
GROWTTH Academy@Model.HeadlineTag.Tag>
Individual face-to-face GROWTTH training program.
Freudenberg Sealing Technologies is dedicated to improving the efficiency and effectiveness of its supply chain through an extensive Supplier Development Program. As a vital element of this initiative, the company provides a specialized GROWTTH ((Get Rid Of Waste Through Team Harmony)) Training Program to its suppliers. This program concentrates on instilling crucial lean principles and methodologies, aiming to optimize both production and administrative processes while minimizing waste. The training covers Lean Systems, Lean Administration, and Six Sigma. By investing in the skill development of its suppliers, Freudenberg Sealing Technologies seeks to promote a collaborative and streamlined supply chain, fostering mutual success and continuous improvement.
The GROWTTH Training Program includes three distinct topics: Lean Systems, Lean Admin., and Six Sigma. Each of these topics has different scopes and objectives, is scheduled separately, and is facilitated by highly trained and experienced experts.
Lean Systems
Black Belt
Objectives: Acquire skills in facilitating lean implementation projects, training employees through the Lean Systems Green Belt program, supporting lean policy deployment, coaching in core process improvement projects, and guiding the implementation of Lean Systems.
Target group: Employees responsible for advancing strategic improvements in manufacturing processes and implementing Lean Systems.
Time required: 12 to 24 months (including 13 weeks of in-person training and 18 kaizen projects).
Prerequisite: Anyone certified as a Lean Systems Green Belt or who has passed a LSGB exam is welcome to participate.
Throughout this training process, the cohort of trainees will have the opportunity to network and communicate with other employees from their respective facilities. Each candidate should be paired with a Lean Systems Green Belt training wave in their home facility to assist in implementing their various projects.
Lean Administration
Black Belt
Objectives: Acquire skills in facilitating lean implementation projects, training employees through the Lean Admin. Green Belt program, supporting lean policy deployment, coaching in core process improvement projects, and guiding the implementation of Lean Administration.
Target group: Employees responsible for advancing strategic improvements in administration processes and implementing Lean Admin.
Time needed: 12 to 24 months (including 9 weeks of in-person training).
Pre-requisite: None.
Throughout this training process, the cohort of trainees will have the opportunity to network and communicate with other employees from their respective facilities. Each candidate should be paired with a Lean Admin. Green Belt cohort in their home facility to assist in implementing their various projects.
Six Sigma
Black Belt
Objectives: Develop proficiency in facilitating Six Sigma projects, training employees through the Six Sigma Green Belt program, supporting lean policy deployment, and guiding the implementation of Six Sigma.
Target group: Employees responsible for advancing strategic improvements in operational processes and implementing Six Sigma.
Time required: 12 to 24 months (including 7 weeks of in-person training; participants need to allocate approximately 80% of their time to training and project work throughout the training process).
Pre-requisite: None.
Throughout this training process, the cohort of trainees will have opportunities to network and communicate with other employees from their respective facilities.
While participating in the GROWTTH Training Program, Freudenberg Sealing Technologies anticipates that suppliers will choose collaborative projects to promote mutual success and continuous improvement.
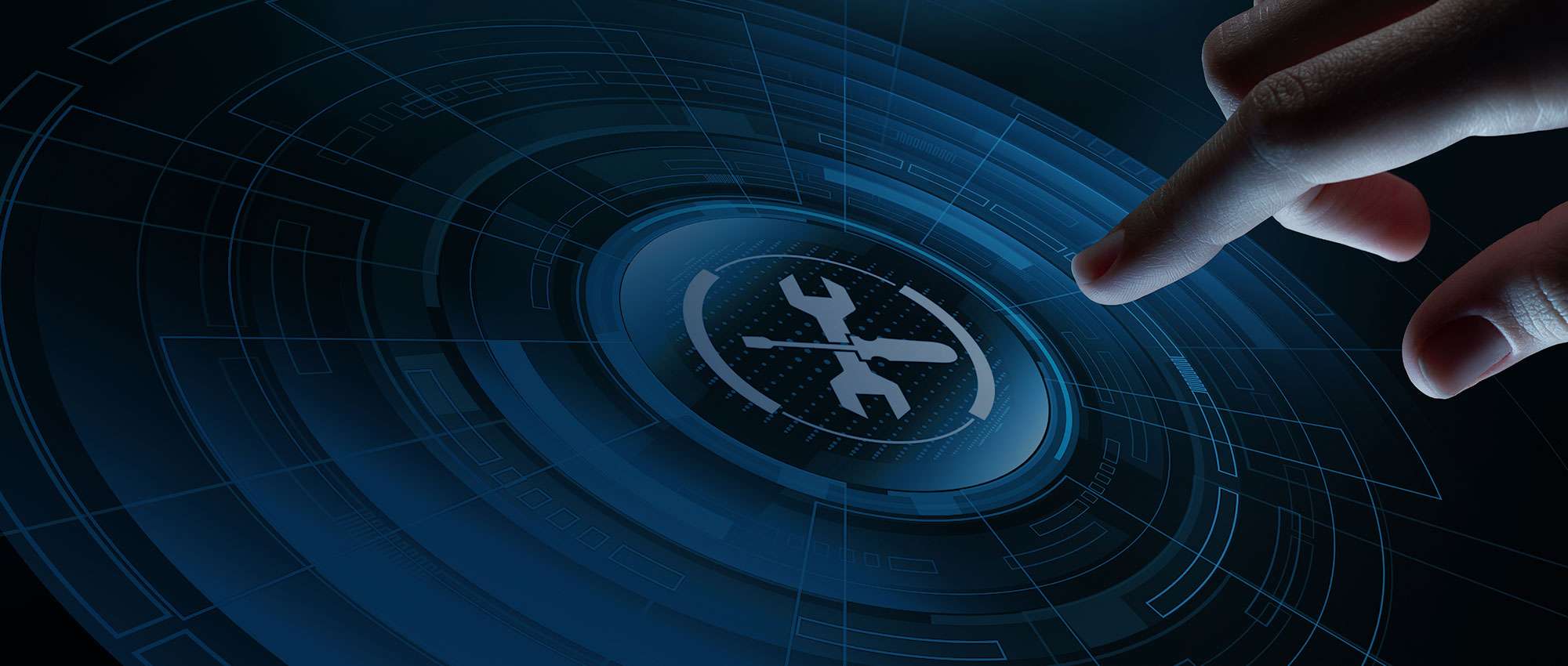
Services
Freudenberg Sealing Technologies offers a wide range of product-related services, logistics services and smart online tools for customers in the general, process and automotive industries to complement its comprehensive range of sealing solutions.
Learn more on fst.com