carbon2Chem“ die Stahlindustrie klimafreundlicher machen. Einfach ist das nicht, denn im Hochofen eines Stahlwerks wird Koks nicht nur als Energieträger genutzt, sondern auch, um den im Eisenerz enthaltenen Sauerstoff zu entfernen. Ohne Kohle kein Stahl, so einfach ist die Gleichung, zumindest bei mehr als 50 Stahlwerken weltweit, die mit dem Hochofenprozess arbeiten. Das hat Folgen: Der Hochofen emittiert Kohlenstoffdioxid sowie weitere Hüttengase, vor allem Kohlenmonoxid, Stickstoff und Wasserstoff. Zwar lässt sich das Hüttengas in einem nachgeschalteten Gaskraftwerk noch energetisch nutzen, doch dabei gelangt der enthaltene Kohlenstoff als CO2 in die Luft und trägt zum Treibhausgaseffekt bei. Rund 37 Millionen Tonnen des Klimakillers emittiert die Stahlindustrie allein in Deutschland jährlich.
Carbon2Chem, ein Verbundprojekt, in dem sich neben ThyssenKrupp sowohl weitere Industriepartner als auch mehrere Fraunhofer-Institute sowie die Max-Planck-Gesellschaft engagieren, basiert auf einer simplen Idee. „Wir betrachten die Hüttengase nicht mehr als Abfall, sondern wollen sie als chemischen Rohstoff nutzen“, erläutert Oles. Auf Basis dieser Rohstoffe sollen künftig Kraftstoffe, Düngemittel oder Kunststoffe entstehen. Im Duisburger Technikum, in das mehr als 40 Millionen Euro investiert wurden, untersuchen Chemiker und Ingenieure gemeinsam, ob das zuvor im Labor bereits erprobte Verfahren auch unter realen Bedingungen funktioniert.
Zunächst führt Oles in ein blaues Gebäude, in dem Wasserstoff produziert wird. Der wird für die nachfolgenden Schritte in großen Mengen benötigt – der Anteil im Hüttengas reicht dafür nicht aus. Bislang spalten Chemieunternehmen in der Regel Erdgas auf, um Wasserstoff herzustellen. „Das macht für uns keinen Sinn, denn dabei entsteht noch mehr Kohlendioxid“, so Oles. In seiner Anlage kommt daher ein Elektrolyse-Verfahren zum Einsatz, das als Grundstoff nur destilliertes Wasser benötigt, welches mithilfe von umweltschonend erzeugtem Strom in Wasserstoff gewandelt wird. Das Verfahren ist bekannt, aber die Kunst besteht darin, eine solche Anlage auch dann mit hohem Wirkungsgrad zu betreiben, wenn Strom aus volatilen erneuerbaren Quellen genutzt wird. Genau das wird an der Anlage im Technikum, äußerlich einer riesigen Brennstoffzelle ähnelnd, untersucht – alle 15 Minuten ändert sich die Stromlast. Die einzelnen Zellen, in denen die Elektrolyse stattfindet, unterscheiden sich nur in Details, die jedoch für einen großindustriellen Einsatz wichtig sind: Mal variiert die Beschichtung der Elektroden, mal der Aufbau der Membran, an der die Sauerstoffreduktion stattfindet. Mittlerweile läuft die Anlage stabil, der mittlere Wirkungsgrad liegt im Schnitt bei 82 Prozent.
Bislang haben wir im Hüttengas keine Elemente gefunden, die wir auf diesem Weg nicht beseitigen könnten.
Dr. Markus Oles, Leiter Innovationsstrategie ThyssenKrupp
Direkt neben dem Gebäude steht ein Chemiewerk im Kleinformat. Über ein Rohr wird das Hüttengas direkt aus einem benachbarten Hochofen zugeführt. Insgesamt 240 Normkubikmeter des Gases werden hier pro Stunde aufbereitet. Zunächst gilt es, Wasser und Schwefel zu entfernen, Letzterer würde die Katalysatoren in der Anlage sonst schnell zerstören. Mit hochauflösender Messtechnik werden die Gase auf weitere Spurenelemente untersucht, die ein Aktivkohlefilter auffängt. „Bislang haben wir im Hüttengas keine Elemente gefunden, die wir auf diesem Weg nicht beseitigen könnten“, fasst Oles zusammen. Auf die Reinigung folgt die Trennung der Gase. Ziel ist es, dass am Ende Kohlenmonoxid und Wasserstoff in einem genau definierten Verhältnis zueinander vorliegen, das als „Synthesegas“ bezeichnet wird. Dieses Synthesegas wird anschließend entweder methanisiert – also zu synthetischem Erdgas verarbeitet – oder dient als Zwischenprodukt für die Herstellung jener Grundstoffe, auf denen Kunst- und Kraftstoffe sowie Dünger basieren: Ammoniak, Methanol und hochwertige Alkohole. Getestet wird mit dem Industriepartner Linde auch eine Abtrennung des Wasserstoffs, der dann separat in den Prozess eingespeist werden kann. Das Verfahren ist nicht nur für die Stahlherstellung interessant, sondern auch für andere industrielle Prozesse, die verunreinigten Wasserstoff – in Reinform ein begehrter Rohstoff – freisetzen.
Über eine zentrale Leitwarte steuern Verfahrenstechniker die gesamte Anlage. Auf den Monitoren werden alle Prozesse laufend überwacht – bis hinein in die Details einzelner Zellen in der Elektrolyse. Teil des Forschungsprojekts ist auch der Aufbau einer Steuerungssoftware, die mit unterschiedlichen Zusammensetzungen des Hüttengases und verschiedenen elektrischen Lastprofilen optimal funktioniert. Eines Tages, so die Hoffnung, soll die so entstehende Automatisierungstechnik in jedem Stahlwerk auf der Welt eingesetzt werden.
In Betrieb genommen wurde das Carbon2Chem-Technikum nach zweijähriger Vorbereitungsphase im Herbst 2018. Schon zum Start ist es gelungen, das erste synthetische Methanol zu produzieren. Mittlerweile wird die nur containergroße Anlage schon wieder umgerüstet auf die Herstellung höherwertiger Alkohole. Die erste Ammoniakproduktion erfolgte im Januar 2019. „Ehrlich gesagt hat uns überrascht, wie stabil die Prozesse laufen“, sagt Oles. Das Forschungsvorhaben läuft trotzdem noch bis 2020, denn am Ende sollen nicht möglichst viele wissenschaftliche Publikationen stehen, sondern ein wirtschaftliches Anlagenkonzept, das rasch weltweit zum Einsatz kommen kann. Anders formuliert: Da die aus dem Carbon2Chem-Verfahren gewonnenen Grundstoffe mit Erdöl- und Erdgasprodukten konkurrieren, muss es kostengünstig sein. Die bisherigen Ergebnisse zeigen aber bereits: Agieren Stahlhersteller und chemische Industrie gemeinsam, ist ein Optimum an Nachhaltigkeit und Wirtschaftlichkeit zu erreichen.
Dieser Beitrag stammt aus unserem Unternehmensmagazin „ESSENTIAL“, in dem wir kontinuierlich über Trends und Schwerpunktthemen aus unseren Zielindustrien und -märkten berichten. Weitere Beiträge des Magazins finden Sie hier.
Weitere Storys zum Thema Nachhaltigkeit
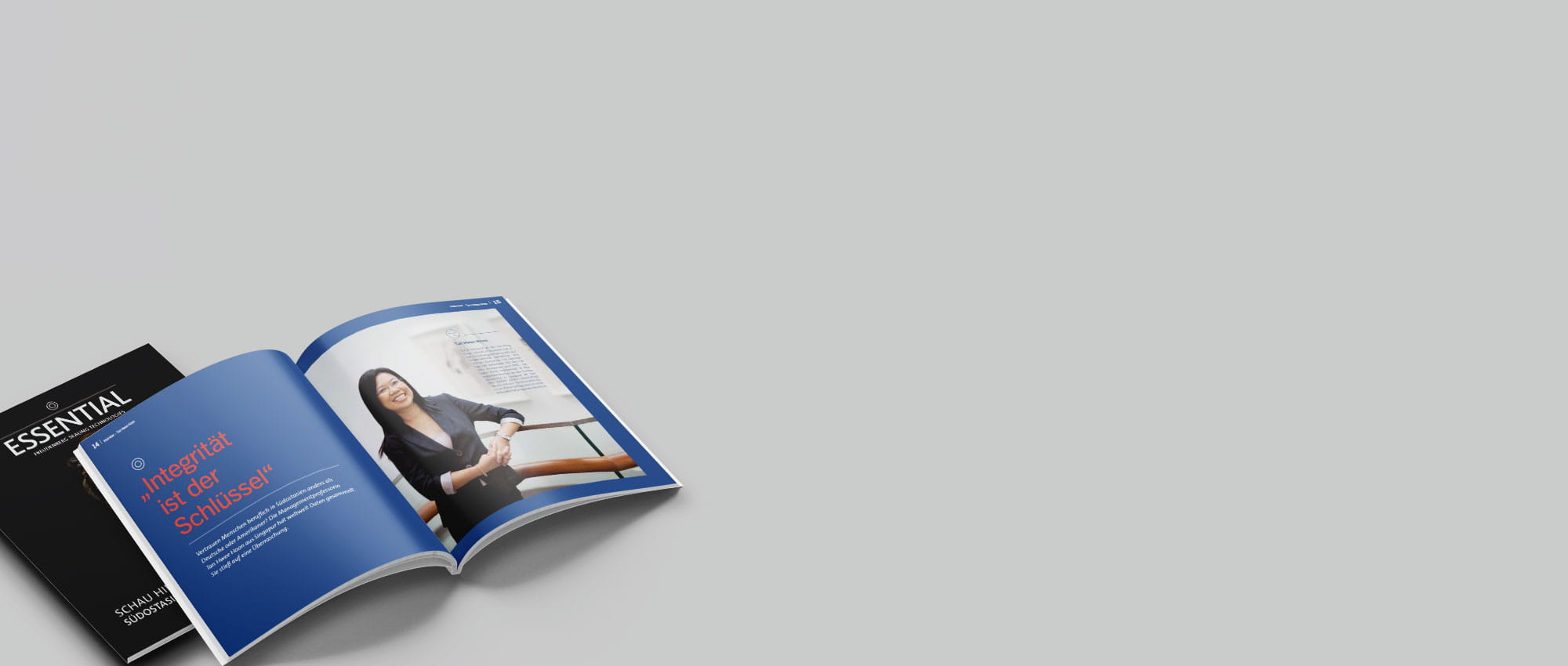